Key Takeaway: Types of Conveyor Belt Scrapers at a Glance
Type | Purpose | Material | Best For |
Primary Scraper | Removes bulk material at discharge points. | Polyurethane, Tungsten Carbide | General cleaning needs. |
Secondary Scraper | Cleans residual material after the primary. | Tungsten Carbide, Rubber | Fine cleaning and high precision. |
Return Belt Scraper | Cleans the underside of the belt. | Polyurethane | Underside debris removal. |
Brush Scraper | Rotating brushes for specialized cleaning. | Nylon, Polypropylene | Sticky or fine materials. |
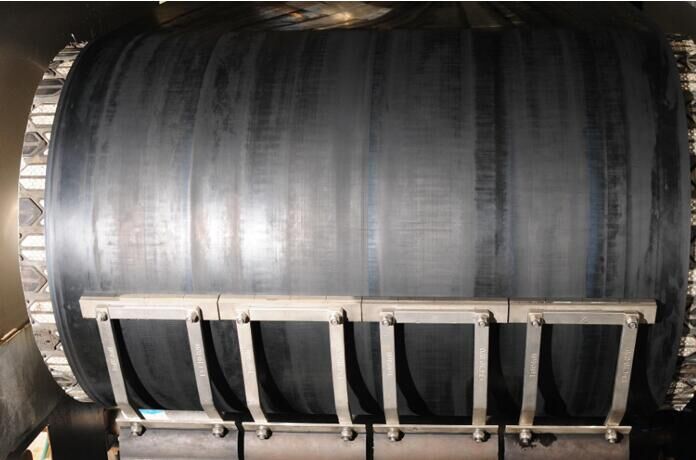
Why Are Conveyor Belt Scrapers Important?
Conveyor belt scrapers are indispensable in industrial operations. They reduce carryback, a common issue where leftover material sticks to the belt and falls off at unintended locations. Carryback wastes valuable material and causes operational inefficiencies, increased cleaning costs, and safety hazards.
Industry Insight: Research suggests that without proper scrapers, up to 3% of material can be lost daily due to carryback. This loss is particularly significant in industries like mining, where throughput is high.
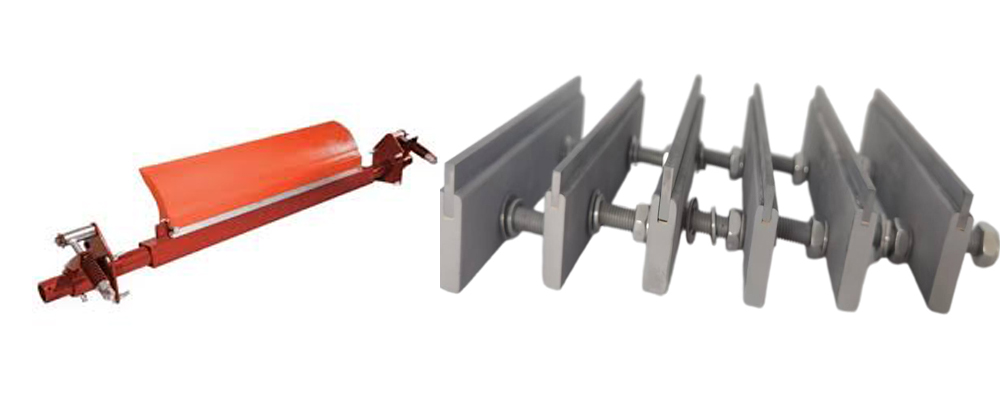
Types of Conveyor Belt Scrapers Explained
1. Primary Scrapers
- Purpose: Remove most of the material at the discharge point.
- Material Options: Polyurethane for flexibility; tungsten carbide for durability.
- Best For: Heavy-duty applications like mining or sand production.
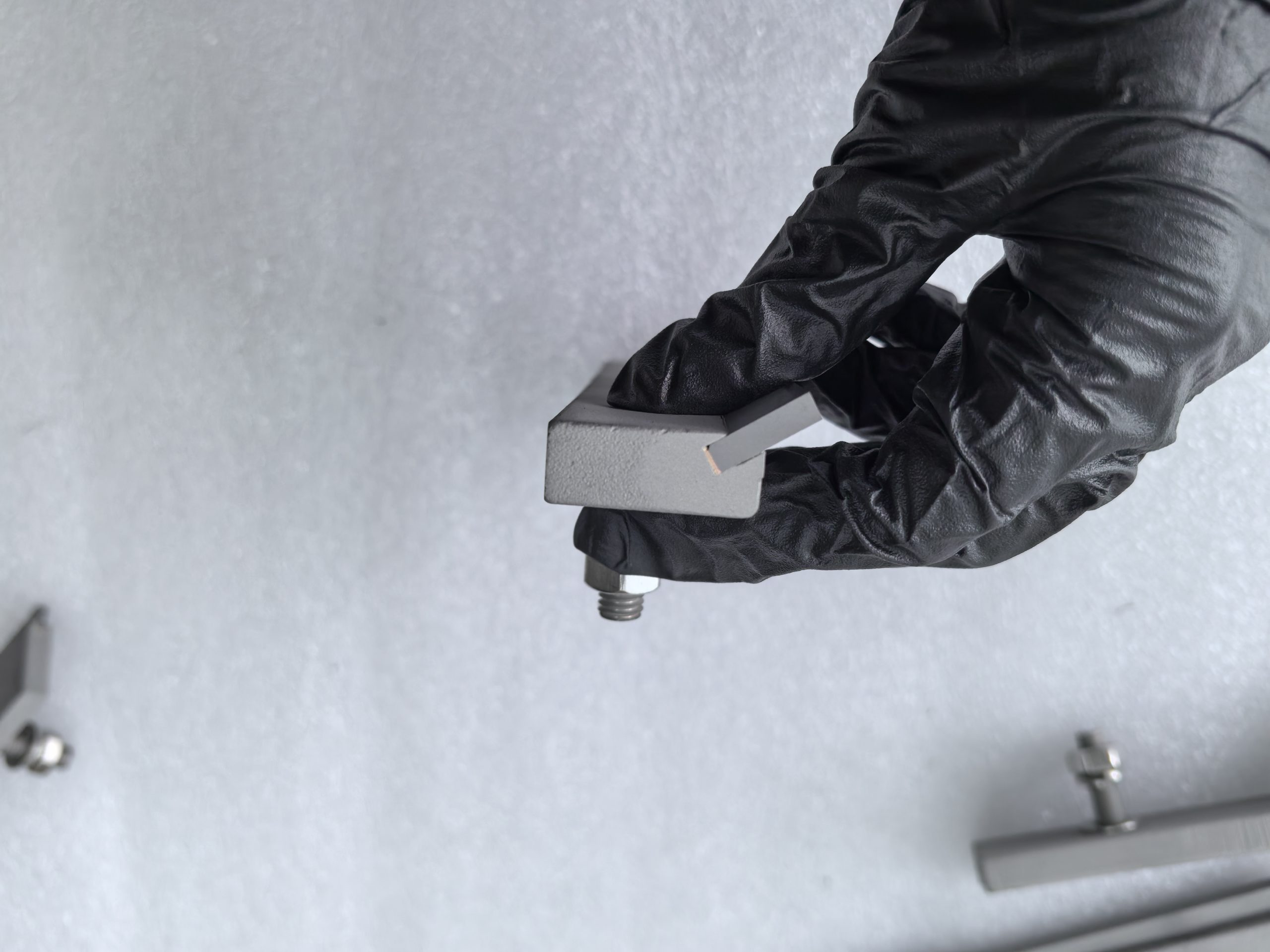
2. Secondary Scrapers
- Purpose: Handle residual material left by the primary scraper.
- Material Options: Rubber for softer cleaning; tungsten carbide for precision.
- Best For: Conveyor systems requiring high cleanliness levels.
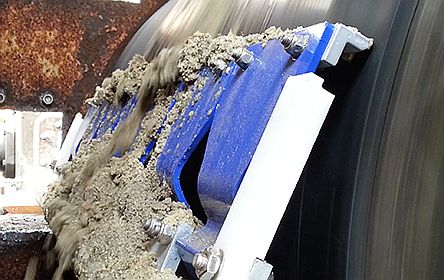
3. Return Belt Scrapers
- Purpose: Clean the underside of the conveyor belt.
- Material Options: Polyurethane.
- Best For: Preventing material build-up on the return rollers.
4. Brush Scrapers
- Purpose: Use rotating brushes for cleaning fine or sticky materials.
- Material Options: Nylon or polypropylene brushes.
- Best For: Applications like food processing and fine powder handling.

Choosing the Right Scraper for Your Conveyor System
When selecting a scraper, consider the following:
- Material Being Handled: Is it abrasive, sticky, or fine?
- Operating Environment: Is it wet, dry, or corrosive?
- Budget: Durable materials like tungsten carbide have a higher initial cost but longer lifespan.
Common Questions About Conveyor Belt Scrapers
- Q1: How Often Should Scrapers Be Inspected?
- Regular inspections should occur at least once a month to check for wear and alignment.
- Q2: Can I Combine Scraper Types?
- Yes, combining primary and secondary scrapers enhances cleaning efficiency.
- Q3: What’s the Lifespan of a Scraper?
- Tungsten carbide scrapers can last up to five times longer than polyurethane alternatives.
External Resources for Conveyor Maintenance
- Bulk Handling Systems Guide: Comprehensive insights on conveyor technologies.
- Mining.com: Articles on improving operational efficiency in material handling.
- Belt Cleaning Solutions: Expert advice on selecting and maintaining conveyor scrapers.
Conclusion: Upgrade Your Conveyor Efficiency with the Right Scrapers
Conveyor belt scrapers are vital for keeping operations efficient, clean, and cost-effective. Investing in high-quality scrapers, like those made from tungsten carbide, reduces downtime, enhances material recovery, and minimizes wear on your equipment.
At Zhuzhou OC Precision Alloy Co., Ltd., we specialize in producing durable and efficient tungsten carbide scrapers tailored to meet the needs of various industries. Whether you’re dealing with abrasive mining materials or fine powders, we have the solution for you.
Take Action Now!
Visit Our Product Page and explore our full range of scrapers. For tailored advice, contact our team today!