The rotor of the hammer crusher is one of the core components of the hammer crusher. It is mainly responsible for striking and impact crushing the materials entering the crushing chamber. The rotor is equipped with several hammers, which are usually made of high-hardness wear-resistant materials to withstand the high-intensity impact and wear of the materials.
When the material enters the crushing chamber of the hammer crusher, the high-speed rotating rotor drives the hammer to strike the material. The material is crushed under the impact of the hammer, and throws to the impact plate of the crushing chamber under the centrifugal force of the rotor, and is impacted and crushed again. This process is repeated until the material reaches the required particle size and is then discharged from the discharge port of the crusher.
This series of operations is very demanding on the wear resistance of the hammer. Therefore, choosing a hammer with the right material is crucial for the crusher and is the key to ensuring the performance of the crusher and extending its service life.
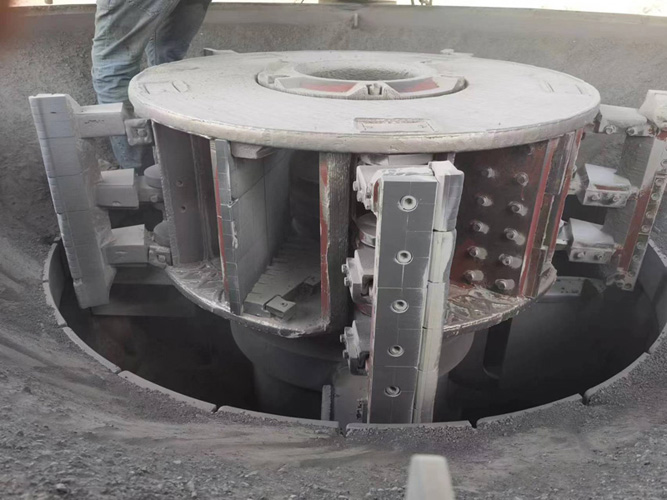
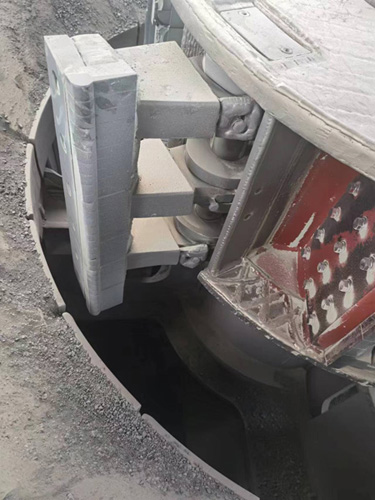
By understanding the advantages and disadvantages of the crusher, we can have a clearer
Advantages
- Large Crushing Ratio: Hammer crushers are capable of achieving a large crushing ratio, making them ideal for breaking medium-hard materials like limestone, coal, and gypsum. The use of durable hammers ensures continuous high-efficiency performance during the crushing process.
- Simple Structure: The rotor structure is relatively simple and easy to maintain. By using high-quality hammers, maintenance intervals are longer, reducing overall repair costs.
- Versatility: Hammer crushers can handle a wide range of materials, from ores and coal to construction waste and solid refuse. Using high-wear-resistant hammers allows the crusher to maintain stable performance when processing various materials.
Disadvantages
Hammer Wear: Despite the use of high-quality wear-resistant hammers, they are still subject to wear over time due to direct contact with the material. Regular replacement of hammers is necessary to maintain peak performance.
Through the above comparison, we can know that choosing a right and high-quality hammer is crucial for the crusher. Our company’s tungsten carbide hammer can solve this problem well.
Why Choose ZZ Old Craftsman Tungsten Carbide Hammers?
At ZZ Old Craftsman, we prioritize quality, precision, and performance. Our tungsten carbide hammers are tailored to meet the specific needs of your crushing operations, providing an optimal balance between durability, efficiency, and cost-effectiveness. With our hammers, you can expect higher productivity, reduced maintenance, and longer equipment life.
At ZZ Old Craftsman, our tungsten carbide hammers are specifically designed to enhance the performance and longevity of hammer crushers. The tungsten carbide material we use offers exceptional wear resistance and durability, making our hammers ideal for high-impact, high-abrasion environments. Here are the key advantages of our tungsten carbide hammers:
Safety and Reliability
The high durability of our tungsten carbide hammers minimizes the risk of unexpected failure, ensuring safer operation with fewer risks of equipment damage or downtime. This reliability contributes to smoother, more consistent crushing operations.
Outstanding Wear Resistance
Our tungsten carbide hammers are crafted from high-quality tungsten carbide, known for its extreme hardness and ability to withstand wear. This results in a significantly longer service life compared to conventional hammers made from materials like high-manganese steel, reducing the need for frequent replacements and maintenance.
Enhanced Crushing Efficiency
With superior hardness, our tungsten carbide hammers maintain their sharpness and cutting edge over extended periods of use. This ensures consistent crushing performance, improving efficiency by reducing energy consumption while delivering effective material reduction.
Optimal Performance in Tough Conditions
Our tungsten carbide hammers are engineered to handle the most demanding conditions. Whether you’re crushing hard rocks, ores, or other abrasive materials, our hammers can withstand the high-impact forces and extreme environments typically found in hammer crushers. Their resistance to deformation and cracking ensures reliable performance even under challenging operating conditions.
Cost-Effective Long-Term Solution
While tungsten carbide hammers represent an initial investment, their long-lasting durability and reduced need for maintenance make them a cost-effective choice in the long run. Fewer replacements and reduced downtime due to hammer failure result in lower overall operating costs.
High Thermal Stability
Tungsten carbide’s excellent thermal stability ensures that our hammers retain their strength and hardness even at elevated temperatures, making them perfect for high-speed operations or environments where material heat generation is significant.
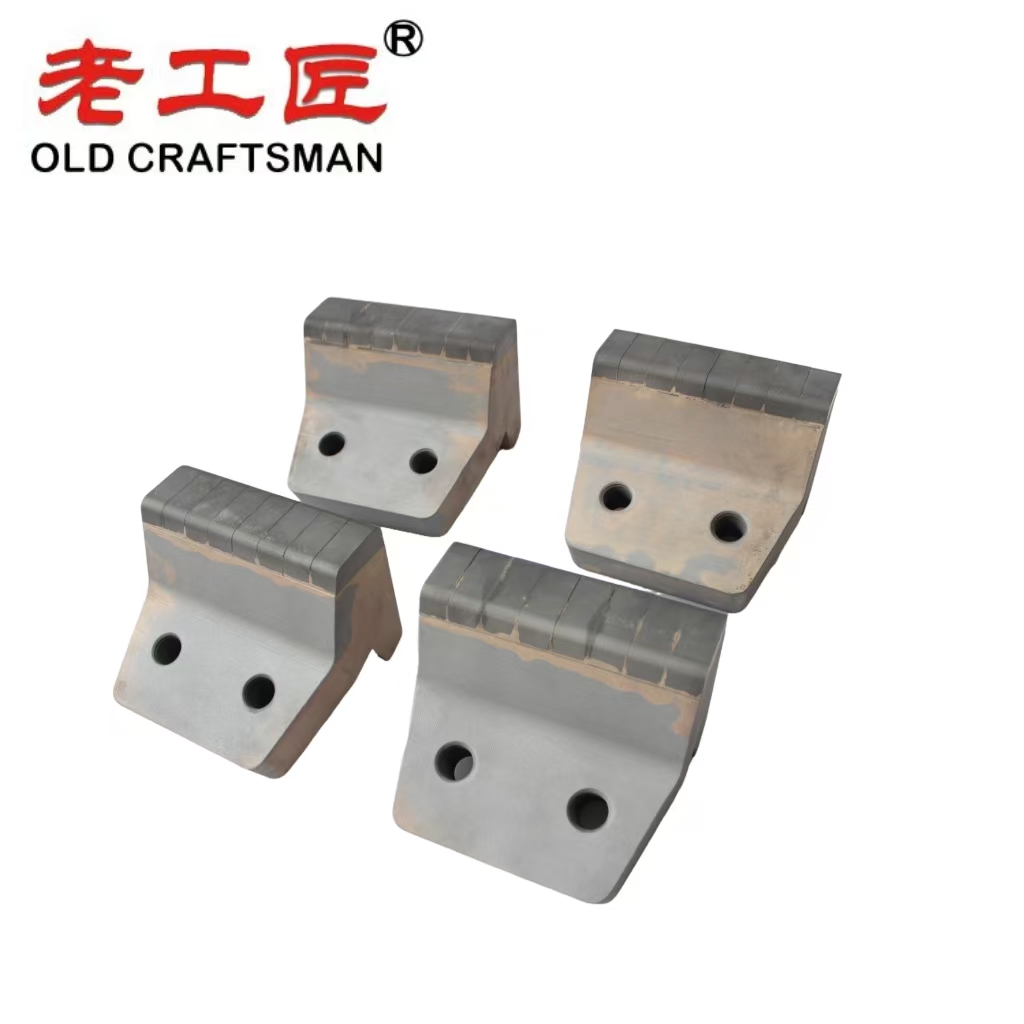
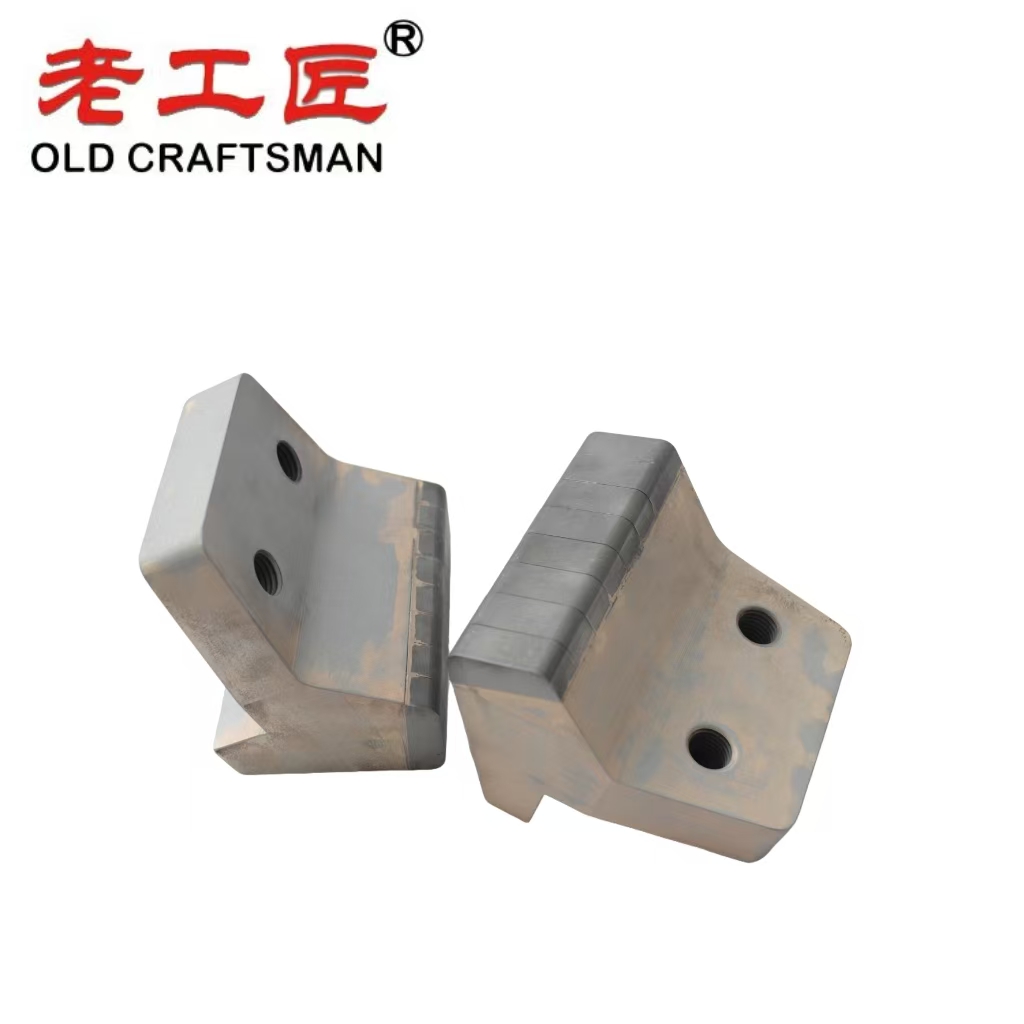
Related articles
Impact Crusher wear Liner Selection Guide: Why Tungsten Carbide is the Optimal Choice?