In the world of industrial crushing equipment, the efficiency, durability, and cost-effectiveness of components are critical to operational success. Among these components, the hammer head stands out as a vital part of a crusher, directly influencing its performance. In recent years, carbide hammer heads—made from hard alloys such as tungsten carbide—have gained widespread recognition for their exceptional practicality in various crushing applications. This article explores the key advantages of carbide hammer heads, their applications, and why they are a preferred choice in modern crusher designs.

✦ Superior Wear Resistance
One of the standout features of carbide hammer heads is their remarkable wear resistance. Crushers are often tasked with breaking down tough, abrasive materials like rocks, ores, and construction debris. Traditional hammer heads, typically made from steel or other softer alloys, tend to wear out quickly under such conditions, leading to frequent replacements and downtime. Carbide hammer heads, however, are engineered to withstand extreme abrasion and impact. The hardness of tungsten carbide, often combined with a tough metal binder like cobalt, ensures that these hammer heads maintain their shape and cutting edge for significantly longer periods. This durability translates into reduced maintenance costs and improved operational efficiency.
✦ Enhanced Crushing Efficiency
The design and material properties of carbide hammer heads contribute to their ability to crush materials more effectively. Their high hardness allows them to break down even the toughest materials with precision, resulting in a more uniform output. This is particularly beneficial in industries such as mining and cement production, where consistent particle size is essential for downstream processes. Additionally, the sharp, durable edges of carbide hammer heads reduce the energy required to fracture materials, optimizing the crusher’s overall power consumption. This efficiency not only lowers operational costs but also supports environmentally sustainable practices by reducing energy usage.
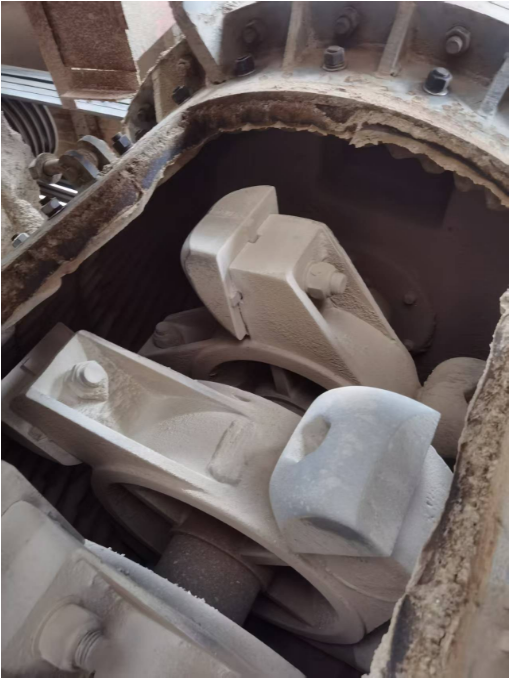
✦ Versatility Across Applications
Carbide hammer heads are highly versatile, making them suitable for a wide range of crushing tasks. Whether it’s primary crushing of large rocks or secondary crushing of finer aggregates, these hammer heads adapt well to different material types and hardness levels. They are commonly used in hammer crushers, impact crushers, and shredders across industries like mining, quarrying, recycling, and metallurgy. For example, in the recycling sector, carbide hammer heads excel at processing reinforced concrete and scrap metal, where their resistance to wear and fracture is put to the test. This adaptability makes them a practical choice for businesses looking to streamline equipment use across multiple applications
✦ Cost-Effectiveness Over Time
While carbide hammer heads may have a higher upfront cost compared to traditional steel alternatives, their long-term cost-effectiveness is undeniable. The extended service life reduces the frequency of replacements, minimizing downtime and labor expenses associated with maintenance. Furthermore, their consistent performance eliminates the need for frequent adjustments or repairs to the crusher itself, ensuring steady productivity. For industries operating on tight margins, this balance of initial investment and long-term savings makes carbide hammer heads an economically sound choice.
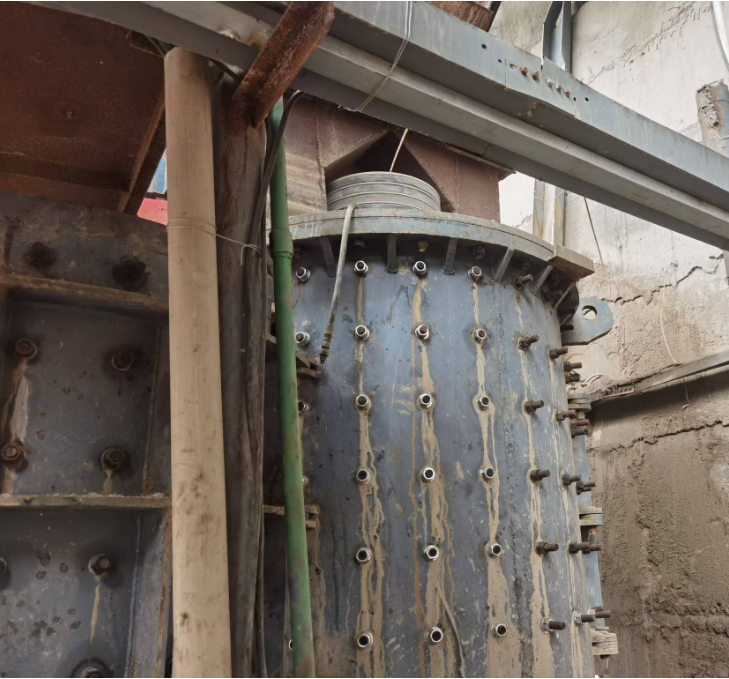
✦ Challenges and Considerations
Despite their many advantages, carbide hammer heads are not without challenges. Their brittleness, a trade-off for their hardness, can make them susceptible to cracking under extreme impact or improper use. To mitigate this, manufacturers often design them with a composite structure, embedding carbide tips into a tougher base material. Proper crusher settings and regular inspections are also essential to maximize their lifespan. Operators must weigh these factors against the specific demands of their application to ensure optimal performance.
✦ Conclusion
The practicality of carbide hammer heads in crushers lies in their unmatched durability, efficiency, and versatility. By offering superior wear resistance, enhanced crushing performance, and long-term cost savings, they have become a cornerstone of modern crushing technology. While they require careful handling and an initial investment, their benefits far outweigh the drawbacks for industries that rely on consistent, high-quality material processing. As crusher designs continue to evolve, carbide hammer heads are likely to remain a key innovation, driving productivity and sustainability in material processing worldwide.
“Zhuzhou Old Craftsman Precision Alloy Co., Ltd. could make tungsten carbide crusher hammer and make your crusher hammer use life is tens of times longer than before! We specialize in providing customized carbide solutions to meet the demanding requirements of industries such as aerospace, automotive, mining, and precision machining.”