Mining is a cornerstone of industrial development, providing essential raw materials for construction, manufacturing, and energy production. However, the harsh conditions of mining environments—such as abrasive rock surfaces, high pressures, and extreme temperatures—pose significant challenges to the durability and efficiency of mining tools. One of the most critical issues faced by the industry is tool wear, which reduces operational efficiency, increases downtime, and raises maintenance costs. To address this, cemented carbide, a composite material known for its exceptional hardness and wear resistance, has become a key solution in enhancing the lifespan and performance of mining tools. This essay explores the role of mining tools, the wear challenges they face, and how cemented carbide provides effective wear protection.
The Role of Mining Tools
Mining tools encompass a wide range of equipment, including drill bits, cutting picks, crusher components, and conveyor systems, all of which are designed to extract, process, and transport minerals from the earth. These tools are subjected to constant mechanical stress, friction, and impact as they interact with hard geological formations like granite, quartz, and limestone. For example, rotary drill bits used in underground mining must penetrate dense rock layers, while conveyor belts and crusher jaws handle the abrasive forces of ore processing. The efficiency of these tools directly impacts the productivity of mining operations, making their durability a top priority.
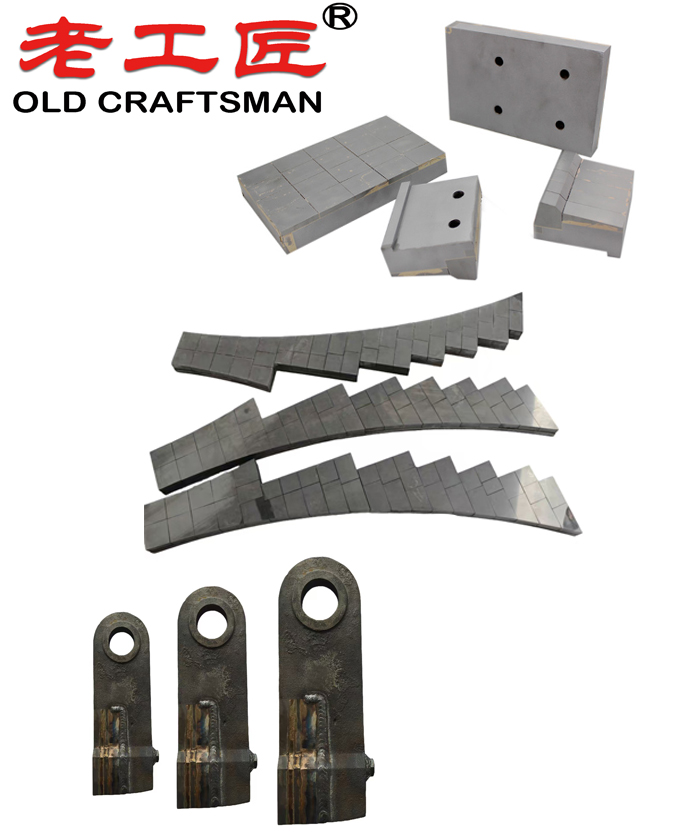
Wear Challenges in Mining Tools
Wear in mining tools occurs through several mechanisms: abrasion, impact, erosion, and corrosion. Abrasion, caused by the constant rubbing of tool surfaces against hard mineral particles, is the most common form of wear. Impact wear results from high-force collisions, such as those experienced by hammer drills or rock breakers. Erosion occurs when fine particles or slurries degrade tool surfaces over time, while corrosion can weaken tools in wet or chemically aggressive environments. These wear mechanisms lead to material loss, deformation, or cracking, ultimately shortening tool life and necessitating frequent replacements. In addition to economic losses, excessive wear can compromise safety and environmental sustainability by increasing energy consumption and waste.
Cemented Carbide: One Of Wear Protection Solution
Cemented carbide, also known as tungsten carbide (WC) bonded with a metallic binder like cobalt (Co), offers an advanced solution to combat wear in mining tools. This material combines the extreme hardness of tungsten carbide particles with the toughness of the cobalt matrix, resulting in a composite that excels in both wear resistance and fracture toughness. The unique properties of cemented carbide make it ideal for applications where tools must withstand abrasive and high-impact conditions.
In practice, cemented carbide is applied to mining tools through various methods, such as cladding, coating, or manufacturing entire tool components from the material. For instance, drill bits tipped with cemented carbide inserts can penetrate harder rock formations with less wear compared to traditional steel bits. Similarly, cutting picks and crusher teeth reinforced with cemented carbide maintain their sharpness and structural integrity over extended periods, reducing the frequency of replacements. The versatility of cemented carbide also allows it to be tailored to specific mining conditions by adjusting the grain size of tungsten carbide or the binder content, optimizing the balance between hardness and toughness.
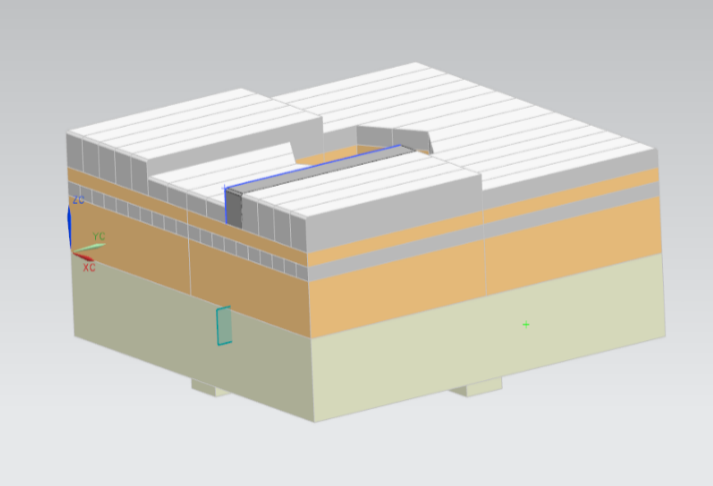
Advantages and Innovations
The use of cemented carbide in mining tools provides several advantages. First, it significantly extends tool life, reducing downtime and maintenance costs. Second, it enhances cutting and drilling efficiency, enabling faster extraction rates and lower energy consumption. Third, it contributes to sustainability by minimizing material waste and the need for frequent tool production. Recent innovations in cemented carbide technology, such as the development of nanostructured carbides and advanced coating techniques (e.g., physical vapor deposition), have further improved wear resistance and thermal stability, making these materials even more effective in extreme mining environments.
Challenges and Future Directions
Despite its benefits, cemented carbide is not without challenges. The high cost of tungsten and cobalt, coupled with supply chain vulnerabilities, can limit its widespread adoption. Additionally, while cemented carbide excels in hardness, it may still fail under extreme impact or fatigue conditions, necessitating complementary designs like shock-absorbing tool geometries. Looking forward, research is focusing on alternative binders (e.g., nickel or iron) to reduce reliance on cobalt, as well as recycling programs to recover tungsten from worn-out tools. These advancements promise to make cemented carbide solutions more cost-effective and environmentally friendly.
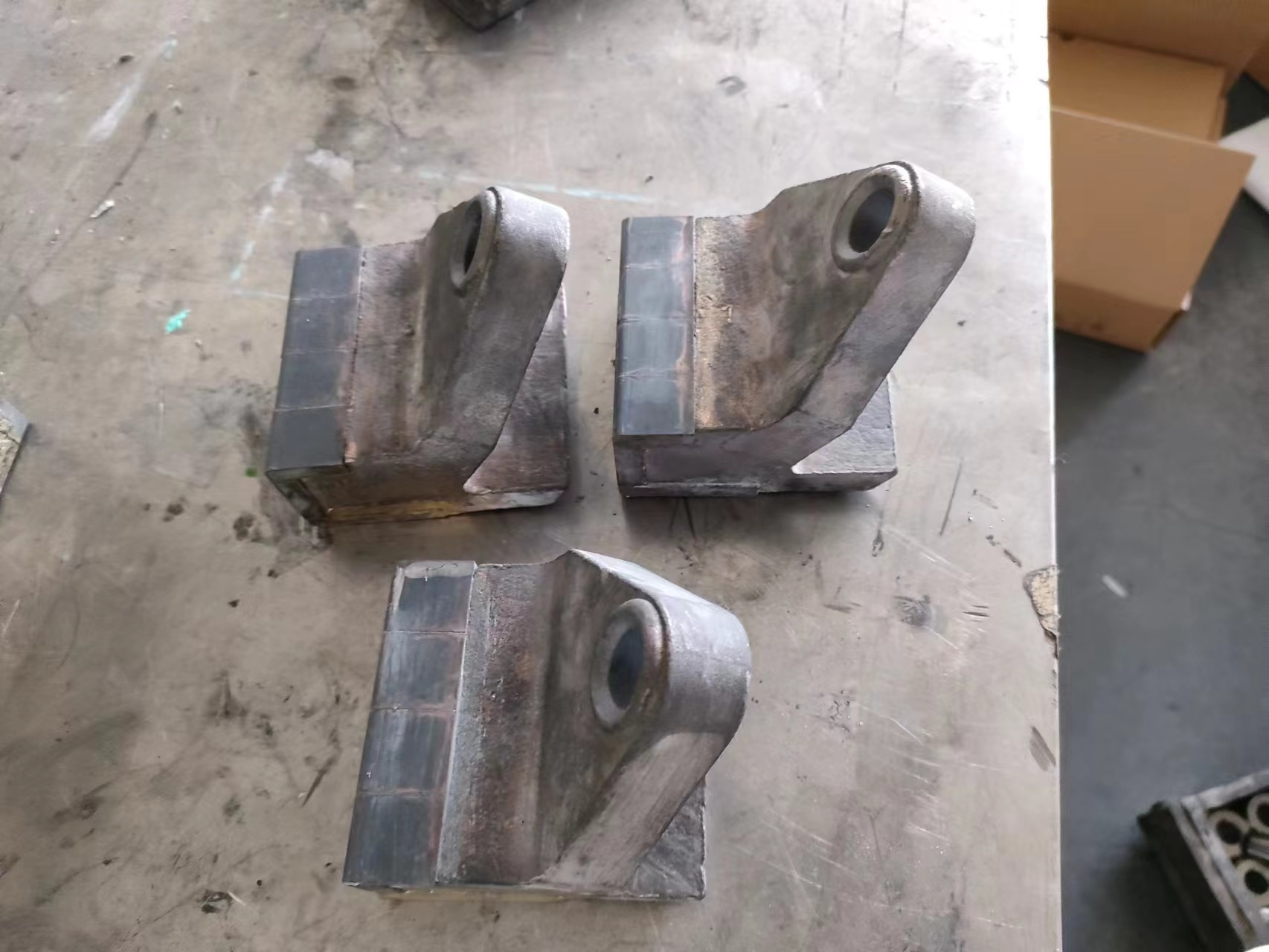
Conclusion
Mining tools are the backbone of the mining industry, and their ability to withstand wear is critical to operational success. Cemented carbide has emerged as a transformative material in wear protection, offering unmatched hardness, toughness, and adaptability to the demanding conditions of mining. By integrating cemented carbide into tool design and embracing ongoing innovations, the industry can achieve greater efficiency, safety, and sustainability. As challenges like cost and material availability are addressed, cemented carbide will continue to play a pivotal role in shaping the future of mining technology.
“Zhuzhou Old Craftsman Precision Alloy Co., Ltd. could make tungsten carbide crusher hammer and make your crusher hammer use life is tens of times longer than before! We specialize in providing customized carbide solutions to meet the demanding requirements of industries such as aerospace, automotive, mining, and precision machining.”
Blet scarper Brazing brazingprocess CARBDIE HAMMER carbide Carbide belt scraper carbidebrazing carbide hammer Crusher CRUSHER HAMMER Informational Internal stress metal mining mold operate Refractory Brick Mold Secondary belt cleaner scraper stresses VSI VSI crusher wear plates welding work