Tungsten carbide wear parts are critical in mining crushers due to their exceptional hardness, wear resistance, and durability, which significantly extend the lifespan of machinery under harsh conditions. These parts are used in various crusher components, including:
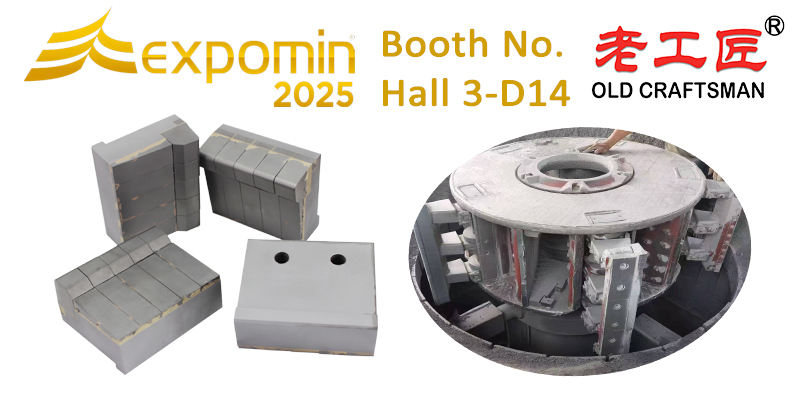
Jaw Crusher Plates: Tungsten carbide plates outperform traditional high manganese steel, offering several times longer service life, even with materials up to 7-8 Mohs’ hardness. They resist strong impacts and abrasive wear, reducing downtime and maintenance costs.
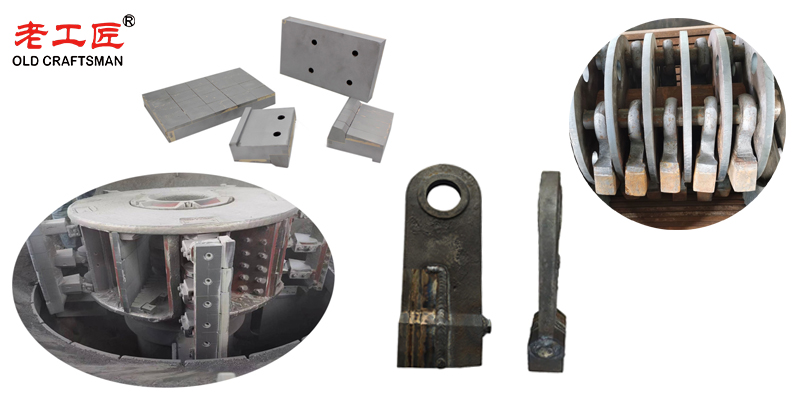
Hammers and Grinding Rolls: These parts withstand high stress and abrasive materials, maintaining their shape and cutting edges for extended periods. This durability ensures smoother crushing operations and fewer replacements.
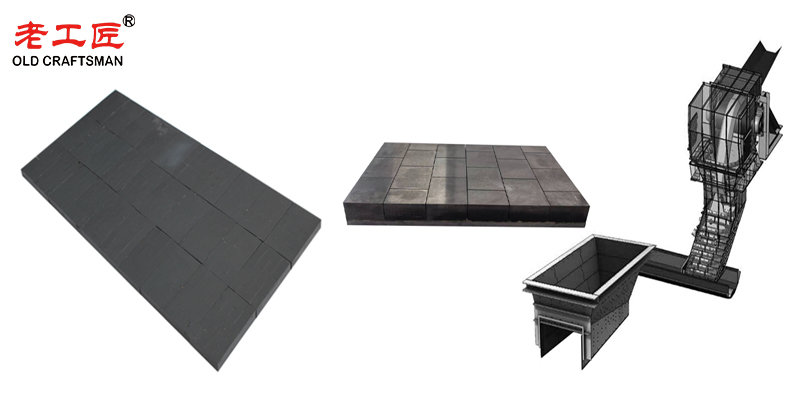
Rotor Tips and Wear Plates: Used in Vertical Shaft Impactor (VSI) crushers, tungsten carbide rotor tips and plates provide high wear resistance, ensuring consistent performance in sand-making or coal mining applications.
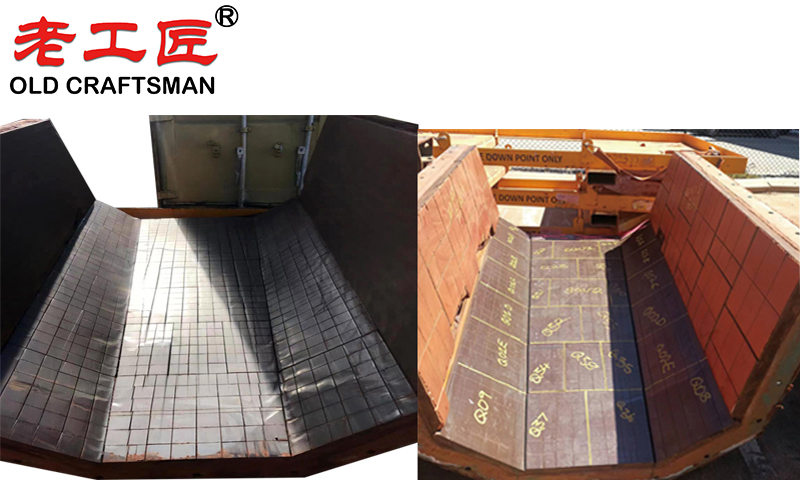
Conveyor Components: Tungsten carbide wear parts for idlers and pulleys resist abrasion from transported materials, enhancing conveyor longevity and reliability.
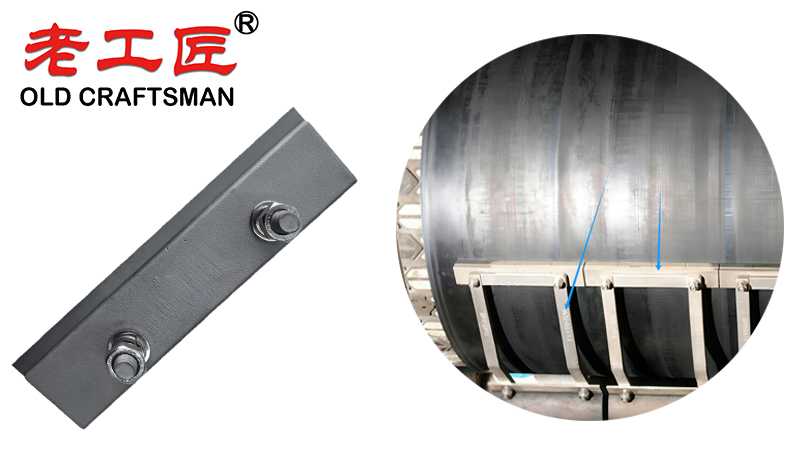
Key Properties:
✦ Hardness: Tungsten carbide has a Rockwell Hardness (HRA) of 89+, making it nearly as hard as diamond, ideal for crushing tough materials.
✦ Wear and Impact Resistance: Its unique combination of hardness and toughness allows it to endure high-impact and abrasive environments without significant wear.
✦ Corrosion Resistance: Suitable for corrosive mining environments, reducing degradation over time.
Benefits:
Extended Lifespan: Parts last 3-10 times longer than standard materials, reducing replacement frequency.
Cost Efficiency: Lower maintenance and downtime costs improve operational efficiency.
Customizability: Parts can be tailored to specific crusher needs, ensuring optimal performance.
Applications:
Commonly used in jaw crushers, cone crushers, VSI crushers, and hammermills across mining, aggregate, and coal industries.
Specific uses include crushing hard materials like diamond ferroalloy, cemented carbide, and ferro-manganese.
For lubrication, manufacturers recommend specific greases to minimize friction and wear, ensuring compatibility with tungsten carbide. Leading suppliers like Miller Carbide, KoneCarbide, and Unicast offer customized solutions, with innovations like Unicast’s “Wolf Technology” enhancing durability.
Looking Forward to EXPOMIN 2025
EXPOMIN 2025 is a fantastic opportunity for us to connect with the mining community, share our expertise, and explore new partnerships. We are particularly excited to engage with clients and partners in Chile, a country at the forefront of the global mining industry. Join us in Santiago to discover how ZZ OLD CRAFTSMAN can help you achieve greater efficiency, sustainability, and profitability in your mining operations.
Stay tuned for more updates as we prepare for EXPOMIN 2025. Follow us on ZZ OLD CRAFTSMAN Social Media Links, for the latest news and insights from our team. We can’t wait to see you in Santiago!
Blet scarper Brazing brazingprocess CARBDIE HAMMER carbide Carbide belt scraper carbidebrazing carbide hammer Crusher CRUSHER HAMMER Informational Internal stress metal mining mold operate Refractory Brick Mold Secondary belt cleaner scraper stresses VSI VSI crusher wear plates welding work