ZZ OLD CRAFTSMAN’s carbide brazed chute Liners and skirt Liners are designed to be an integral part of a conveyor system. Our pre-engineered chute lining protects and cushions the chute from the material being handled; Skirt Liners prevents fugitive materials from escaping and damaging the conveyor loading areas. The carbide brazed chute liners are mainly used instead of the chrome wear plates and ceramic liners in harsh environments, such as high temperature, low cold, and high impact. It is suitable for wear-resistant protection for equipment that works with large transport volumes, big-size materials, and extreme impact conditions, and can be used in the mining of iron ore, coal, lithium, uranium, and basalt. The thickness of the carbide can be from 6-22mm and the backing plates’ thickness also can be 6-35mm.

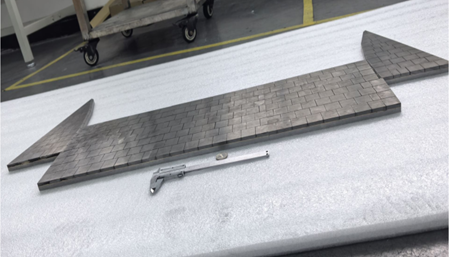
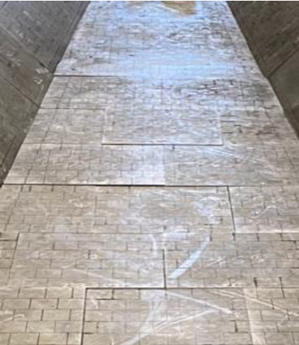
Advantages of carbide chute liner
Combining the right liner with the correct chute design improves overall system efficiency and maximizes material transfer, promoting efficient flow, dust suppression, and reduced buildup inside the chute. The carbide brazed liners produced by ZZ OLD CRAFTSMAN have the following advantages:
1. Because of the good hardness of the carbide, we can reduce the liner’s total thickness from 63mm to 26mm, which increases the loading volume of the chute invisibly, increasing ore flow in the unit time.
2. Because of the good impact of the carbide, the use life of the carbide brazed liners is much extended, according to our customer’s feedback, the use life of 20mm carbide on 6mm backing plates for iron ore chutes can be last more than 2 years, greatly reduced shutdown time, replacement cost, reduced the labor intensity of miners. At the same time, the working efficiency increased.
3. Compared to the vulcanized, we do not need to consider the aging of the bonding material, and the application range is much larger. No need to worry about the bonding strength even the liners used for more than two years.
4. ZZ OLD CRAFTSMAN is strong at customized design. We can recommend proper carbide grade and thickness according to different use conditions. We support sample testing, and middle batch testing to bulk production, we can adjust the carbide parameter and brazing technique according to the onsite testing result until the product reaches the best cost performance.
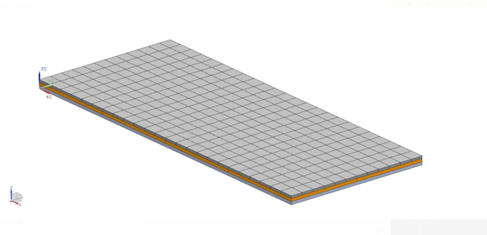
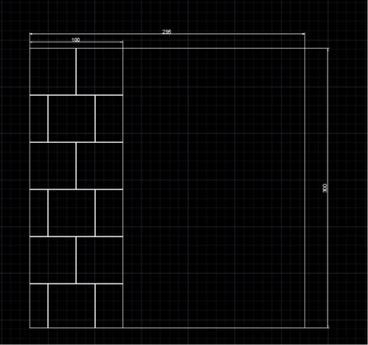
Application:
1. Used for transfer chute and transfer tower: Choosing different carbide thicknesses, our brazed liners can be used on the chute after the first crusher, second crusher, third crusher, and so on.
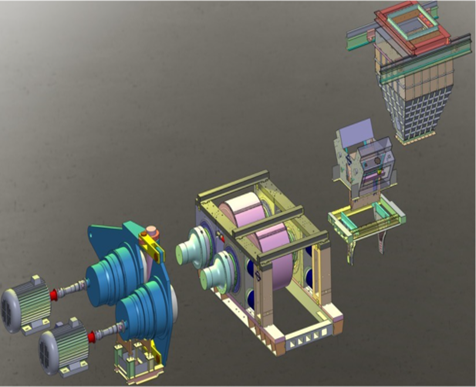
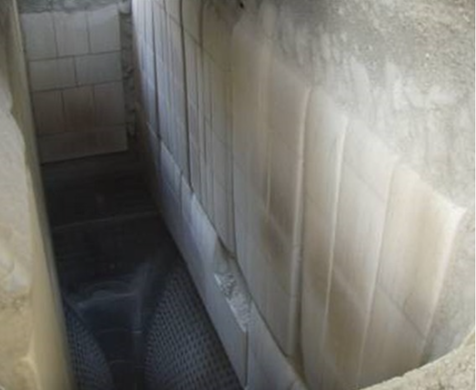
2. Used as conveyor shirt liner. Use different carbide thicknesses according to the wear status to avoid material waste.
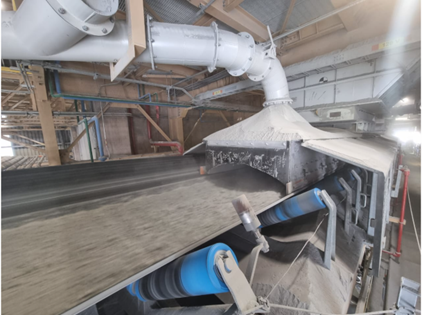
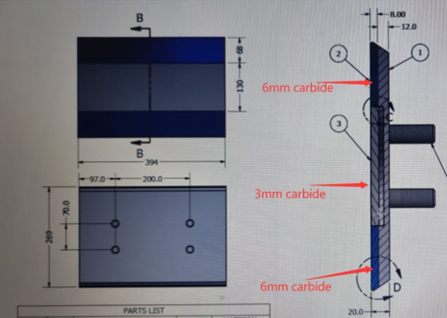
3. Used for hopper.
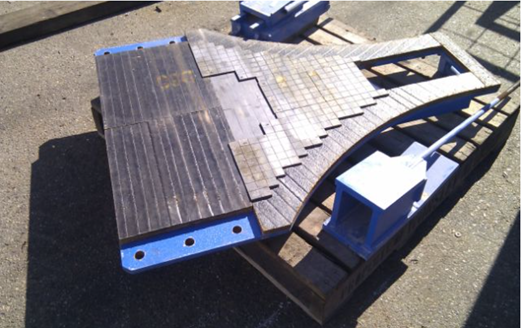
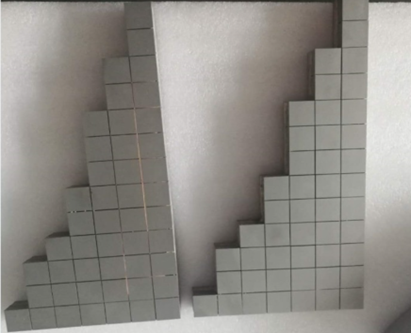
Vacuum brazing advantages:
1. High brazing strength: Vacuum brazing can maintain a stable heating temperature. Relying on the wetting and capillary action of the solder, the joint gap produced by the weldment is small, resulting in stronger brazing strength, which can exceed 200Mpa.
2. Low heat-affected zone: During the vacuum brazing process, due to no oxygen and impurities, the heat conduction effect is small and the workpiece is less heated, thereby reducing the heat-affected zone, reducing thermal deformation and stress of the workpiece, helping to maintain the workpiece Original properties and shape.
3. Neat welds: There is no oxygen and impurities in the vacuum brazing process, and defects such as bubbles and inclusions will not occur. The welds are usually tidy and have high appearance quality and welding strength.
4. Eco-friendly: There is no waste gas emission during the vacuum brazing process, causing little environmental pollution. There is no need to use harmful welding flux or coating, and it meets ecological requirements. In addition, vacuum brazing has no open flames or smoke, and the operation risk is low.
Company Introduction:
Zhuzhou Old Craftsman Precision Alloy Co., Ltd, established in 2014, is a tungsten carbide manufacturer that provides professional research and development, production, sales, and technical services.
The Company upholds its “craftsman spirit” by exploring the traditional process of cemented carbide sublimation, as well as new materials, new technology, the application of new methods.
We have a variety of modern first-class tungsten carbide production equipment, such as powder-mixing line, mold forming, injection, CNC machining, HIP sintering, vacuum welding, CNC grinding, EDM and so on. The Company’s complete testing equipment enables each product to strictly undergo performance, metallographic and visual inspections before it leaves the factory.
Our products are primarily utilized in demanding conditions requiring resistance to impact and wear, such as in the mining, sand and gravel crushing, and solid waste processing industries. We provide tailored solutions for our clients.
We have obtained ISO9001 quality management system certification and was recognized as a “National High-Tech Enterprise” in 2018.
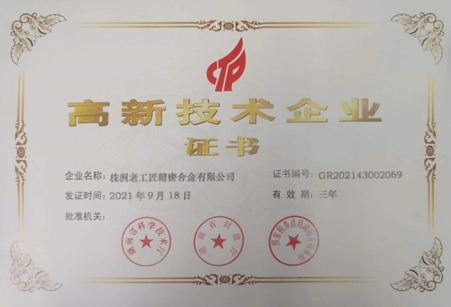
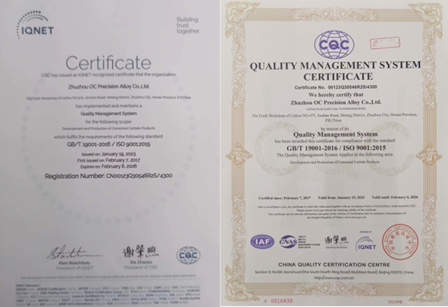
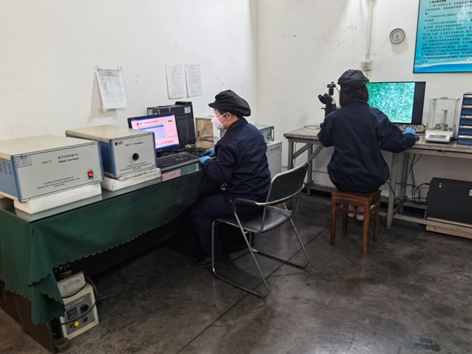
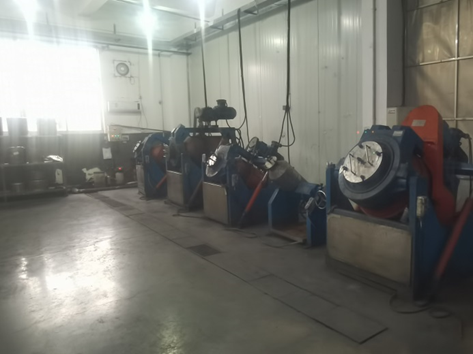
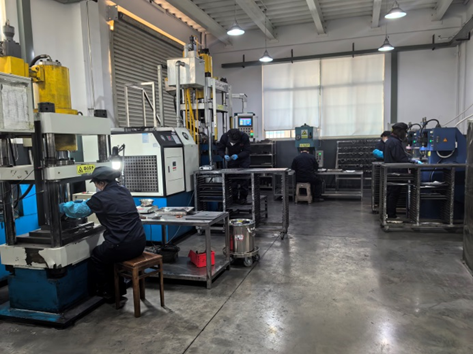
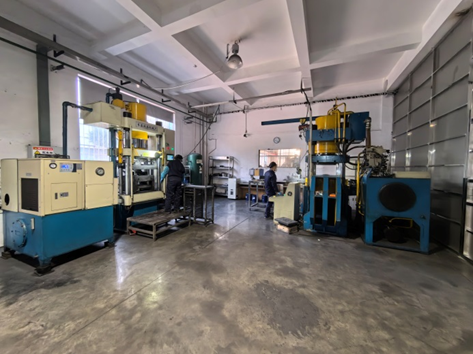
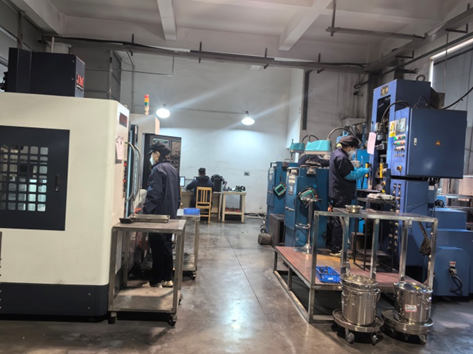
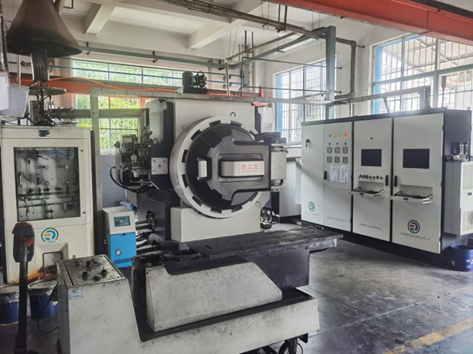

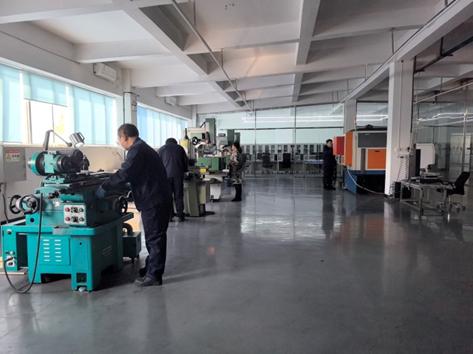
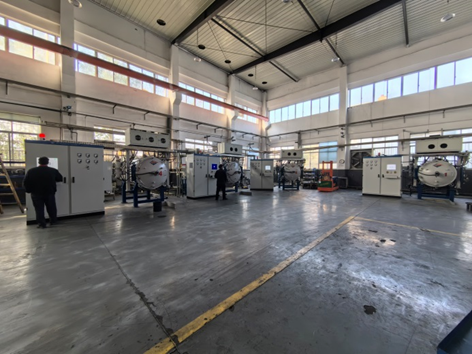
Other Carbide Brazed Products We Are Producing:
Refractory Brick Molds:
Our molds, comprising small diamond and trapezoid pieces welded onto steel plates, require assembly and withstand pressures up to 2000 tons. A decade of experimentation, collaboration with clients, and continuous refinement of alloy grades and processes have positioned us as one of the few global companies capable of producing high-quality molds.
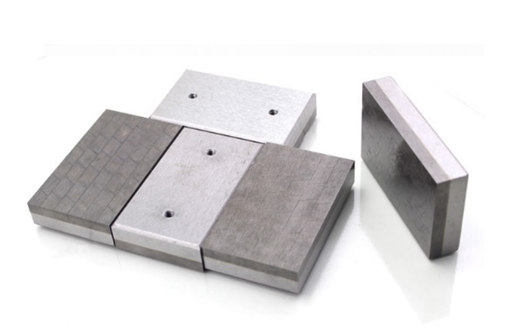
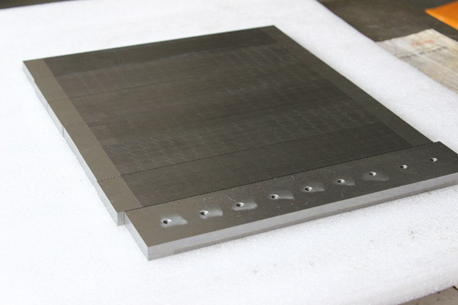
Mixer Blades:
Utilized in various industries for wear-resistant components in mixing equipment, our blades undergo detailed discussions with clients to determine design solutions, custom alloy grades, and welding processes. The stirring blades used for refractory brick materials have received positive feedback from customers, saving them replacement costs, solutions, custom alloy grades, and welding processes. The stirring blades used for refractory brick materials have received positive feedback from customers.
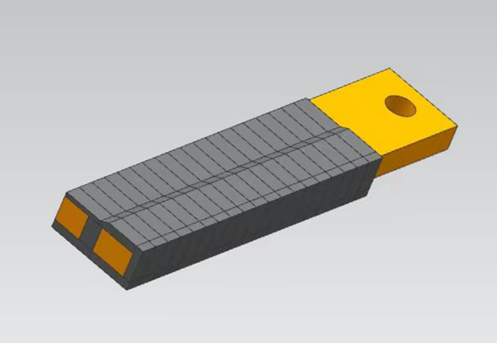
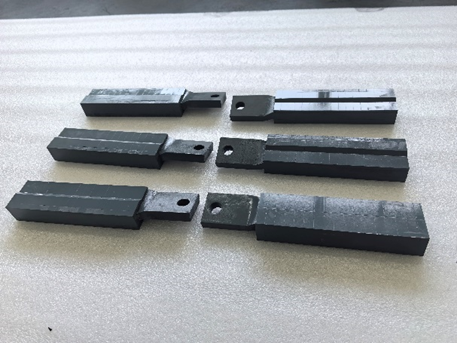
Sand Making Machine Hammer Heads, Acceleration Blocks, Installation Bases:
Tailoring welding processes and hard alloy grades based on different sand particle sizes, compositions, and abrasiveness, we have developed specific solutions for different sand pits. This has helped clients improve production efficiency and reduce production costs.
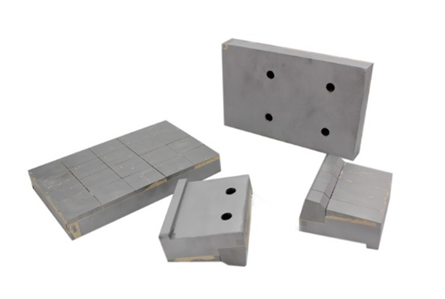
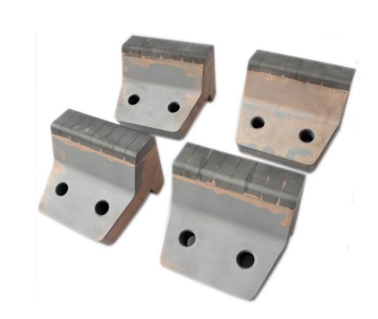
Scraper:
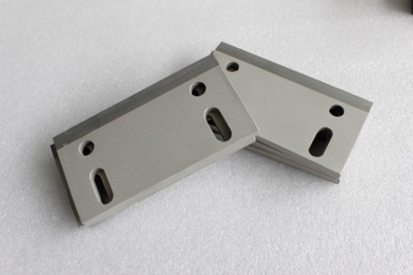
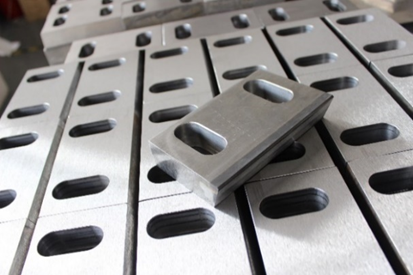