Content
- Introduction
- What does a VSI crusher undertake?
- What is the speed of VSI crusher?
- What is the process of a VSI crusher?
- How does a VSI crusher operate?
- Conclusion
Introduction
VSI crushers, renowned as Vertical Shaft Impact crushers, stand as indispensable equipment within the crushing industry. These crushers bear pivotal importance in the reduction of mammoth rocks into smaller, more manageable particles, rendering them suitable for multifarious applications spanning construction, mining, and industrial domains. With a design and functionality that exudes uniqueness, VSI crushers establish themselves as exceptionally proficient and versatile machinery, engendering top-tier aggregates and meticulously shaping the final product. Within the confines of this article, we embark on an exploration of the inner workings of VSI crushers, focusing acutely on the pivotal components and mechanisms that underlie their capacity to deliver an unparalleled crushing performance. Gaining an understanding of the intricacies within the realm of VSI crushers unravels profound insights into the crushing process and the momentous role these machines assume in the broader landscape of mining and construction. Now, let us delve into the captivating realm of VSI crushers, where the secrets behind their resounding success await our unearthing.
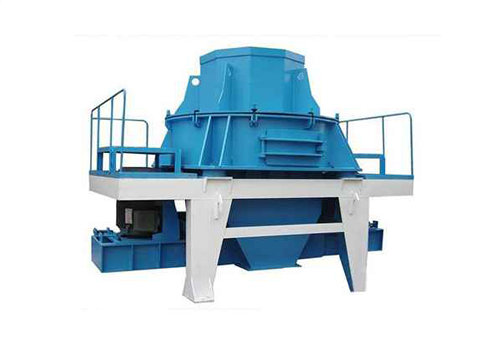
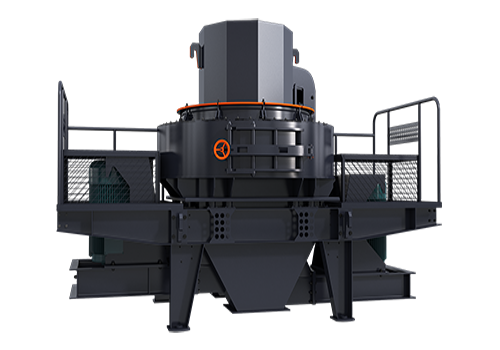
What precisely does a VSI crusher undertake?
At its core, a VSI crusher, an abbreviated rendition of the Vertical Shaft Impact crusher, shoulders the primary responsibility of transforming colossal rocks into diminutive particles that exude a sense of uniformity. Its modus operandi revolves around the principle of delivering high-velocity impacts to dismantle the material and craft exquisitely crushed aggregates. Discern below the intricate process by which a VSI crusher accomplishes this endeavor:
Diminishing rock dimensions: The primary objective of a VSI crusher centers around the ingestion of substantial rocks and the subsequent fragmentation into smaller fragments. This operation transpires by channeling the rocks into the epicenter of a revolving rotor, which propels them towards the anvils or walls of the crushing chamber.
Impact-induced fragmentation: As the rocks encounter the anvils or walls, a collision of immense speed ensues. These high-velocity impacts fracture the rocks, causing them to splinter and rupture. The resultant fragments, diminished in size, undergo a crushing process that bequeaths them with a newfound uniformity, rendering them suitable for a myriad of applications.
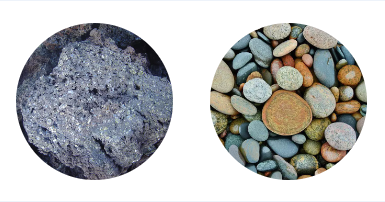
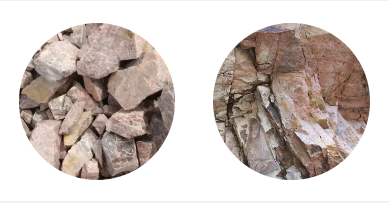
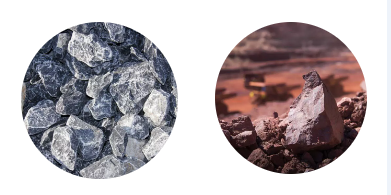
The pivotal role of VSI crusher rotor tips:
Within the heart of a VSI crusher resides a critical component, known as the rotor, which comprises a central main shaft alongside an array of rotor tips. These rotor tips, alternatively referred to as wear parts or anvils, bear substantial significance in the process of crushing. Observe how they substantively contribute:
Direct impact prowess: The rotor tips are purposefully crafted to endure the high-velocity impacts emanating from the rocks. They facilitate the efficient transference of energy from the rotating rotor to the incoming material, thereby fostering an optimal state of crushing.
Particle sculpting: The contours and designs embodied by the rotor tips exert a discernible influence upon the ultimate shape of the particles. Through strategic placement and arrangement of the tips, manufacturers attain the desired particle shapes, be it cubical or elongated, catering precisely to the prerequisites set forth by specific applications.
Resilience against wear: Owing to incessant impacts and abrasion, the rotor tips face the specter of substantial wear and tear. Consequently, manufacturers typically employ durable materials such as tungsten carbide in the fabrication of these tips, thereby endowing them with remarkable resistance to wear and bolstering the longevity of the rotor.
In essence, the primary mission of a VSI crusher revolves around the reduction of large rocks into smaller, more uniform particles via high-velocity impacts and crushing. The rotor, adorned with meticulously engineered tips, occupies a momentous role in facilitating efficient crushing and meticulous shaping of the material at hand.
What is the speed of a VSI crusher?
The speed at which a VSI (Vertical Shaft Impact) crusher operates holds paramount importance in determining its overall performance and the quality of the final crushed product. Allow us to delve into the intricacies of rotor speed within VSI crushers and the profound implications it holds for the crushing process.
Rotor speed and its impact on crushing:
The term “rotor speed” alludes to the rotational velocity exhibited by the rotor of a VSI crusher, encompassing the main shaft alongside the affixed rotor tips. This rotational speed wields direct influence over the intensity of the collisions between the rocks and the anvils or walls within the crushing chamber.
Implications for crushing efficiency:
Higher rotor speeds inherently yield a greater frequency and heightened intensity of collisions between the rocks and the anvils or walls. This augmented impact energy engenders enhanced crushing efficiency, as a larger quantum of energy is transferred to the rocks, thereby fostering superior fragmentation and the reduction of particle sizes.
Quality of the final crushed product:
The rotor speed exerts a momentous impact on the quality of the ultimate crushed product. Elevated rotor speeds generally generate finer and more uniform particle sizes, culminating in a higher-caliber end product. This attribute holds particular significance in applications necessitating precisely shaped and uniform aggregates, such as those prevalent within the construction industry.
Considerations of throughput:
The manipulation of rotor speed entails consequential ramifications for the throughput capacity of the crusher. Amplified rotor speeds tend to yield augmented throughput, as a larger quantity of rocks is processed within a given time frame. However, a delicate equilibrium must be struck between rotor speed, crushing efficiency, and the desired quality of the end product, as excessively high rotor speeds may precipitate heightened wear and maintenance requirements.
Adjustability and optimization:
Modern iterations of VSI crushers often encompass the inclusion of adjustable rotor speed settings. This invaluable feature empowers operators to optimize the crusher’s performance, tailoring it to meet the idiosyncratic requirements intrinsic to a particular application. By fine-tuning the rotor speed, operators can meticulously calibrate the balance between crushing efficiency, the quality of the final product, and the capacity for throughput.
To summarize, the rotor speed of a VSI crusher stands as an instrumental factor in the crushing process, the quality of the final crushed product, and the overall throughput capacity. Heightened rotor speeds foster augmented crushing efficiency and yield finer particle sizes, ultimately generating top-tier end products. However, identifying the optimal rotor speed necessitates contemplation of factors such as the precise specifications desired for the end product, while concurrently balancing wear and maintenance considerations.
What is the process of a VSI crusher?
The process of an impact crusher, including a VSI crusher, is characterized by a systematic sequence of events that enables the reduction of rocks into smaller particles. Allow us to elucidate the step-by-step explanation of the crushing process within a VSI crusher, shedding light on the role played by the rotor and the mechanics of impact and crushing.
The first stage: the material under the action of gravity through the hopper to form a vertical downward material flow, through the drop ring into the top of the rotor centre cone cap. Then the material is evenly distributed into a number of strands (3-5 strands) of horizontal material flow, in the acceleration channel due to the rotor spinning wave of the material of the powerful impact in the channel, the first to produce a strong extrusion and grinding crushing, and in the accelerated channel at the terminal to suffer from the rotating head of the material thrown into the collision broken.
The second stage: the horizontal material flow in the high-speed rotation of the rotor under the action of centrifugal force, by accelerating the channel is rapidly accelerated by the shooting and at the same time to obtain a huge kinetic energy. This high-speed material flow in the vortex crushing chamber and the material bedding (stone hit the stone model) or anvil (stone hit the iron model) impact, resulting in intense kinetic energy and crushing energy between the energy conversion and the collision of the collision crushing. Kinetic energy converted into crushing energy of the material will be high-speed rotor to provide a steady stream of horizontal material flow chase to produce continuous crushing, tangential projection will also produce high-speed extrusion, grinding and crushing.
The third stage: after the horizontal impact of the material, due to the huge material flow energy cannot be fully released, will be reverse spattering, if the spattering into the rotor movement area will be encountered again by the construction of the rotor counterattack to form the impact crushing.
The fourth stage: the high-speed rotor and vortex crushing chamber barrel wall between the formation of a dense high-speed vortex particle cloud, the material to chase each other, the establishment of a continuous high-energy collision, extrusion, grinding, the formation of a continuous high-energy collision of the chain in line with the reaction process.
The actual crushing process can be roughly regarded as the above four stages of the chain composite action process.
In essence, the process of an impact crusher, exemplified by a VSI crusher, transpires through the introduction of material into the crusher’s central region. The subsequent rotational motion of the rotor propels the material towards the anvils or walls, eliciting impactful collisions. This cascade of events culminates in the fragmentation of rocks and the creation of smaller particles, ultimately shaping them as desired. The final product materializes upon the discharge of the crushed particles, encapsulating the culmination of the crushing process.
How does a VSI crusher operate?
The operation of a crusher, such as a VSI (Vertical Shaft Impact) crusher, encompasses various essential aspects that contribute to its efficient and safe functioning. Let’s delve into a comprehensive overview of the operational procedures involved in running a VSI crusher, including control systems, feed mechanisms, and safety considerations.
Control Systems:
Modern VSI crushers are equipped with advanced control systems that enable precise and optimized operation. These sophisticated systems monitor key parameters like feed rate, rotor speed, and crusher power to ensure optimal performance and mitigate potential issues. Operators have the flexibility to adjust and fine-tune these parameters based on specific crushing requirements and desired product specifications.
Feed Mechanisms:
A VSI crusher receives the material through a feed mechanism, typically a feed tube or hopper. The feed mechanism is responsible for maintaining a controlled and consistent supply of material to the crusher. Regulating the feed rate is crucial to ensure a steady and efficient crushing process. Some crushers may incorporate additional features such as adjustable curtains or baffles to further control material flow, enhancing crushing efficiency.
Safety Considerations:
Operating a crusher necessitates strict adherence to safety protocols to protect both personnel and equipment. Here are some vital safety considerations:
Personal Protective Equipment (PPE): Operators must don appropriate PPE, including hard hats, safety glasses, and ear protection, to safeguard against potential hazards.
Lockout/Tagout Procedures: Before conducting any maintenance or repair tasks, proper lockout/tagout procedures must be followed. This ensures the crusher is safely powered off and isolated from energy sources.
Guarding: Crushers should be equipped with safety guards and protective covers to prevent access to moving parts during operation, reducing the risk of accidents.
Emergency Stop Systems: Crushers should have easily accessible emergency stop buttons or switches to swiftly halt operations in case of an emergency.
Training and Supervision: Operators should receive comprehensive training on the safe operation and maintenance of the crusher. Adequate supervision and monitoring during operation are crucial to maintain a safe working environment.
Overall, the operation of a crusher involves utilizing advanced control systems, managing the feed mechanisms, and prioritizing safety considerations. Proper operation and maintenance practices ensure efficient crushing processes while minimizing risks to personnel and equipment. Adhering to manufacturer guidelines and industry best practices is paramount for safe and effective crusher operation.
Conclusion
In conclusion, VSI crushers, also known as Vertical Shaft Impact crushers, are vital equipment in the crushing industry. They excel at reducing large rocks into smaller, more manageable particles, making them suitable for a wide range of applications in construction, mining, and industrial sectors. The unique design and functionality of VSI crushers enable them to deliver exceptional crushing performance and high-quality aggregates.
Understanding how VSI crushers work and their key components, such as the rotor and its tips, provides valuable insights into the crushing process. The rotor speed plays a crucial role in determining the crusher’s performance, impacting factors such as crushing efficiency, final product quality, and throughput capacity. Higher rotor speeds generally result in improved crushing efficiency and finer particle size reduction, leading to higher-quality end products. However, finding the optimal rotor speed requires careful consideration of various factors, including desired product specifications and wear and maintenance requirements.
Operating a crusher, including a VSI crusher, involves employing advanced control systems, managing the feed mechanisms, and prioritizing safety. Modern crushers come equipped with sophisticated control systems that optimize performance and protect against potential issues. Regulating the feed rate and ensuring proper safety measures, such as the use of personal protective equipment and adherence to lockout/tagout procedures, are crucial for safe and efficient crusher operation.
By adhering to manufacturer guidelines, following industry best practices, and providing adequate training and supervision, operators can ensure the efficient and safe operation of VSI crushers. These machines play a significant role in the mining and construction industry, enabling the production of high-quality aggregates and shaping the final product. The continuous advancements in technology and safety measures further enhance the performance and reliability of VSI crushers, contributing to their success in various applications.
To sum up, the world of VSI crushers is fascinating, and their importance in the crushing industry cannot be overstated. With their unique design, efficiency, and versatility, VSI crushers continue to revolutionize the production of aggregates, driving advancements in the mining and construction sectors.