The scraper cleaner used in mining conveyor belts are typically made from a variety of materials, each chosen for its durability, wear resistance, and suitability to the specific mining environment. Here are some common materials used for conveyor belt scraper cleaner:
1. Polyurethane: Polyurethane is widely used due to its excellent wear resistance, flexibility, and toughness. It performs well in abrasive environments and can be formulated in different hardness levels to suit various applications. It’s also resistant to chemicals and moisture, making it ideal for harsh mining conditions.
2.Rubber: Rubber scraper blades are valued for their elasticity and cost-effectiveness. They are often used in less abrasive environments or as secondary scrapers to complement harder materials. Rubber can absorb impact and is less likely to damage the belt surface.
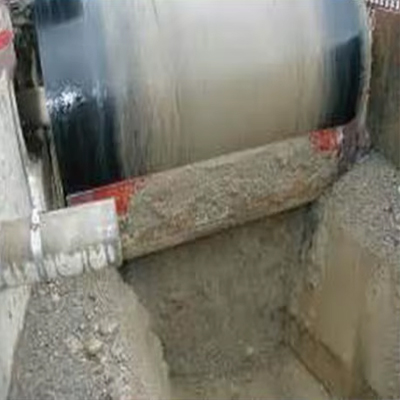
3.Carbide (Tungsten Carbide): Tungsten carbide is an extremely hard and durable material, often embedded into scraper blades for heavy-duty mining operations. It excels in highly abrasive conditions, such as handling coal, ore, or gravel, and provides a longer service life compared to softer materials.
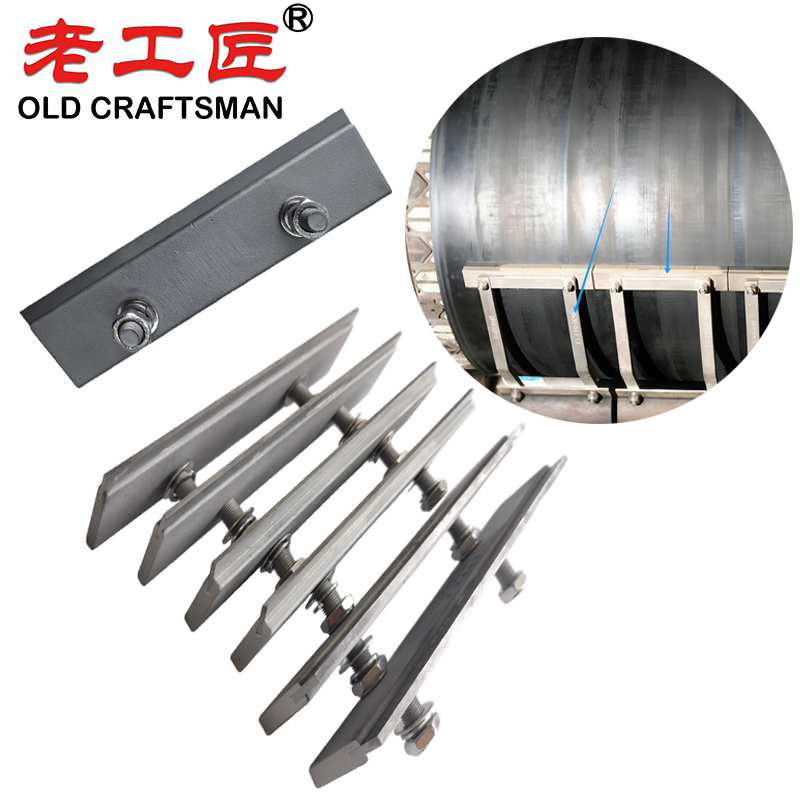
4.Steel: Stainless steel or hardened steel is used in some scraper designs for its strength and resistance to corrosion. Steel blades are typically employed in primary scrapers where robust cleaning of sticky or tough materials is required.
5.Ceramics: Ceramic-tipped or ceramic-embedded scraper blades offer exceptional hardness and wear resistance. They are particularly effective in extreme conditions involving sharp, abrasive materials, though they may be more brittle than other options.
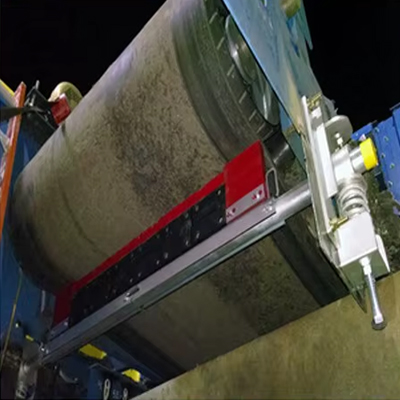
6.Composite Materials: Some scraper blades combine materials like polyurethane with ceramic or carbide inserts to balance flexibility, durability, and cost. These hybrids are tailored to specific mining needs, offering versatility in challenging environments.
The choice of material depends on factors like the type of material being conveyed, the conveyor speed, environmental conditions (e.g., wet or dry), and budget considerations. For instance, polyurethane and rubber are more common in lighter applications, while carbide and ceramics dominate in heavy-duty, high-wear scenarios.
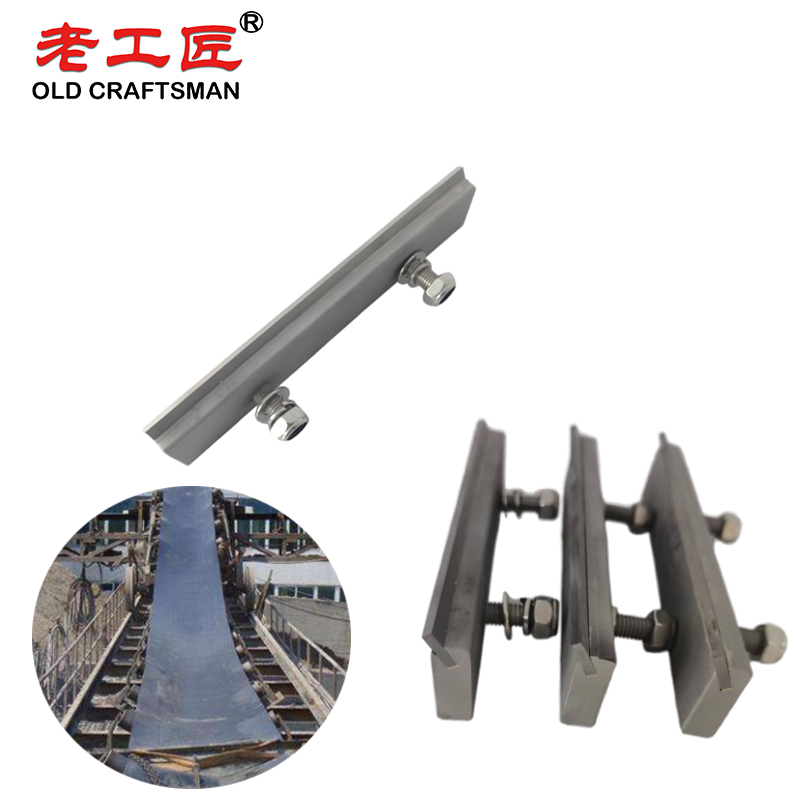
“Zhuzhou Old Craftsman Precision Alloy Co., Ltd. could make tungsten carbide wear parts and make your equipment use life is tens of times longer than before! We specialize in providing customized carbide wear products solutions to meet the demanding requirements of industries such as aerospace, automotive, mining, and precision machining.”
Blet scarper Brazing brazingprocess CARBDIE HAMMER carbide Carbide belt scraper carbidebrazing carbide hammer Crusher CRUSHER HAMMER Informational Internal stress metal mining mold operate Refractory Brick Mold Secondary belt cleaner scraper stresses VSI VSI crusher wear plates welding work