In mineral processing, the HPGR feed chute plays a crucial role in ensuring the smooth operation of the entire high-pressure grinding roll (HPGR) system. It’s not just a simple channel for material; it directly affects the efficiency and performance of the grinding process. Given the intense friction and pressure experienced during operations, the HPGR feed chute needs to be built with durability in mind.
For any equipment operating under heavy loads, the durability of the HPGR feed chute is directly linked to the overall efficiency of the crushing system. The right wear liners can protect the feed chute, minimize downtime, and lower long-term operational costs.
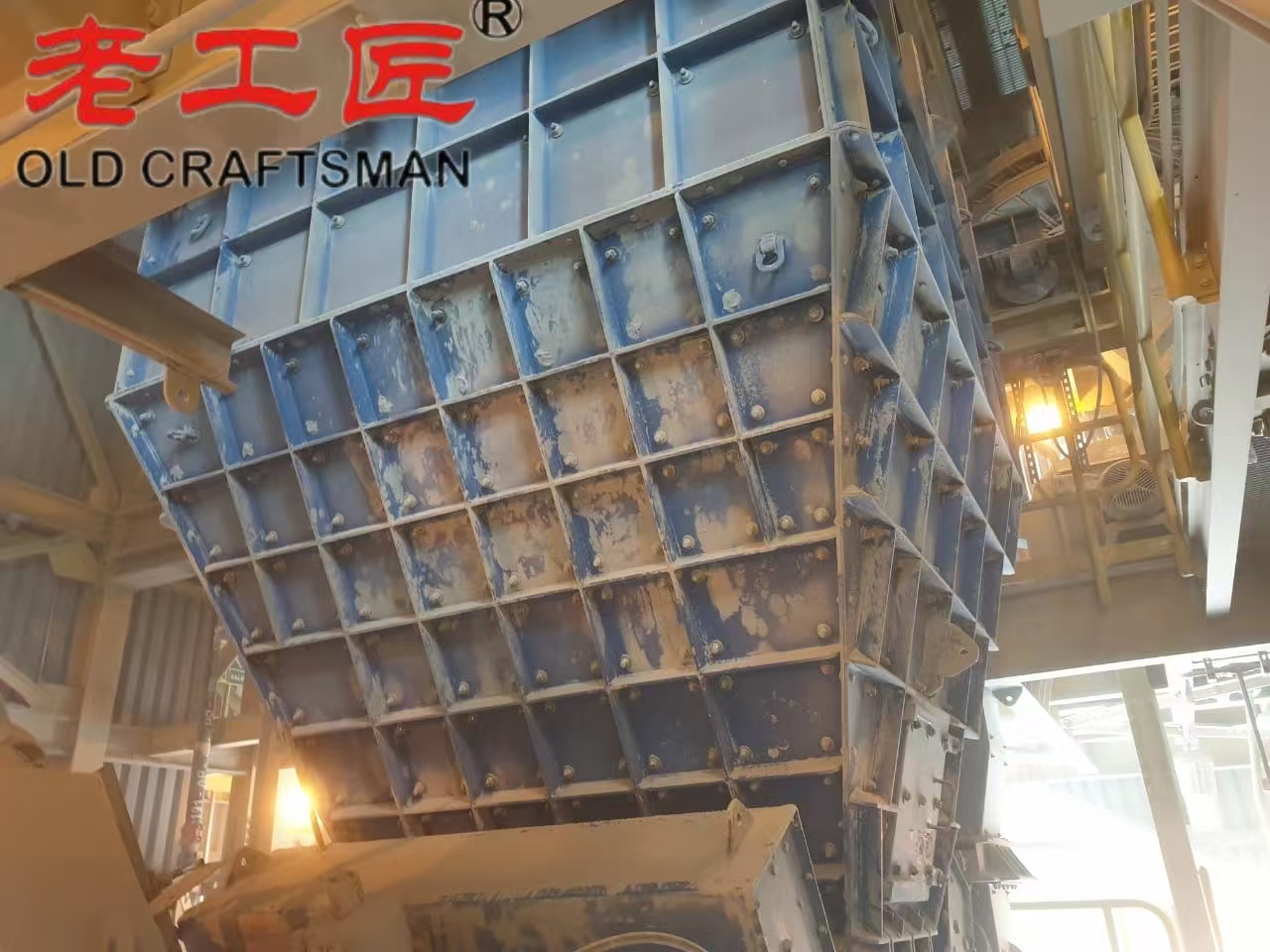
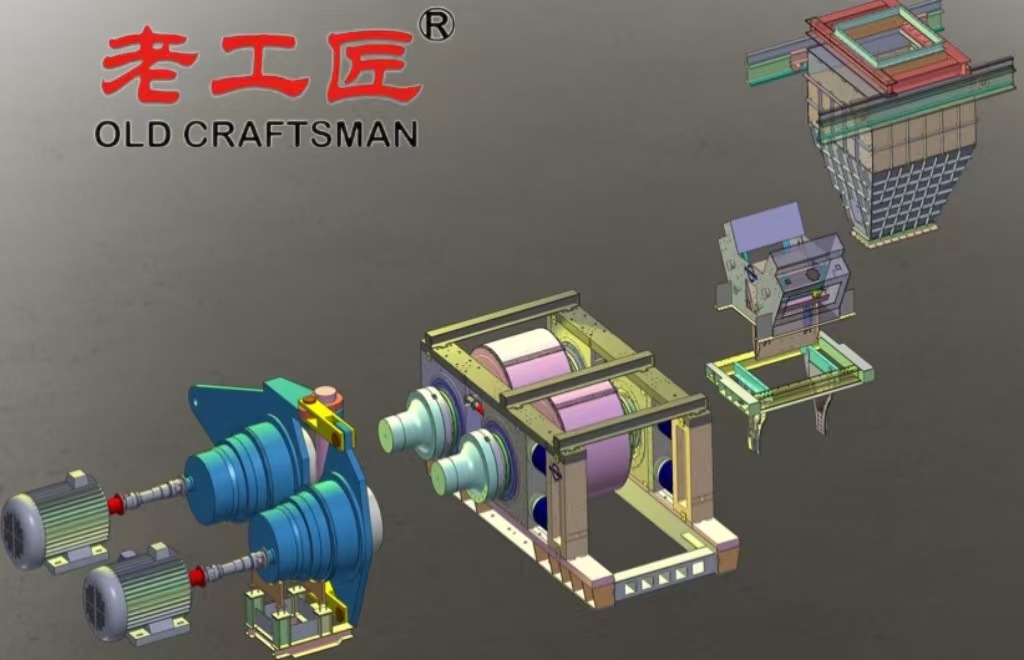
Why is the HPGR Feed Chute So Important?
The HPGR feed chute is responsible for directing the material evenly into the grinding rolls. A consistent and smooth flow of material ensures that the HPGR system functions at peak efficiency, preventing blockages and optimizing throughput. If the feed chute fails or gets damaged, it can result in material jams or inefficiencies that hinder the entire process.
Because of the significant wear and tear the HPGR feed chute experiences during operation, it’s essential to protect it from excessive damage. This is where wear liners come in—they act as a shield, absorbing impact and reducing abrasion.
The Role of Wear Liners: How They Protect HPGR Feed Chutes
In harsh environments like those of an HPGR system, wear liners are crucial for extending the lifespan of the HPGR feed chute. These liners are specifically designed to withstand extreme wear from abrasive materials, significantly reducing the frequency of repairs and replacements.
Tungsten Carbide is a material commonly used in HPGR wear liners due to its superior wear resistance. Tungsten Carbide vacuum brazed wear liners are designed to handle the intense abrasion present in high-pressure grinding applications, making them an ideal choice for HPGR feed chutes.
Scientific Data Supporting Tungsten Carbide in HPGR Applications
Several independent studies and industry reports have verified the remarkable advantages of Tungsten Carbide wear liners for HPGR systems. Some of the most authoritative data includes:
1.Tungsten Carbide’s Superior Wear Resistance:
A study published in the Journal of the Southern African Institute of Mining and Metallurgy (SAIMM) (2018) demonstrated that Tungsten Carbide wear liners outperform conventional steel and chromium-based materials by up to 400% in wear life when used in HPGR systems. The study specifically highlighted Tungsten Carbide’s ability to resist wear under high impact and abrasive conditions commonly found in mineral processing.
2.Reduction in Maintenance Intervals:
According to a research paper from the University of Queensland (2019) on wear behavior in HPGR systems, plants that used Tungsten Carbide vacuum brazed wear liners experienced 50-60% longer operational lifespans for their HPGR equipment. The paper also noted a 40% reduction in unscheduled downtime, as the material was able to withstand the abrasive nature of ores like gold, copper, and iron ore.
3. Increased Throughput and Efficiency:
An industry report from Metso Outotec (2020) revealed that HPGR systems fitted with Tungsten Carbide wear liners exhibited a 15-20% increase in throughput when processing hard and abrasive ores. The study attributed this improvement to the durability of the wear liners, which ensured that the feed chute remained in optimal condition for longer periods, allowing for smoother material flow and reducing blockage risks.
4. Cost Savings in the Long Run:
A field study published by Mining Magazine (2021) reported that operations using Tungsten Carbide wear liners in HPGR systems reduced their overall operational costs by 25-35% over five years. This reduction was primarily driven by lower replacement costs, less frequent maintenance, and increased uptime.
5. Custom Solutions:
Our Tungsten Carbide Vacuum Brazed Wear Liners are tailored to meet the specific needs of your HPGR feed chute, ensuring the best fit for your operation and material characteristics.
Why Choose Our HPGR Wear Liners?
At ZZ Craftsman, we specialize in manufacturing custom HPGR wear liners designed to offer maximum protection for HPGR feed chutes and other high-wear areas in crushing systems. Our Tungsten Carbide Vacuum Brazed Wear Liners are engineered to provide excellent resistance to wear in high-impact, abrasive environments, extending the life of your equipment.
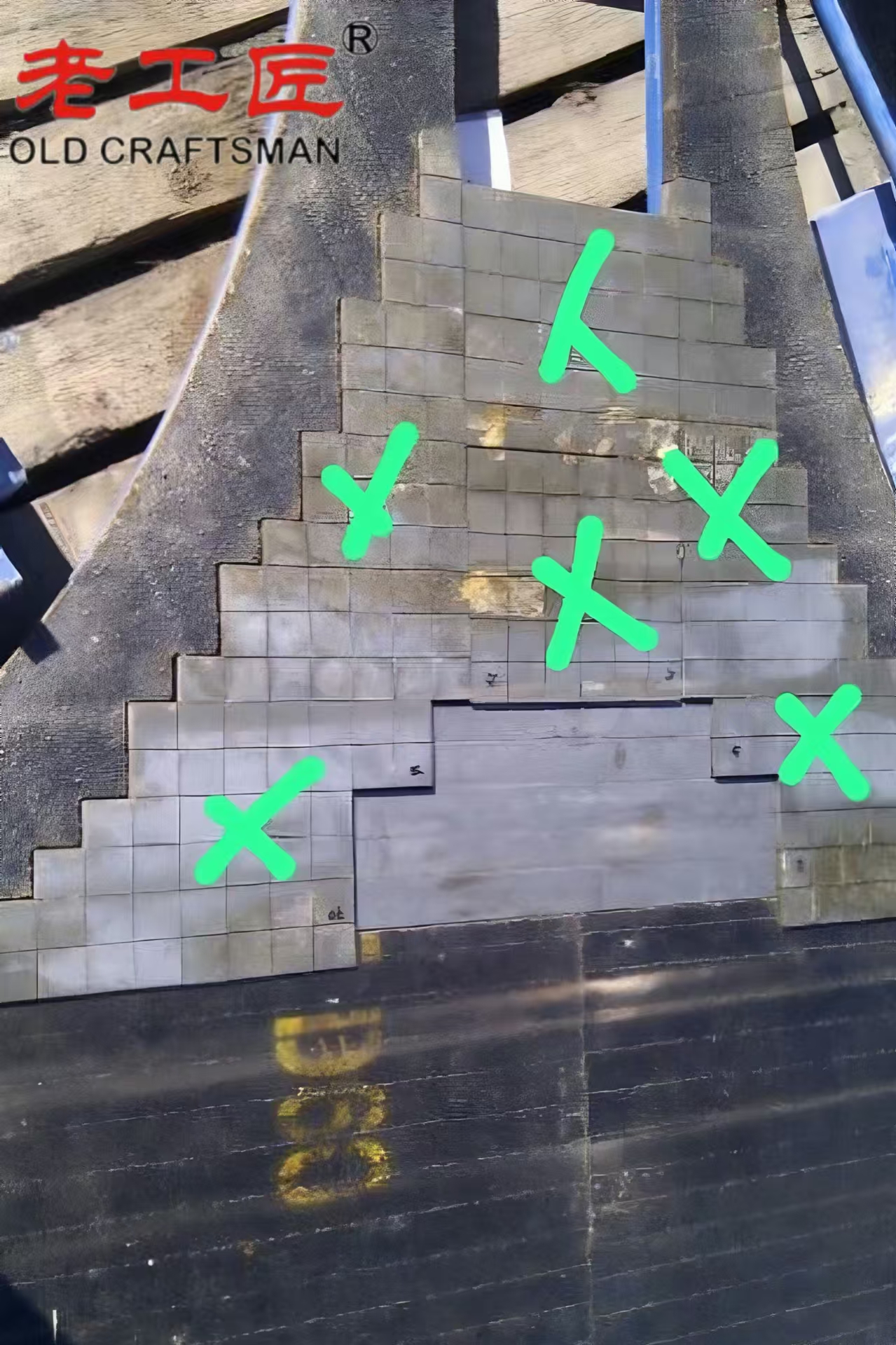
(This is a picture of the installation of the wear-resistant lining produced by our company)
We can not only produce the wear-resistant lining marked in green in the above picture, but also the connecting parts next to it can be customized and produced in various shapes without restriction.
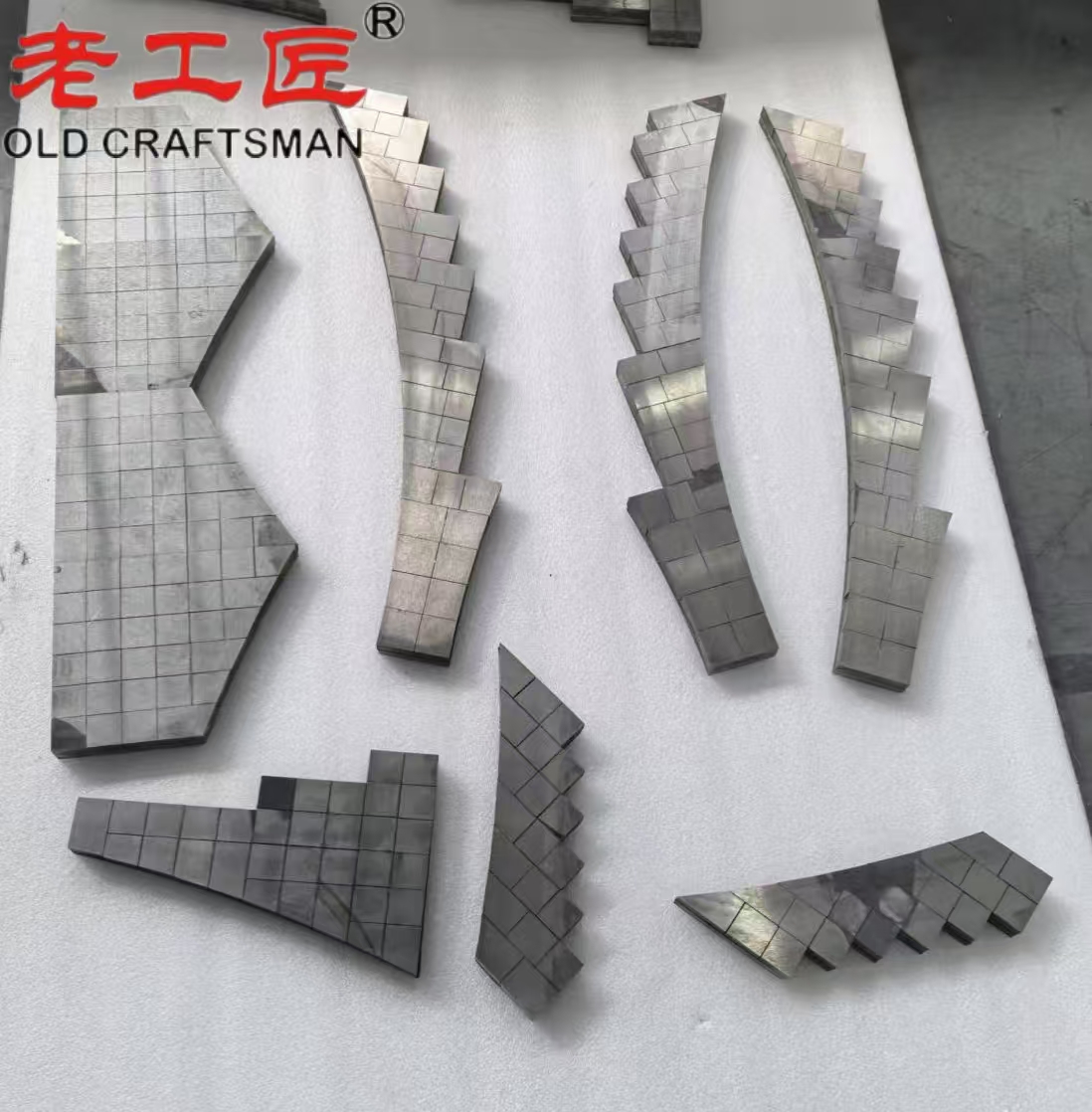
When you choose our products, you get:
- Superior wear resistance in the toughest environments, ensuring your HPGR feed chute operates smoothly.
- Tailored solutions that match your specific HPGR system and material processing needs.
- Cost savings through reduced maintenance needs and fewer replacements.
Conclusion: Protecting Your HPGR System with the Right Wear Liners
To maintain optimal performance in today’s high-efficiency crushing systems, the HPGR feed chute must be protected with the right wear liners. Choosing Tungsten Carbide vacuum brazed liners can help prevent excessive wear, reduce maintenance costs, and improve the overall efficiency of your HPGR system.
If you’re looking for durable, high-performance wear liners for your HPGR feed chute, we have the perfect solution. Contact us today to learn more about our products and how we can help you enhance the performance of your HPGR system.
If you want to know more, please contact us.