Project country: Peru
Date:2024.12
Application: wear liners for high pressure grinding rolls feeder chute
Project detail: it carbide brazed wear plates used in High Pressure Grinding Roller Machine’s feed chute
Material used:15mm thickness 30mm*30mm carbide tiles vacuum brazed on the steel plates, different shapes.
Here are some pictures of the products being packaged:
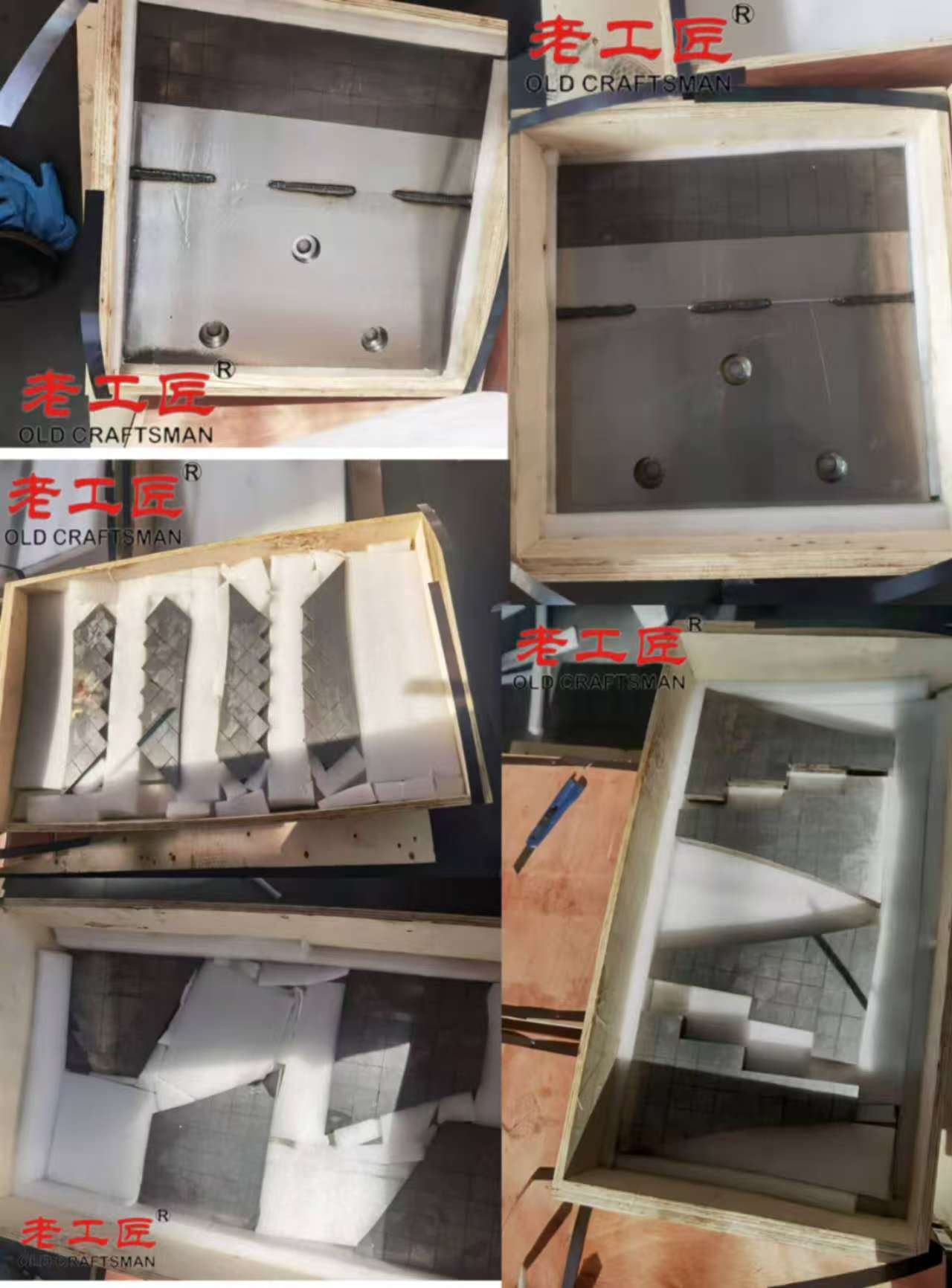
Why more and more companies choose tungsten carbide wear plates in high pressure grinding rollers (HPGR)’s feed chute?
- Excellent wear resistance
High hardness: The hardness of tungsten carbide is close to that of diamond (about 90 HRA), which can effectively resist the strong wear of materials in high-pressure grinding rollers on equipment.
High impact resistance: Under high pressure and severe friction, tungsten carbide materials have good impact resistance and can maintain stable performance under various working conditions. - Excellent heat and corrosion resistance
High temperature resistance: Tungsten carbide materials can maintain physical and chemical stability in high temperature environments and adapt to thermal shock and high temperature conditions during the operation of high-pressure grinding rollers.
Corrosion resistance: Suitable for corrosive minerals or wet environments, it can effectively prevent the accelerated wear of equipment caused by chemical corrosion. - Significantly extend service life
High reliability: Tungsten carbide vacuum brazed wear-resistant plates combined with advanced manufacturing processes greatly improve the bonding strength between the wear-resistant layer and the substrate, and are not easy to peel off or fail.
Reduce replacement frequency: Compared with traditional wear-resistant materials (such as ordinary high manganese steel or ceramic composite plates), tungsten carbide materials have a longer service life, reducing the cost and downtime of frequent replacement. - Improve equipment operation efficiency
Stable roller surface performance: Tungsten carbide wear-resistant plates can maintain the consistency of roller surface shape, ensure uniform pressure on materials, and improve grinding efficiency.
Reduce energy consumption: After the wear is reduced, the equipment runs more smoothly, thereby reducing power consumption and improving the overall performance of the high-pressure roller mill. - Adapt to harsh working conditions
High pressure and high strength: Tungsten carbide materials can withstand high-intensity operations under extreme working conditions in high-pressure roller mills and are not easy to deform or crack.
Wide applicability: Suitable for processing ore materials with high hardness and sharp particles (such as iron ore, diamond ore, and copper ore, etc.). - Significant long-term economic benefits High cost-effectiveness: Although the initial cost of tungsten carbide wear-resistant plates is high, the overall cost of use is significantly reduced due to their long life and low maintenance requirements.Environmental benefits: Reduce material replacement and waste generation, in line with the requirements of green production and sustainable development.
From the above, we can know that the wear-resistant plate made of tungsten carbide stands out in the high-pressure grinding roller mill for its excellent wear resistance, impact resistance and high reliability. It is an ideal choice for improving equipment operation efficiency and reducing comprehensive costs, especially suitable for extreme working conditions and high-intensity application scenarios. This is why more and more companies choose our tungsten carbide material as the wear-resistant lining of the high-pressure roller mill feeding chute.