Innovative Design Features for Long-Lasting Refractory Brick Molds
Over the past decade, the refractory brick mold has undergone a series of changes and innovations. On the one hand, with the rapid development of high-temperature industry and technological progress, the performance and quality requirements for refractory brick molds have become higher and higher. On the other hand, the emergence of various new materials, processes and technologies has also brought new opportunities and challenges for the design and production of refractory brick molds.
In terms of materials, more and more new high-temperature materials are being used in the production of refractory brick molds, such as silicon carbide, alumina, silicon nitride, etc.
In terms of design and production, the wide application of CAD technology, digital manufacturing technology and intelligent production technology has not only improved the precision and quality of refractory brick molds, but also accelerated production efficiency and reduced costs.
In addition, more and more attention has been paid to the use and maintenance of refractory brick molds, and various new maintenance programs have been developed that can extend the service life of refractory brick molds and reduce maintenance costs.
In the past ten years, Zhuzhou Old Craftsman has also made a series of explorations on the materials and design of refractory brick molds, and after unremitting efforts, we have successfully developed a unique refractory brick mold.
How do we change the design of refractory brick mold?
Difference in the shape of refractory brick mold:
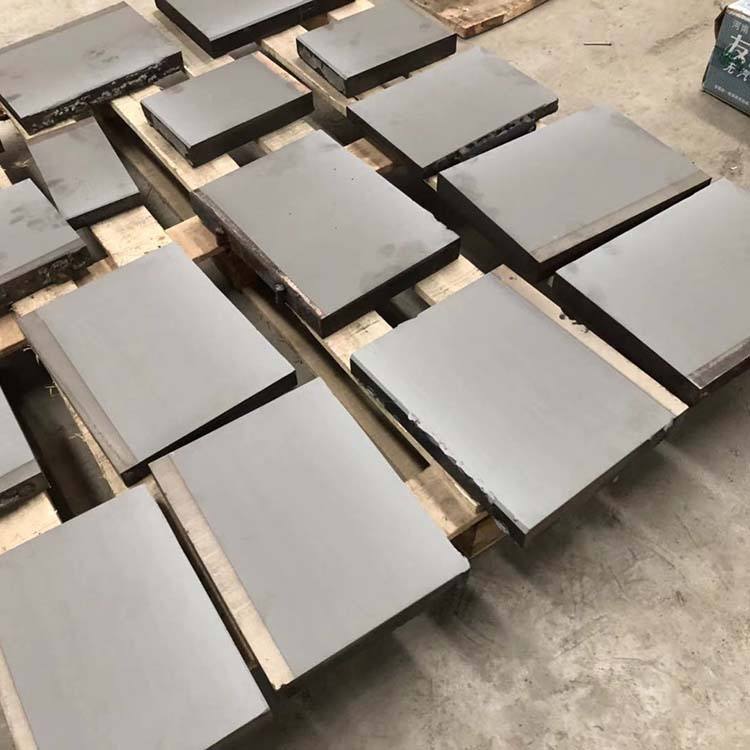
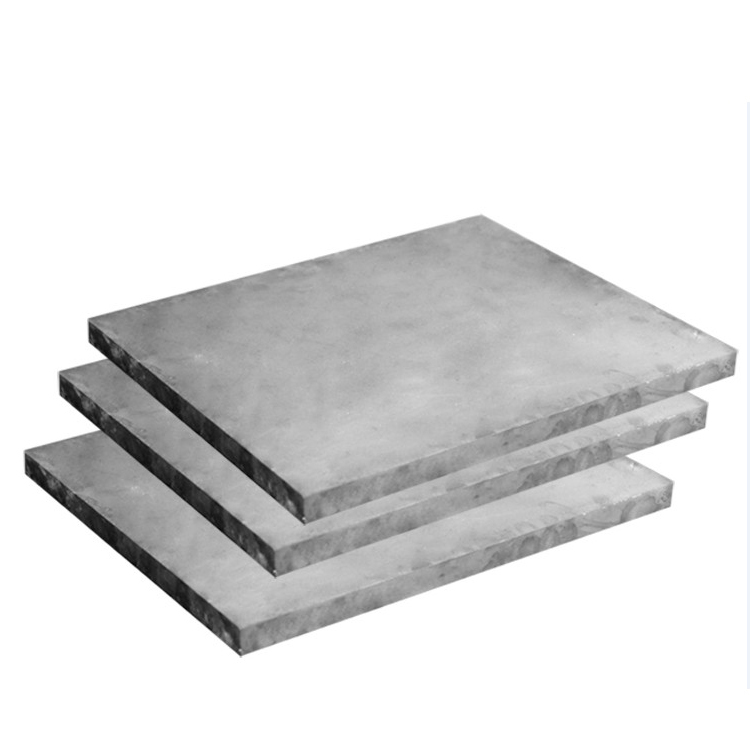
①Take steel parts as the main body and apply wear-resistant coating on the outside.
②Take the carbide wear plate as the main body and replace the steel parts
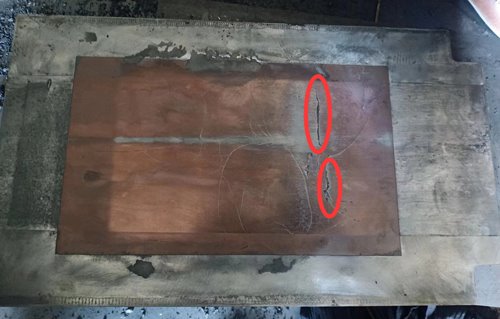
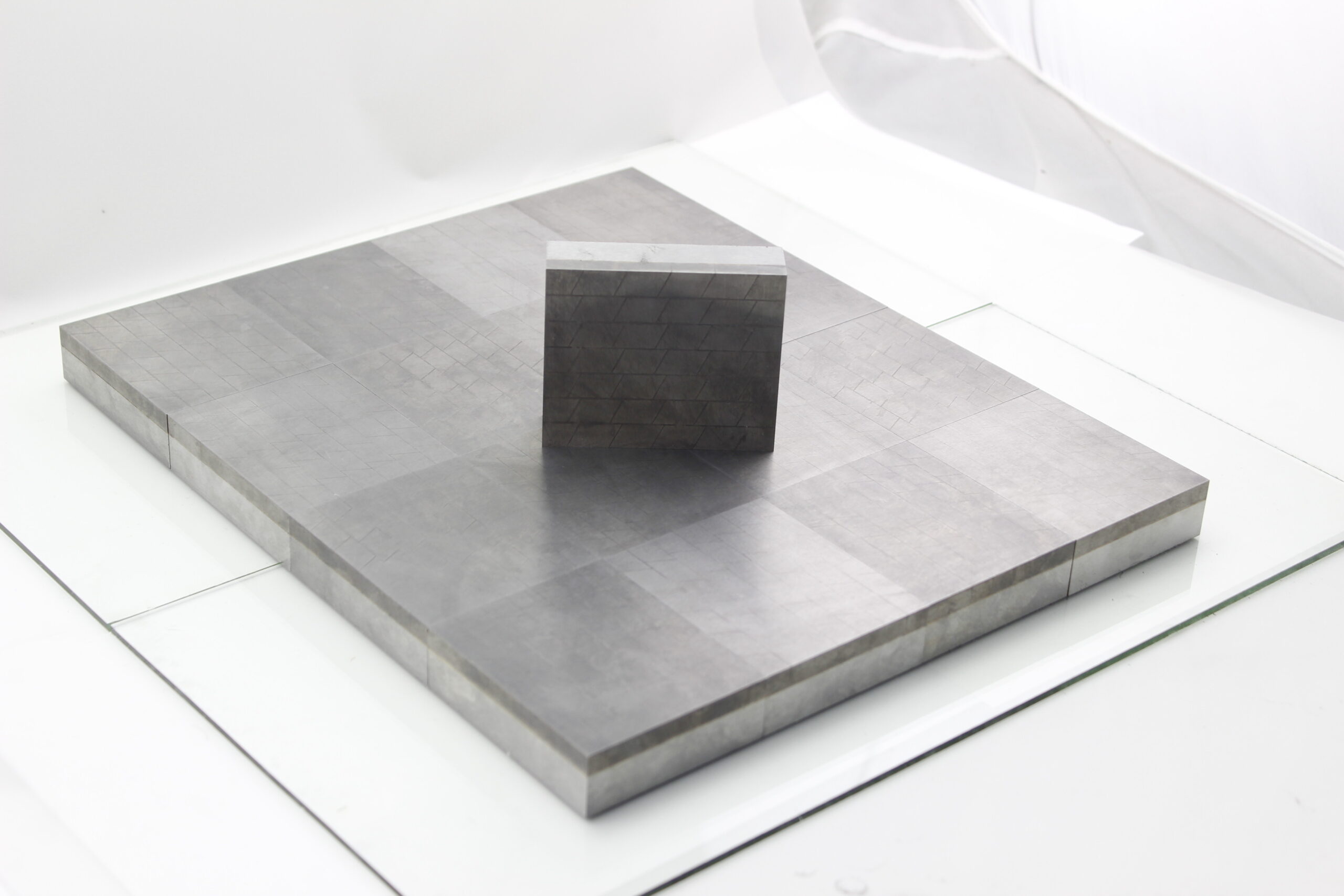
③Previous design: Take steel parts as main body and weld carbide plate on the substrate.
④Current design: Take steel parts as the main body and replace carbide plate with small carbide plates, arrange and weld them according to certain design.
Check the detailed picture:
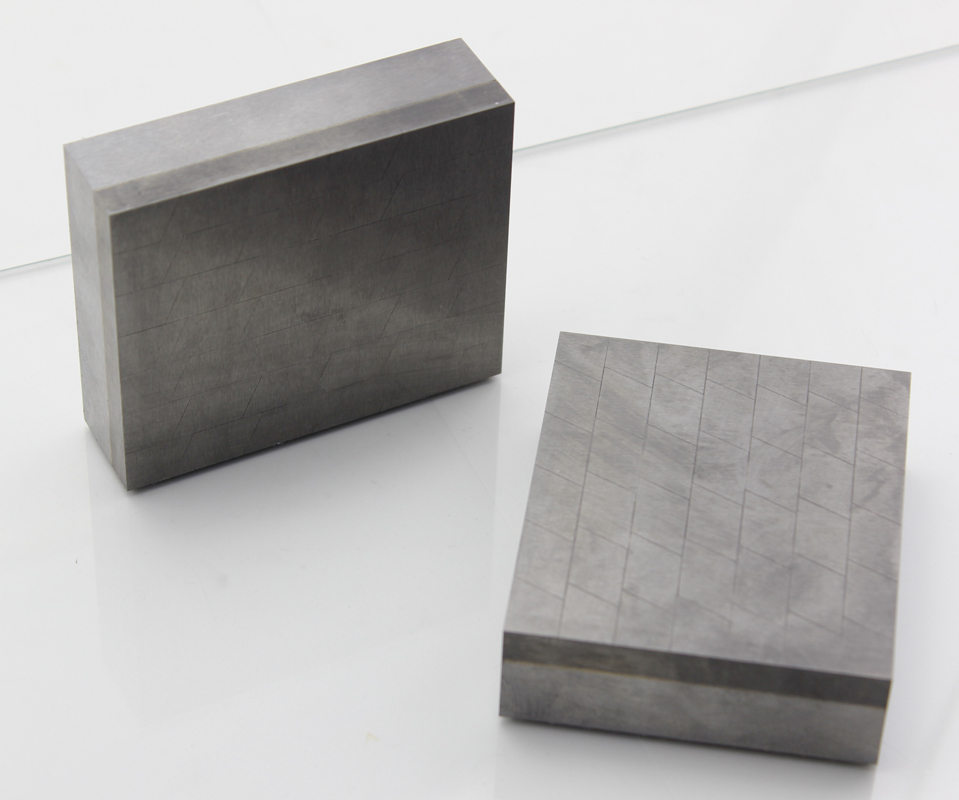
As you can see, the carbide refractory brick molds we design are different from the above molds. We use the vacuum brazing technology to weld the carbide pieces on the steel substrate. And through the reasonable layout, there is almost no gap between the welded joints. This arrangement can generate low internal stress, which can ensure the production of high precision refractory bricks.
Why do we change refractory mold in this way?
① Wear-resistant coated steel parts. Wear-resistant coating usually has high hardness and wear-resistance, and is able to resist various external environments and abrasive effects. It also has certain corrosion resistance and can be used in tough environments. Although the wear-resistant coating has the advantages of good coating, easy to use and low cost, its hardness and wear resistance is slightly inferior to that of cemented carbide. In addition, the refractory brick production process is usually in harsh environment with a high pressure, which has high requirements for the wear resistance of the mold.
② Cemented carbide has higher hardness and wear resistance, especially in the extreme environment such as high temperature, high pressure and heavy load. Cemented carbide is usually pressed from a mixture of tungsten-cobalt alloy and other metal powders, which have high hardness, wear resistance, corrosion resistance and high temperature resistance. However, the cost of cemented carbide is high, and it is difficult to process and repair, and there is few feasibility of using the whole cemented carbide wear plate for refractory brick molds.
③ Steel parts and welded carbide wear plate. This design uses welding to combine the carbide plate and steel parts. This method reduces the cost to a great extent compared to ② and has a longer service life than ①, which seems to be very suitable for refractory brick molds. However, in practice, cracks can easily appear due to the internal stresses generated in the whole wear plate during high pressure loading. This not only affects the service life of the mold, but also greatly reduces the accuracy of the refractory brick products.
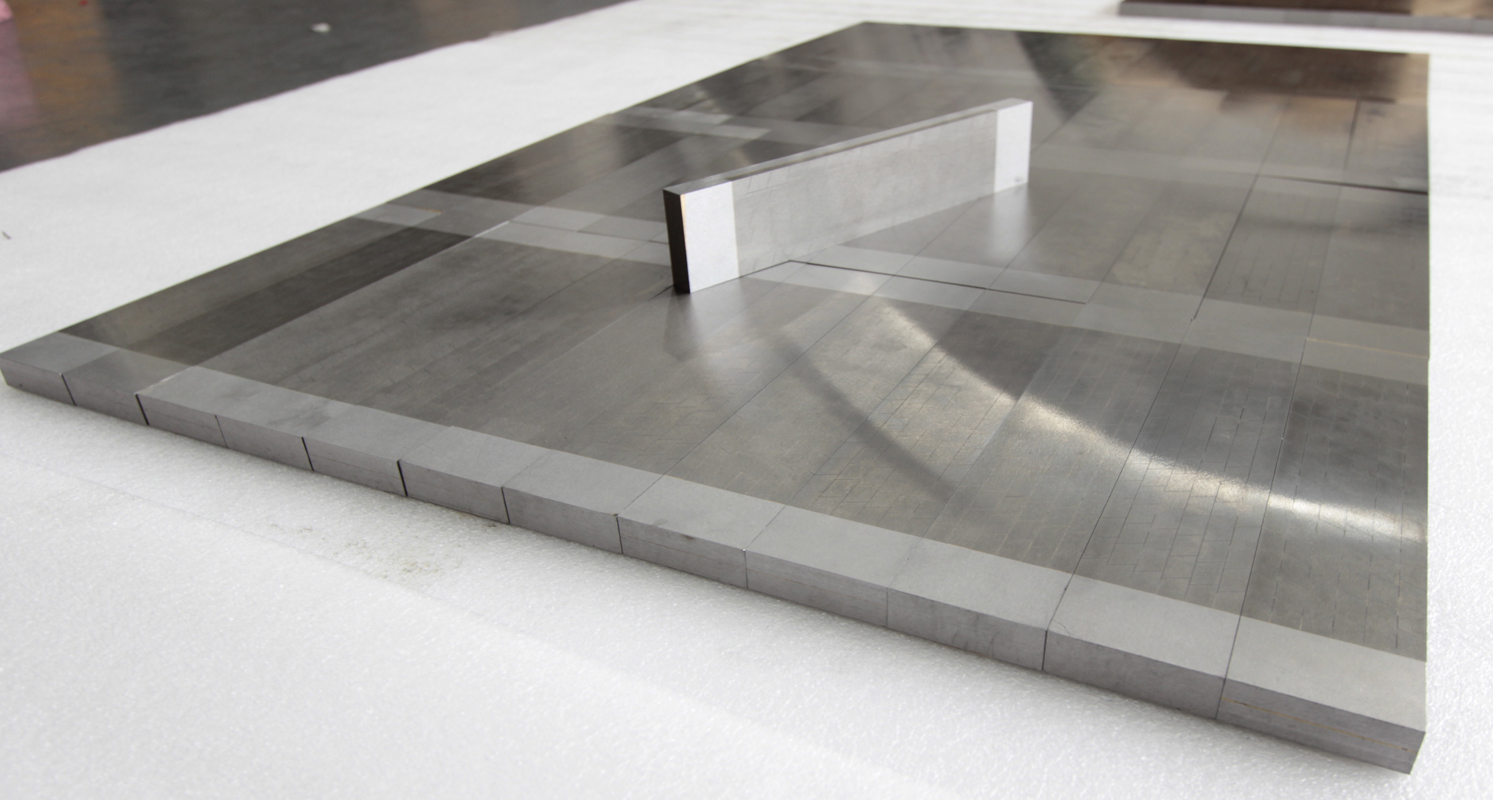
④Steel part with welded small carbide plates. The design is similar to ③, but instead of using a whole carbide plate for welding, small carbide pieces are brazed onto the steel part substrate through a staggered arrangement of layers. This arrangement can effectively reduce the internal stress during pressing process, greatly reducing the chance of cracks in the die. This can significantly increase the product life, reduce the cost of downtime for maintenance and replacement, and allow pressing times to exceed 15,000. In addition, the choice of small carbide pieces makes it less difficult to process and repair, while vacuum brazing can also effectively avoid the problems of corrosion and oxidation of cemented carbide.
How to improve the service life of refractory brick mold
The factors affecting the wear of the mold are various and comprehensive. For instance, the geometry, size and mechanical properties of the abrasive (hardness, strength, etc.), as well as the size of the collision angle between the abrasive grain and the surface being rubbed. The following are some suggestions to improve the service life of the mold:
Reasonable mold design is the basis to ensure its life. The batch, shape and precision of the finished product determine the structure of the mold, and attention should be paid to the economy of its use; a suitable refractory brick mold not only has a compact structure and flexible and convenient operation, but also can make the its parts have enough strength and hardness. The design of refractory brick molds should generally follow the following basic principles:
1. Correctly select the direction of pressure, and make the molding pressure on the small or thin parts section as far as possible.
2. Strive for simple structure, easy processing, assembly and replacement.
3. Ensure the air discharge when forming, so as to avoid the elastic after-effect caused by the pressure of the blank to make the refractory bricks cracking.
4. The side plate of the mold requires high hardness, while the upper and lower plates should not be too high, otherwise it is easy to collapse the edge and fall off the block.
5. Mold surface should be processed to a high degree of finish, to ensure that the gap is uniform, to prevent the sticky material from affecting the accuracy of refractory bricks.
Refractory brick mold, used in pressing machine, should be crafted with higher precision and rigidity, and try to use high-precision mold suit and double-sided pressing machine to form bricks in a floating way. This is because when doing single-sided pressing, the maximum impact force is concentrated on the platform, and the mold is easy to wear in some part. During the downtime, it is suggested that the mold surface is clean and stored in a dry environment, and check whether there are cracks on the surface before and after using.
Conclusion
No mold can be used once and for all, and it is necessary to constantly innovate new molds that meet higher requirements. In this regard, it is also possible to consider molds made from different materials or match several molds with different hardness in order to extend the service life of each. Zhuzhou Old Craftsman promises to continue to explore new refractory brick mold designs to meet the higher requirements of the refractory market. We offer a variety of customized designs and optimization services to meet the needs of our customers in different application environments. We also provide maintenance programs for our customers to extend the life of their refractory brick molds. We believe that our refractory brick molds can provide stable, efficient and long-lasting services for various high-temperature industries. If you have unique ideas or guidance, you are welcome to contact us, and we will provide you with first-hand experimental data to make your ideas become reality.