Tungsten Carbide Blank
A wide range of tungsten carbide we are supplying, such as brazed tips, carbide shims which are in stock. Fast delivery, high and stable quality.
REQUEST A QUOTE FOR MORE DETAILS
Something you should know about tungsten carbide blanks
Tungsten carbide blanks, also known as cemented carbide blanks or hard metal blanks. Tungsten carbide blanks combine high wear resistance, hardness and strength to form a hard-wearing material used in a variety of manufacturing processes. Crafted through an intricate process involving the mixing of tungsten carbide powder with binders like cobalt or nickel then pressed into its desired shape before being heated at extreme temperatures - it's almost like baking your own custom cake! As such these materials offer unparalleled durability ideal for use across industries requiring consistent performance in rough conditions. Furthermore they are able to carry out specialized tasks that other products cannot handle reliably due their versatility which makes them invaluable within certain sectors.
What are the grades, properties, and applications of tungsten carbide blanks?
Carbide grades
There are a variety of tungsten carbide grades, each with its unique properties. These grades are enumerated by the cobalt used in their manufacture, and the amount of cobalt affects their hardness, toughness, and resistance to corrosion. Below is a table of carbide grades:
Grade | Density g/cm3 | Hardness HV3(HRA) | Strength MPa | Grade | Density g/cm3 | Hardness HV3(HRA) | Strength MPa | |
YK05 | 14.85-15.05 | 91 | 2500 | YS2T | 14.35-14.55 | 92 | 2400 | |
YK10 | 14.60-14.76 | 90 | 2700 | YS25 | 12.95-13.15 | 91.5 | 2500 | |
YK20 | 14.40-14.60 | 86 | 3000 | YC40 | 13.04-13.20 | 91 | 2300 | |
YK25 | 14.40-14.60 | 87 | 2800 | YC45 | 12.65-12.85 | 91.5 | 2500 | |
YG6 | 14.85-15.05 | 91.5 | 2200 | YF06 | 14.86-14.96 | 93.5 | 2400 | |
YG6X | 14.85-15.05 | 92.5 | 2000 | YU08 | 14.56-14.65 | 92.5 | 2200 | |
YG8 | 14.65-14.85 | 90 | 2600 | YL10.2 | 14.40-14.55 | 91.5 | 3200 | |
YG8C | 14.55-14.75 | 88.5 | 2800 | YT5 | 12.90-13.10 | 90.5 | 2200 | |
YG11 | 14.30-14.50 | 88.5 | 2700 | YT14 | 11.40-11.60 | 91.5 | 2000 | |
YG11C | 14.20-14.40 | 87 | 2800 | YT15 | 11.25-11.45 | 92 | 1800 | |
YG15 | 13.95-14.15 | 88 | 3200 | YW1 | 13.20-13.40 | 92.5 | 2000 | |
YG20 | 13.45-13.65 | 85 | 2600 | YW2 | 13.00-13.20 | 92 | 2200 | |
YG20C | 13.40-13.60 | 83.5 | 2800 | YN8 | 14.61-14.85 | 91.5 | 2500 | |
YS30 | 12.65-12.85 | 91 | 2400 | YN10 | 14.22-14.40 | 91.0 | 2800 |
Superb properties
Tungsten carbide blanks are known for their exceptional mechanical properties, which include:
High hardness: Tungsten carbide blanks boast an impressive level of hardness – second only to diamond. This makes them optimal for a variety of applications, from cutting tools and drilling bits to wear-resistant parts that withstand prolonged use in challenging environments.
High strength: Tungsten carbide blanks have proven to be an invaluable material in challenging applications: providing unyielding resilience against extreme temperatures, pressures and bending over prolonged periods. With the strength of metal coupled with incredible durability, these materials are reliable solutions for those seeking dependable performance.
Resistance to wear and tear: Tungsten carbide blanks are highly resistant to wear and tear, making them ideal for use in high-wear applications.
Corrosion resistance: Tungsten carbide blanks are resistant to corrosion and can withstand exposure to harsh chemicals and environments.
Some testing of products' properties in the production line

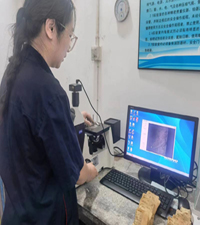

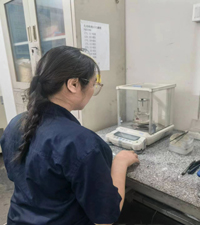
What are the common applications of tungsten carbide blanks in the manufacturing industry?
Aerospace, mining, automobile manufacturing, mold manufacturing and other industries have been counting on tungsten carbide to improve and innovate people’s daily life. Tungsten carbide blanks have become an essential tool in the manufacturing industry due to their remarkable properties, such as high hardness and strength. This versatile material is utilized for a variety of purposes ranging from machining tools and die making, to even jewelry production. With its wear-resistance capabilities allowing it to be used under extreme conditions, tungsten carbide serves countless industries with innovative design solutions that are both cost effective and sustainable.
Below are some applications that you are more likely to find their contribution.
Cutting tools: Tungsten carbide blanks are widely seen in the production of cutting tools, including saw blades, drill bits, milling cutters, and turning tools. The cutting speed and sharpness of tungsten carbide, along with the hardness and wear resistance, make it unparalleled choice for cutting, drilling, and shaping tough materials like metals, composites, and wood.
Wear parts: A wide range of wear parts, such as nozzles, valves, bearings, and seals for industrial equipment, are also the creation of tungsten carbide blanks. Exposed to harsh environments, these components are required to withstand high temperatures, and abrasive materials, and the durability of tungsten carbide makes it a popular choice for these applications.
Mining tools: Mining industry has always been the regular customer for tungsten carbide blanks to manufacture drilling bits and cutting tools for excavating and processing minerals. These mining tools are subjected to extreme conditions, and they look for the help of tungsten carbide because of its high wear resistance and toughness to perform effectively.
Aerospace components: Tungsten carbide blanks are also a close friend with aerospace industry. Many precise and high-performance components, such as turbine blades, engine components, and landing gear parts, are manufactured by them. The tungsten carbide of high bonding strength and great heat resistance becomes the engine for these applications.
Medical instruments: Tungsten carbide blanks may be hardly connected to manufacture surgical instruments such as scalpels, scissors, and forceps. Yet, these precise instruments are required with the highest hygienic standards, and must avoid corrosion and deformation. That’s why they need the helping hand of tungsten carbide blanks. The hardness and corrosion resistance of tungsten carbide make it suitable for use in medical environments.



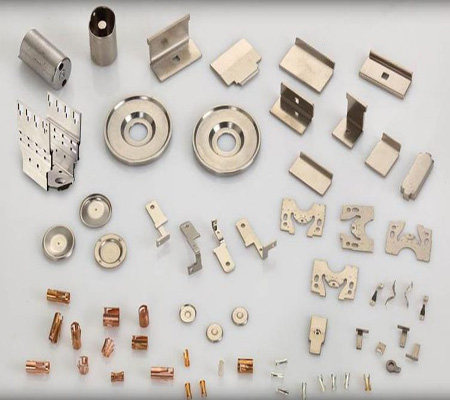
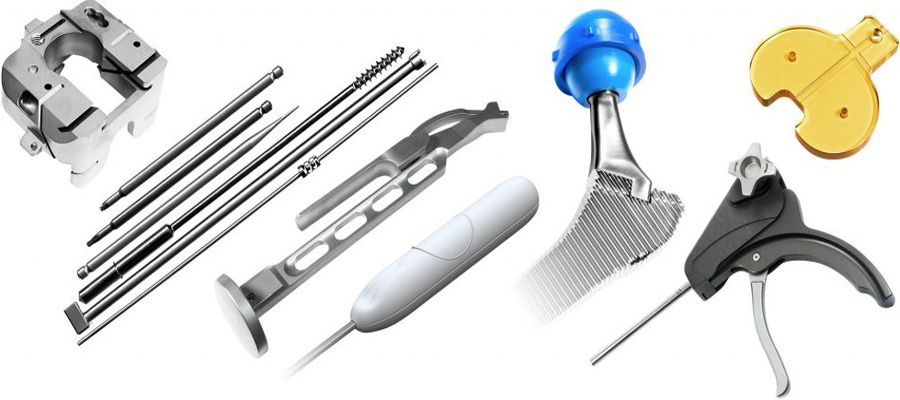
Some more questions and answers about tungsten carbide blanks:
Q: What is the typical hardness of tungsten carbide blanks?
A: Tungsten carbide is known for its exceptional hardness, with a typical hardness range of 800 to 2000 HV. To put that into perspective, diamonds have a hardness of 10 on the Mohs scale, while tungsten carbide can range from 74 to 94. It's like having the Hulk's strength in material form!
Q: What is the maximum temperature tolerance of tungsten carbide blanks?
A: Tungsten carbide has a high melting point of 2780°C and can withstand temperatures up to 1000°C without any loss of hardness or strength. That's like having a material that can handle the heat of a dragon's breath!
Q: What is the difference between tungsten carbide and tungsten steel?
A: Tungsten is a metal that is known for its durability, strength and high melting point. However, tungsten carbide is an alloy of tungsten and predominantly carbon which makes it even better. Tungsten Carbide has a higher ranking on the Mohs scale than regular tungsten does, making it more resistant to scratches and damage over time.
Q: How do you maintain tungsten carbide blanks?
A: Tungsten carbide blanks require minimal maintenance, and it is still important to keep them clean and free of debris. It is recommended to clean them with a soft cloth or use mild detergent regularly. Totally, tungsten carbide blanks will save extra time for buyers. It is also significant to store tungsten carbide blanks in a dry, cool place to prevent corrosion.
Q: Can tungsten carbide blanks be recycled?
A: Yes, tungsten carbide blanks can be recycled. The process involves grinding the used carbide into a powder and then using it to create new tungsten carbide blanks. It is really environmental-friendly and cost-effective.
Conclusion:
Tungsten carbide blanks are ideal for a wide variety of industries, delivering exceptional strength and durability that can stand up to wear and tear. From cutting tools & jewelry to aerospace components & medical equipment – the possibilities seem endless with this remarkable material! Making tungsten carbide an invaluable choice in many applications today.