I. ZZ craftsman researched and developed the carbide vacuum brazed wear liners for 10 years
Artwork Advantages:
- “Hardness: HRA 89-91”
- “Customizable Thickness for Your Needs”
- “Proven in Iron Ore and Copper Mining”
The carbide vacuum brazed wear liner is a new product on the market. The commonly used mining wear liners currently on the market mainly include Steel Liners, Ceramic Liners, Urethane Liners, Plastic Liners, Nitronic SX, Chromium Carbide, and Rubber Liners. These products are affordable and can meet customers’ current requirements. But as the market environment changes, labor costs rise, product competition intensifies, and environmental standards improve, how to improve production efficiency and extend equipment frequency has become the industry’s focus. People are increasingly looking for high-performance products that meet these high standards. That’s why ZZ craftsman took 10 years to research and develop the vacuum brazed wear liners.
ZZ CRAFTSMAN can help clients to produce any shape of the wear liners. And we also can produce liners with curves.
The special vacuum welding process combines the tungsten carbide with the steel perfectly. The tungsten carbide can be applied to various harsh environments such as high temperatures, low cold, and high-impact occasions.
Wear liners are used to transport material in mining operations. When the material is fed into a process or discharged from it, the chutes collect, convey and prepare the material flow for the following processing phase. Chutes are used with crushers, feeders, conveyors, stackers, and grinding mills.
Many people might question how to install the liners if the carbide is brazed on it. Please check the picture below, there are the studs brazed on the backing plates, and the liners can be easily installed onto the chute directly.
For more detailed introduction, welcome to check on Chute Liner – ZZ Old Craftsman (zzcraftsman.com)
II. ZZ craftsman design, assist sample testing, assist in adjusting the carbide grade and brazing technique according to the test result, small sample testing to middle sample testing to buck production.
- Provide CAD drawings for confirmation according to customer requirements before arranging production.
- Make samples for comparing the service life with traditional wear liners.
- If there is a problem during sample testing, we will carefully analyze the rejected products to find out the problem, then adjust the sample production process and provide new samples for testing.
- After small batch sample testing, we usually recommend customers conduct medium batch sample testing and then proceed to mass production.
Through these steps, testing costs can be reduced and customers can have more confidence in our company’s products.
III.Why zz craftsman insists on the vacuum brazing for the wear liners?
Brazing technology has been around for many years, but there are still many problems that have not been solved, especially how to protect the properties of the carbide during the brazing process and prevent quality degradation. Ensuring that the carbide is not oxidized during the brazing process and how to effectively eliminate the internal stress generated by brazing has always been a difficult point in technical research.
The expansion coefficient of steel is 4 times that of carbide. During the brazing process of a large area, the big expansion coefficient difference causes huge internal stress in the carbide tiles. When the strength of the carbide tile is not strong enough to resist this internal stress, the alloy will have transverse cracks. If it cannot be eliminated well, the carbide tiles will become very brittle, and the performance of the carbide will be greatly reduced. The carbide tiles are easy to fall off, and the service life is very short.
Using vacuum brazing, the entire brazing process is completed in a vacuum environment, avoiding oxidation problems during the brazing process. At the same time, it cooperates with our company’s heat treatment process to effectively remove the internal stress of the product and solve the problem of product brittleness and carbide tile fall off.
IV.WHAT ZZ CRAFTSMAN CAN PROVIDE FOR YOU?
- We can help you to make new designs to improve the current products’ working efficiency;
- We can help you to solve the wear problem that is occurring from the current material;
- We can help you adjust the production technique if any problem occur during the testing
- We can provide suggestions if customers do not have good ideas on the improvement.
V. Application of wear liner:
Ideal for iron ore transfer chutes in Australia” or “Perfect for copper ore processing in Peru”.
Applications involving severe sliding abrasion and medium impact, such as
- Chutes
- Deflector chutes
- Ore Handling Systems
- Liner Plates
- Hoppers
- Conveyor skirts
- Conveyor dragplates
- HPGRfeed cheek plates
- HPGR flange
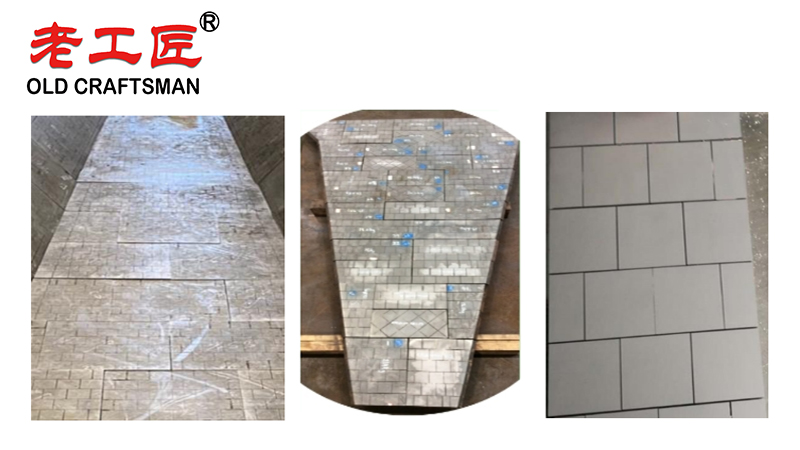

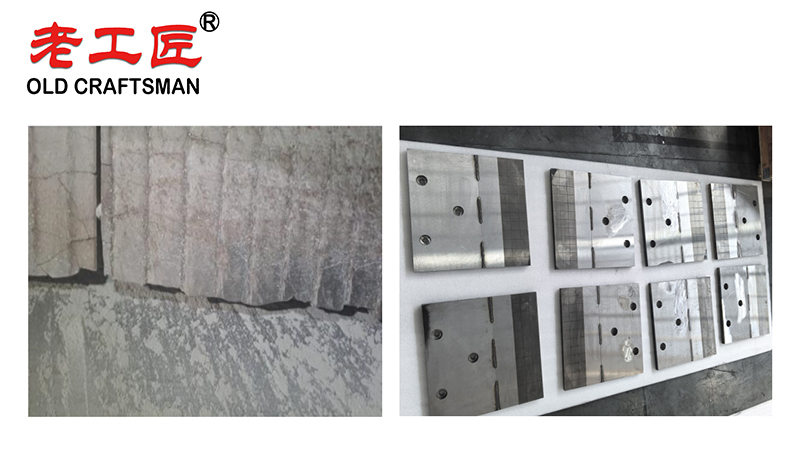
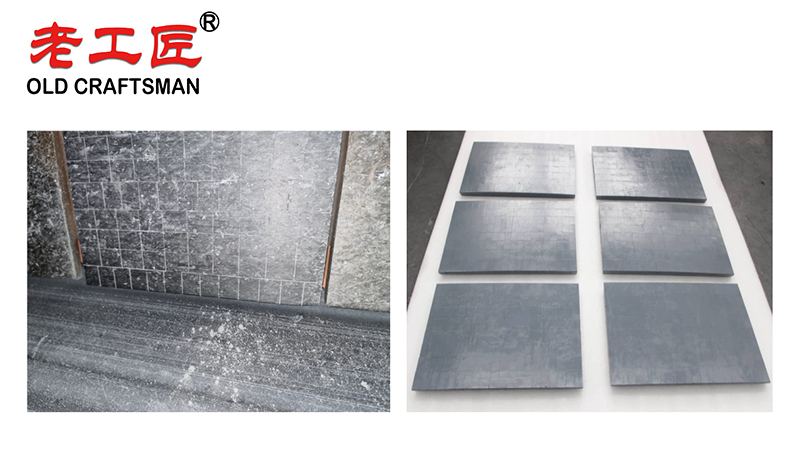
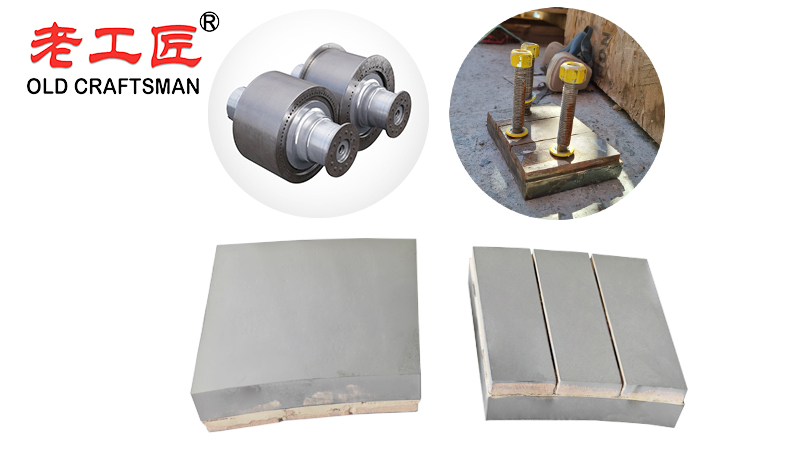
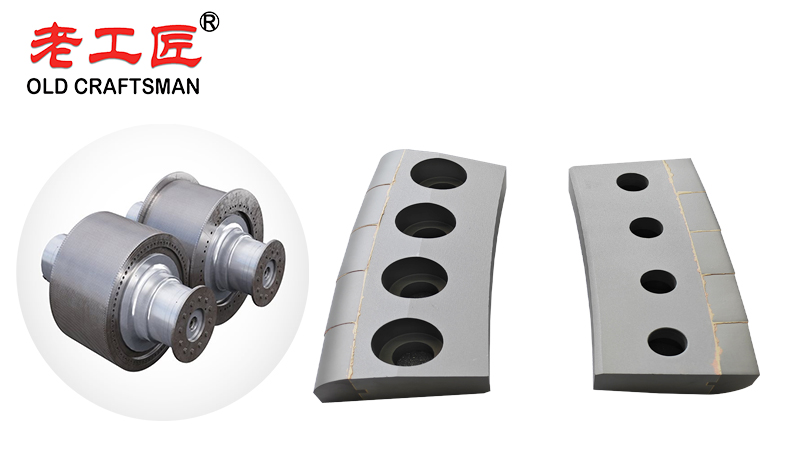
Wear Liners Mining
Chute Lining
Chute Wear Liners
Chute Liner Material
Chute Liners Mining
Conveyor Chute Liners
Mining Hopper
Hopper Plate
Hopper Material Handling
Hopper Feeder Mining
High Pressure Grinding Rolls
High Pressure Grinding Rollers
High Pressure Grinding Roll
HPGR
HPGR Weir
HPGR Mining
Carbide Wear Plate
Mining Wear Plate
HPGR Wear Plate
Mining Wear Plates
Wear Plate For Mining
HPGR Edge Block
Edge Block HPGR
HPGR Flange
HPGR Cheek Plate
Carbide Wear Liner
Vacuum Brazed Wear Liner
Lining Plate
Mining And Quarrying Wear Liner
HPGR Liners
Welcome to contact us for the customized design!
Zhuzhou Old Craftsman Precision Alloy Co., Ltd. could make tungsten carbide wear parts and make your equipment use life is tens of times longer than before! We specialize in providing customized carbide wear products solutions to meet the demanding requirements of industries such as aerospace, automotive, mining, and precision machining.
VI. FAQ of the wear liner
Q: What are your main products for tungsten carbide brazing?
A: Our advantage products are brazed carbide wear plates, brazed carbide crushing hammerheads, brazed carbide nozzles, brazed carbide scrape blades, brazed liners for refractory brick mold, and any of customized brazed items.
Q: Do you have an OEM&ODM option?
A: Yes, we have. Customized product is our advantage.
Q: What is your MOQ?
A: It depends on the exact product; there usually is no MOQ limitation for standard products.
Q: How long have you been producing this product?
A: We have been doing research and development, and producing carbide brazing products for over 8 years, gaining much successful experience in it.