Hard alloys, also known as cemented carbides or hard metals, are composite materials renowned for their exceptional hardness, wear resistance, and strength. These properties make them indispensable in the manufacturing of wear-resistant components used across various industries, including mining, machining, aerospace, and automotive. This essay explores the composition, properties, and applications of hard alloys in wear-resistant parts, highlighting their significance in modern engineering.
Composition and Properties of Hard Alloys
Hard alloys are typically composed of a hard phase, such as tungsten carbide (WC), and a binder phase, commonly cobalt (Co) or nickel (Ni). The hard phase provides the material with its characteristic hardness and resistance to abrasion, while the binder phase enhances toughness and prevents brittleness. The combination of these two phases results in a material that can withstand extreme mechanical stress and prolonged exposure to abrasive environments.
The key properties of hard alloys include high hardness (often exceeding 90 HRA on the Rockwell scale), excellent wear resistance, good thermal stability, and resistance to deformation under high pressure. These attributes stem from the microstructure of the material, where fine carbide particles are embedded in a ductile metal matrix. By adjusting the proportion of the binder and the grain size of the carbide, manufacturers can tailor the alloy’s properties to suit specific applications.
Applications in Wear-Resistant Components
Hard alloys are widely employed in components that experience significant wear due to friction, abrasion, or erosion. Below are some prominent examples of their applications:
1. Cutting Tools: In the machining industry, hard alloy tools such as drills, milling cutters, and lathe inserts are used to cut, shape, and finish metals and other materials. Their ability to maintain sharpness and resist wear even at high temperatures makes them superior to traditional steel tools, improving efficiency and precision in manufacturing processes.
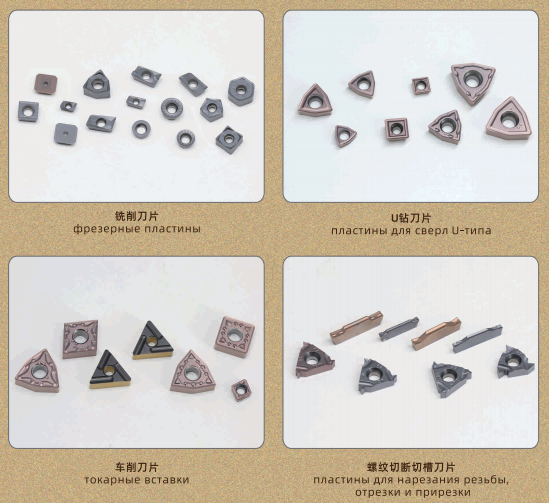
2. Mining and Drilling Equipment: The harsh conditions of mining and oil exploration demand materials that can endure constant abrasion from rock and soil. Hard alloys are used in drill bits, crusher teeth, and wear plates, where they extend the service life of equipment and reduce downtime caused by component failure.
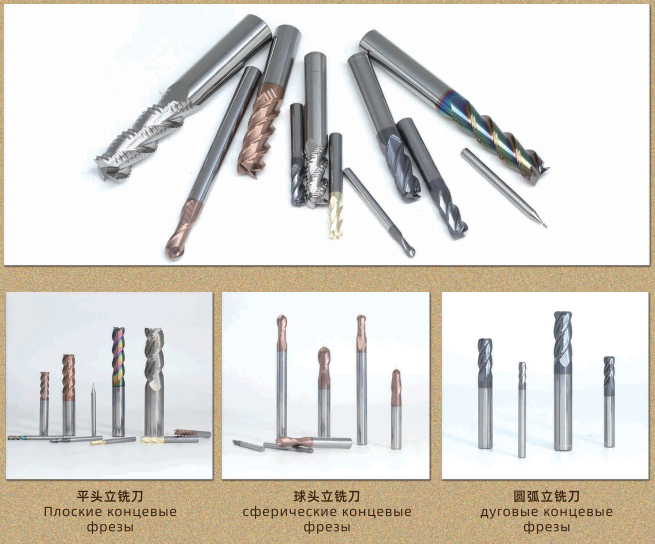
3. Wear Parts in Heavy Machinery: Components like nozzles, bearings, and valve seats in heavy machinery are subjected to continuous friction and impact. Hard alloys provide the durability needed to withstand these conditions, ensuring reliable performance in industries such as construction and agriculture.
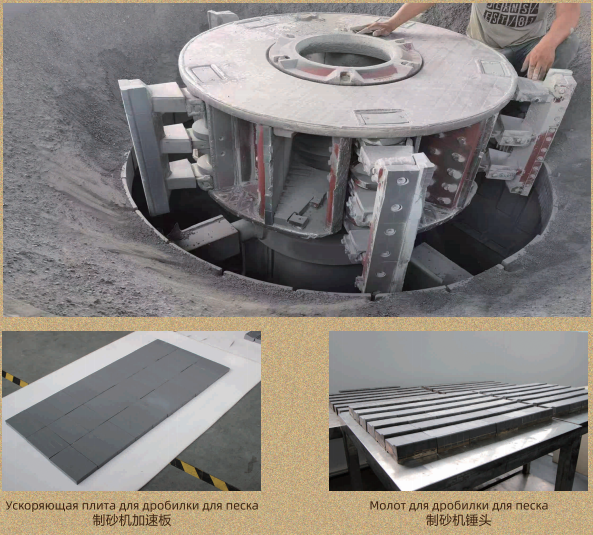
4. Aerospace and Automotive Components: In aerospace, hard alloys are used in turbine blades and other parts exposed to high wear and heat. Similarly, in the automotive sector, they are found in engine components, brake systems, and transmission parts, where longevity and resistance to wear are critical.
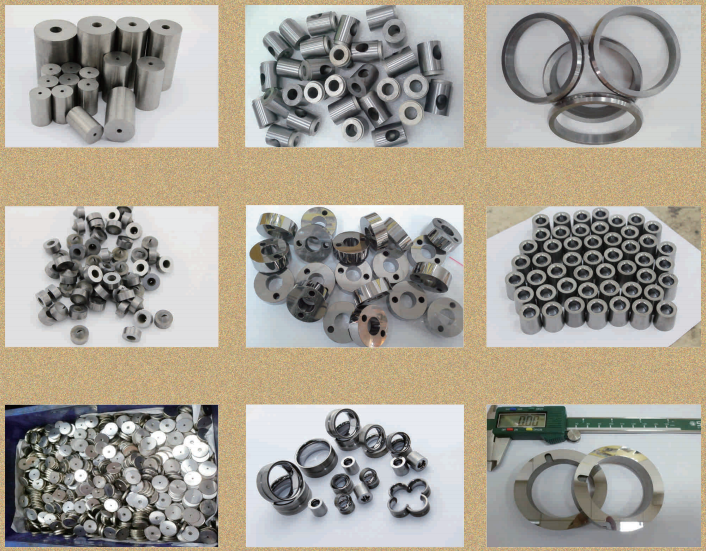
Advantages and Challenges
The primary advantage of hard alloys in wear-resistant applications is their ability to significantly extend the lifespan of components, reducing maintenance costs and improving operational efficiency. Their versatility also allows them to be engineered for specific needs, balancing hardness and toughness as required.
However, hard alloys are not without challenges. Their high hardness makes them difficult and costly to machine, often requiring diamond tools or advanced grinding techniques. Additionally, while they excel in wear resistance, they may be prone to cracking under extreme impact unless properly designed with sufficient binder content.
Future Prospects
Advancements in material science continue to enhance the performance of hard alloys. Innovations such as nano-structured carbides, alternative binders (e.g., iron-based alloys), and coatings like titanium nitride (TiN) are pushing the boundaries of their wear resistance and toughness. These developments promise to expand their applications further, particularly in emerging fields like additive manufacturing and renewable energy systems.
Conclusion
Hard alloys play a pivotal role in the production of wear-resistant components, offering a unique combination of hardness, strength, and durability. From cutting tools to heavy machinery parts, their ability to withstand abrasive and erosive forces has made them a cornerstone of industrial engineering. As technology evolves, hard alloys are likely to remain at the forefront of materials used to combat wear, driving efficiency and innovation across multiple sectors.
“Zhuzhou Old Craftsman Precision Alloy Co., Ltd. could make tungsten carbide crusher hammer and make your crusher hammer use life is tens of times longer than before! We specialize in providing customized carbide solutions to meet the demanding requirements of industries such as aerospace, automotive, mining, and precision machining.”
Blet scarper Brazing brazingprocess CARBDIE HAMMER carbide Carbide belt scraper carbidebrazing carbide hammer Crusher CRUSHER HAMMER Informational Internal stress metal mining mold operate Refractory Brick Mold Secondary belt cleaner scraper stresses VSI VSI crusher wear plates welding work