When comparing the service life of carbide blades in a concrete mixer to blades made from other materials, carbide blades generally have a longer lifespan.
Carbide, often referring to tungsten carbide, is an extremely hard and wear-resistant material. In the context of concrete mixers, where blades are subjected to constant abrasion from sand, gravel, and cement, carbide blades outperform alternatives like steel or cast iron. Standard steel blades, while tough, wear down more quickly due to their lower hardness and susceptibility to abrasion. Cast iron blades, though durable, are prone to cracking under heavy impact and also wear faster than carbide.
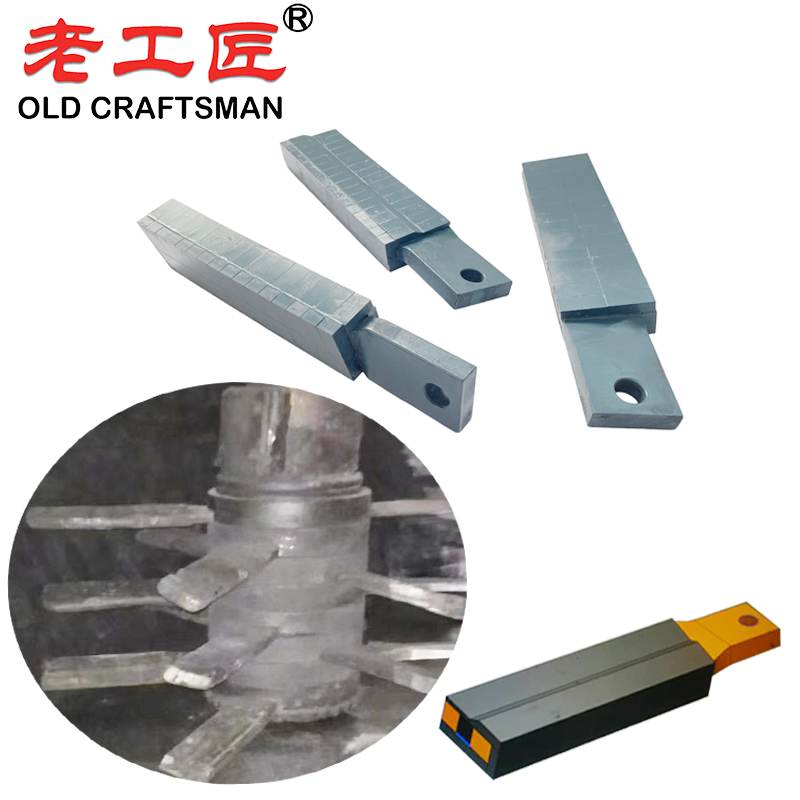
The longer service life of carbide blades in concrete mixers compared to blades made from other materials can be attributed to several key factors rooted in material properties and operational conditions.
✦Superior Hardness:
Carbide, typically tungsten carbide, is an exceptionally hard material, often ranking above 9 on the Mohs hardness scale (close to diamond at 10). In contrast, steel (even hardened steel) and cast iron have lower hardness levels, usually ranging between 4 and 6 on the Mohs scale. In a concrete mixer, blades are constantly grinding against abrasive aggregates like sand, gravel, and stone. The superior hardness of carbide allows it to resist wear and maintain its shape far longer than softer materials.
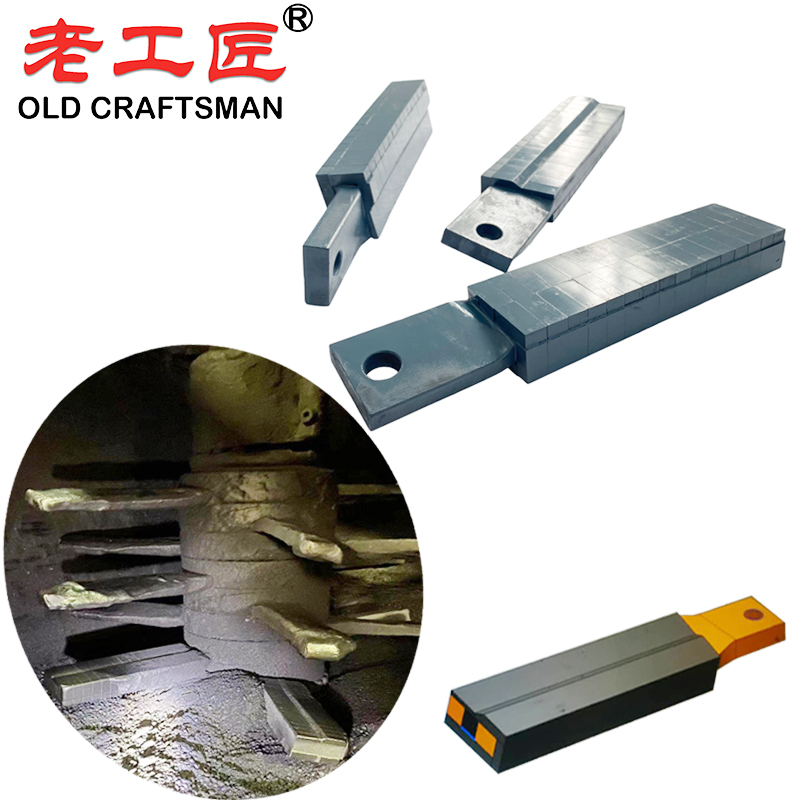
✦Wear Resistance:
The abrasive nature of concrete components causes significant material loss in blades over time. Carbide’s composition—combining tungsten and carbon—creates a structure that is highly resistant to abrasion. Steel blades, while strong, erode more quickly under the same conditions because their surface is less able to withstand the scratching and scouring action of aggregates. Cast iron, though tougher than some steels, also wears down faster due to its relatively brittle nature and lower abrasion resistance.
✦Impact Toughness with Reinforcement:
While pure carbide can be brittle, modern carbide blades in mixers are often engineered as carbide-tipped or reinforced with a tough substrate (like steel). This hybrid design combines carbide’s wear resistance with the ductility of steel, allowing the blades to absorb the mechanical shocks and vibrations of mixing without cracking. Pure steel or cast iron blades, by comparison, either deform (steel) or fracture (cast iron) more readily under repeated impact, shortening their lifespan.
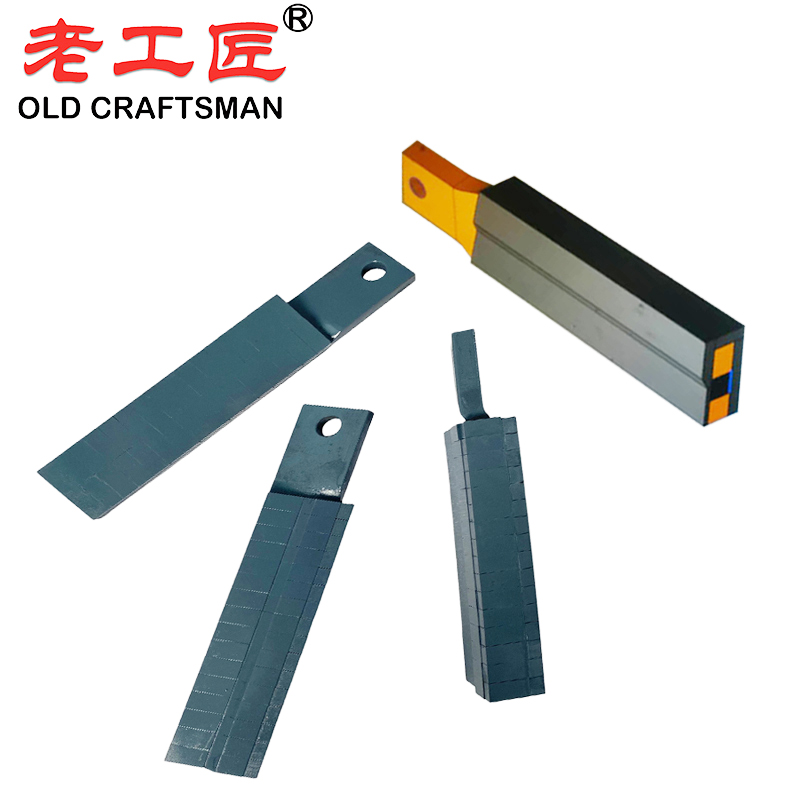
✦Thermal Stability:
Friction during mixing generates heat, which can soften or degrade some materials. Carbide maintains its hardness and structural integrity even at elevated temperatures, whereas steel can lose hardness if overheated, accelerating wear. This thermal stability contributes to carbide’s prolonged usability.
✦Operational Efficiency:
Because carbide blades wear more slowly, they maintain their cutting and mixing efficiency over time. Steel or cast iron blades, as they erode, become less effective, requiring more frequent replacement to maintain performance. This consistent efficiency indirectly extends the practical service life of carbide blades in real-world applications.
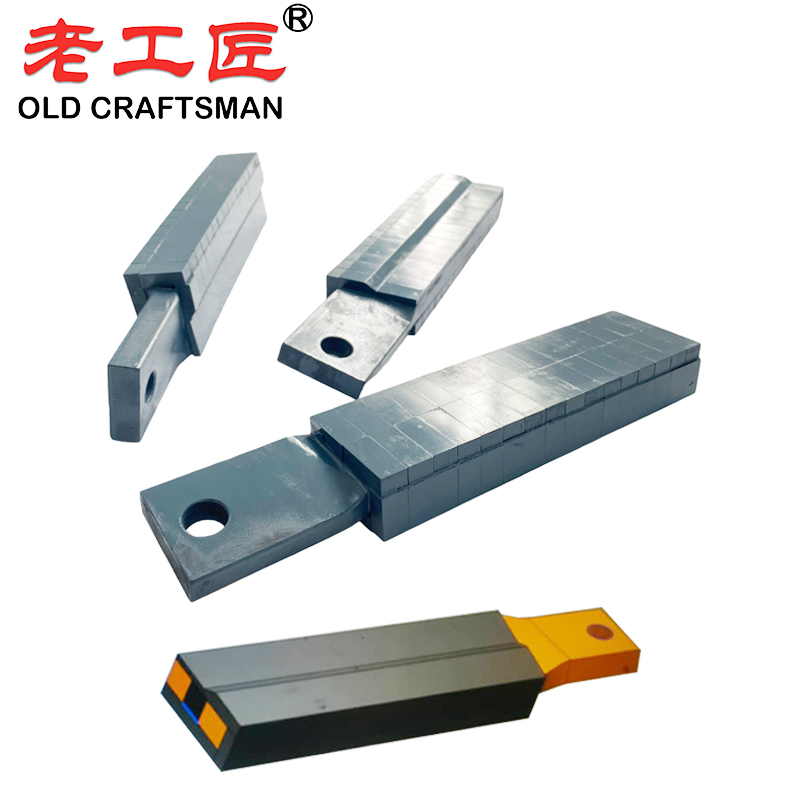
In summary, the extended lifespan of carbide blades in concrete mixers stems from their exceptional hardness, wear resistance, tailored toughness, corrosion resistance, and thermal stability. These properties allow them to outlast alternatives like steel or cast iron by a significant margin, often enduring 5 to 10 times longer in demanding conditions, making them a preferred choice despite their higher initial cost.
“Zhuzhou Old Craftsman Precision Alloy Co., Ltd. could make tungsten carbide wear parts and make your equipment use life is tens of times longer than before! We specialize in providing customized carbide wear products solutions to meet the demanding requirements of industries such as aerospace, automotive, mining, and precision machining.”
Blet scarper Brazing brazingprocess CARBDIE HAMMER carbide Carbide belt scraper carbidebrazing carbide hammer Crusher CRUSHER HAMMER Informational Internal stress metal mining mold operate Refractory Brick Mold Secondary belt cleaner scraper stresses VSI VSI crusher wear plates welding work