Tungsten carbide crusher hammers also with other expresses, like hard alloy crusher hammers, hard alloy crusher hammers, cemented carbide crusher hammer, carbide alloy crusher hammer, hard metal crusher hammer.
Tungsten carbide crusher hammers can last significantly longer—sometimes claimed to be “tens of times” longer—than high chrome crusher hammers due to a combination of material properties that make tungsten carbide exceptionally suited for the harsh conditions of crushing applications. While the exact factor of durability (e.g., “tens of times”) may vary depending on specific conditions and may involve some exaggeration for emphasis, the superior wear resistance and overall performance of tungsten carbide are well-supported by its characteristics. Here’s a detailed explanation:

1. Exceptional Hardness
- Tungsten Carbide: Tungsten carbide (WC) is a ceramic-like material with a Mohs hardness of 9–9.5, close to that of diamond (10). This extreme hardness allows it to resist abrasive wear far better than most metals, including high chrome alloys.
- High Chrome: High chrome cast iron, typically an alloy of iron with 12–30% chromium, has a hardness of around 600–700 HV (Vickers), depending on heat treatment and composition. While this is impressive for a metal, it is significantly softer than tungsten carbide, which can exceed 1500 HV. The greater hardness of tungsten carbide means it can withstand the grinding and scraping action of crushing materials for much longer without significant material loss.
2. Superior Wear Resistance
- Tungsten Carbide: The combination of tungsten and carbon forms a compound that resists abrasion, erosion, and impact wear exceptionally well. In crusher hammers, where materials like rock, ore, or gravel constantly abrade the surface, tungsten carbide’s ability to maintain its integrity under such conditions dramatically extends its lifespan.
- High Chrome: High chrome alloys rely on the formation of chromium carbides within an iron matrix for wear resistance. While these carbides are hard, the surrounding iron matrix is softer and more prone to wear, especially under high-stress abrasion or impact. Once the matrix erodes, the carbides can become exposed and dislodged, accelerating wear. Tungsten carbide, being a more uniform and denser material, doesn’t suffer from this vulnerability to the same degree.
3. Impact Resistance with Proper Design
- Tungsten Carbide: Pure tungsten carbide is brittle, but in crusher hammers, it is typically used as a composite, such as in a cemented carbide form (e.g., with cobalt or nickel as a binder) or as inserts within a tougher steel base. This combination balances hardness with sufficient toughness to absorb the repeated impacts of crushing without fracturing. Manufacturers often engineer these hammers to optimize this synergy, ensuring durability under dynamic loads.
- High Chrome: High chrome cast iron offers good toughness due to its metallic nature, but its brittleness increases with higher chromium content, making it susceptible to cracking or chipping under heavy impact. While it performs well in moderate conditions, it struggles compared to properly designed tungsten carbide composites when subjected to extreme forces or prolonged use.
4. Corrosion and Chemical Resistance
- Tungsten Carbide: Tungsten carbide is highly resistant to corrosion and chemical degradation, even in harsh environments like those involving wet or acidic materials. This stability prevents surface pitting or weakening that could accelerate wear.
- High Chrome: Although chromium improves corrosion resistance in high chrome alloys, they are still more prone to rust and chemical attack than tungsten carbide, especially in wet crushing applications. Over time, this can degrade the hammer’s surface and reduce its lifespan.
5. Thermal Stability
- Tungsten Carbide: Tungsten carbide maintains its hardness and strength at elevated temperatures, which can occur due to friction during crushing. This thermal stability ensures consistent performance over long periods.
- High Chrome: High chrome alloys can soften or lose hardness at high temperatures, reducing their effectiveness in applications where heat buildup is significant. This makes them less durable in prolonged, high-intensity crushing operations.
6. Real-World Performance
- In practical applications, tungsten carbide crusher hammers are often reported to last 2–10 times longer than high chrome hammers, depending on the material being crushed, hammer design, and operating conditions. For example, when crushing highly abrasive materials like granite or quartz, tungsten carbide’s advantages become even more pronounced. The claim of “tens of times longer” might reflect optimal scenarios (e.g., crushing extremely abrasive materials where high chrome fails quickly) or marketing hyperbole, but the underlying trend of significantly extended lifespan is consistent with the material properties.
Why Not Always “Tens of Times”?
- The exact lifespan difference depends on factors like the crusher’s operating conditions, the material being processed, and the specific alloy compositions. High chrome hammers can perform adequately in less abrasive or lower-impact applications, narrowing the gap. However, in high-wear scenarios, tungsten carbide’s advantages are undeniable, often leading to multiples of the lifespan of high chrome—sometimes approaching or exceeding 10 times under ideal conditions.
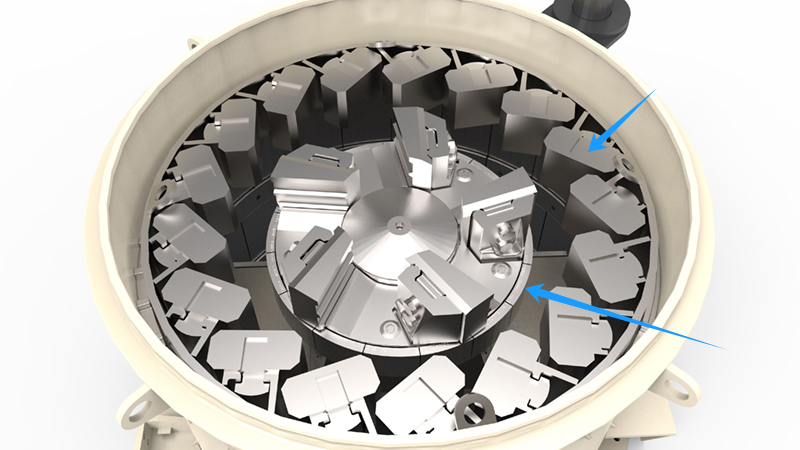
Zhuzhou Old Craftsman Precision Alloy Co., Ltd. could make tungsten carbide crusher hammer and make your crusher hammer use life is tens of times longer than before!
Conclusion
Tungsten carbide crusher hammers outlast high chrome hammers due to their unparalleled hardness, wear resistance, and ability to maintain performance under abrasion, impact, and harsh environmental conditions. While “tens of times longer” may not always be a precise figure, the dramatic improvement in durability stems from tungsten carbide’s fundamental material superiority, making it a preferred choice for demanding crushing tasks.
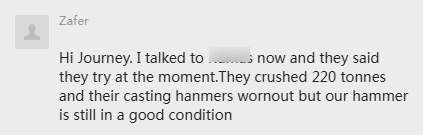