Choosing the right wear parts for crushers is crucial to maximizing efficiency and minimizing downtime. Recently, we delivered a batch of vacuum brazed tungsten carbide hammerheads to a client, and the growing trust in tungsten carbide materials is evident. More crusher operators are switching to our high-performance wear parts, recognizing their clear advantages and the positive market outlook.
So, what makes tungsten carbide hammerheads stand out? Why are they gaining popularity, and how does the vacuum brazing process enhance wear resistance? Let’s explore these questions.
Horizontal crusher hammer picture display
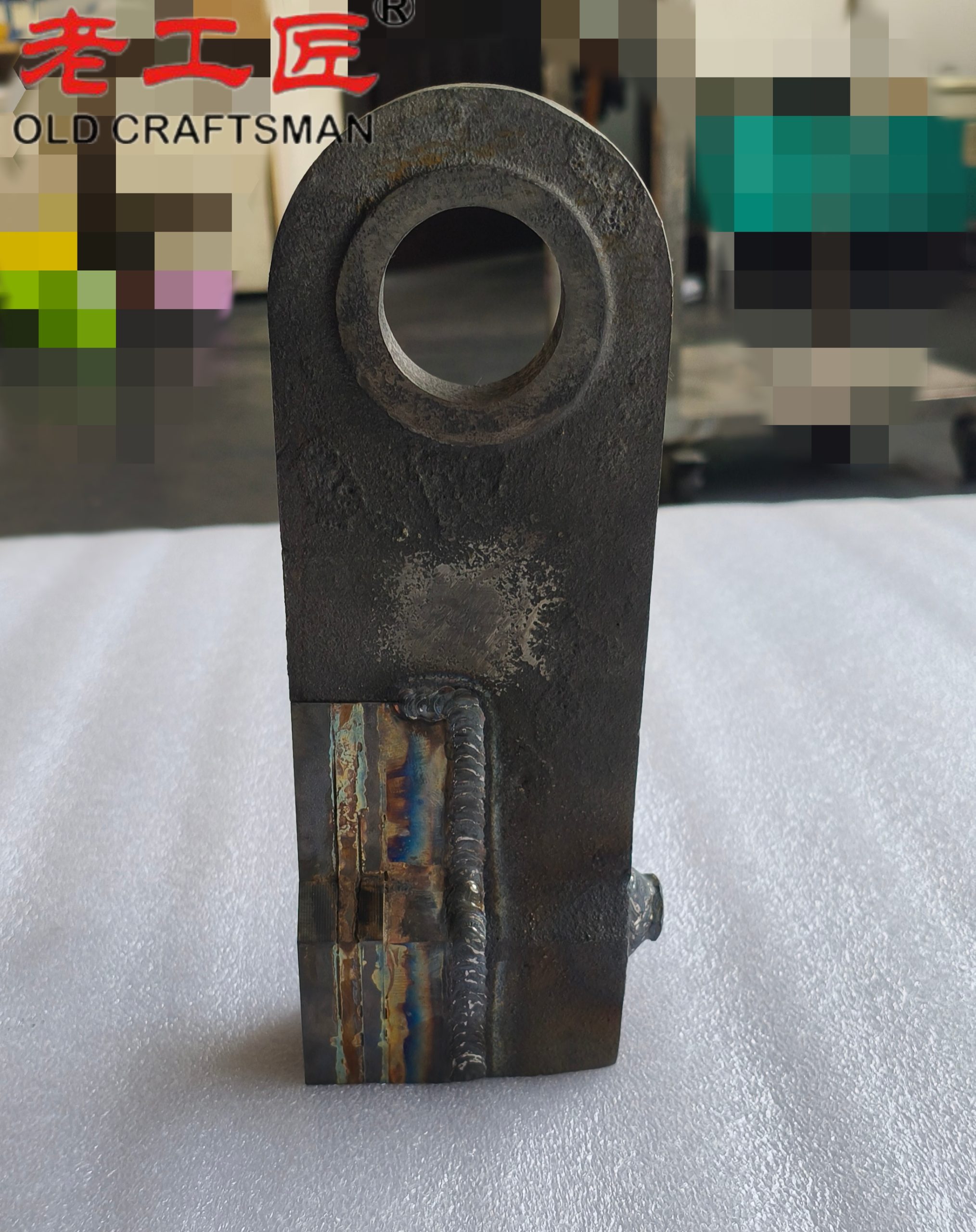
Benefits of Vacuum Brazed Tungsten Carbide Hammer
The vacuum brazed tungsten carbide hammerhead shown above was custom-made for a horizontal crusher. The client previously used standard high-chromium cast iron Cr26 hammerheads, which lasted only 16-20 hours per side. These parts wore down quickly, reducing crushing efficiency and requiring frequent replacements, leading to extended downtime.
We developed a tailored solution: a vacuum brazed tungsten carbide hammerhead. Its key advantages include:
- High-Quality Material: Made from vacuum brazed tungsten carbide with a Mohs hardness of 8.5-9, offering superior wear resistance and longer life than traditional materials.
- Optimized Design: Engineered for even wear and efficient material flow, improving performance and reducing costs.
- Versatile Applications: Suitable for crushing hard, abrasive materials like limestone, coal, and ores.
- Eco-friendly and Cost-Effective: Reduces downtime, minimizes waste, and lowers labor costs.
How Vacuum Brazing Enhances Durability?
Vacuum brazing is an advanced process that fuses tungsten carbide particles with a strong base material in a high-vacuum, high-temperature environment. This technique delivers several key benefits:
- Superior Wear Resistance: Tungsten carbide’s hardness makes the hammerhead highly resistant to wear, extending its lifespan compared to conventional materials.
- Strong Bonding: The vacuum environment removes impurities, ensuring a robust bond between the carbide layer and base material, improving overall durability.
- Longer Life: Our vacuum brazed hammerheads last significantly longer than traditional ones, reducing the need for replacements and cutting maintenance costs.
Why Choose Our Old Craftsman Tungsten Carbide Hammers?
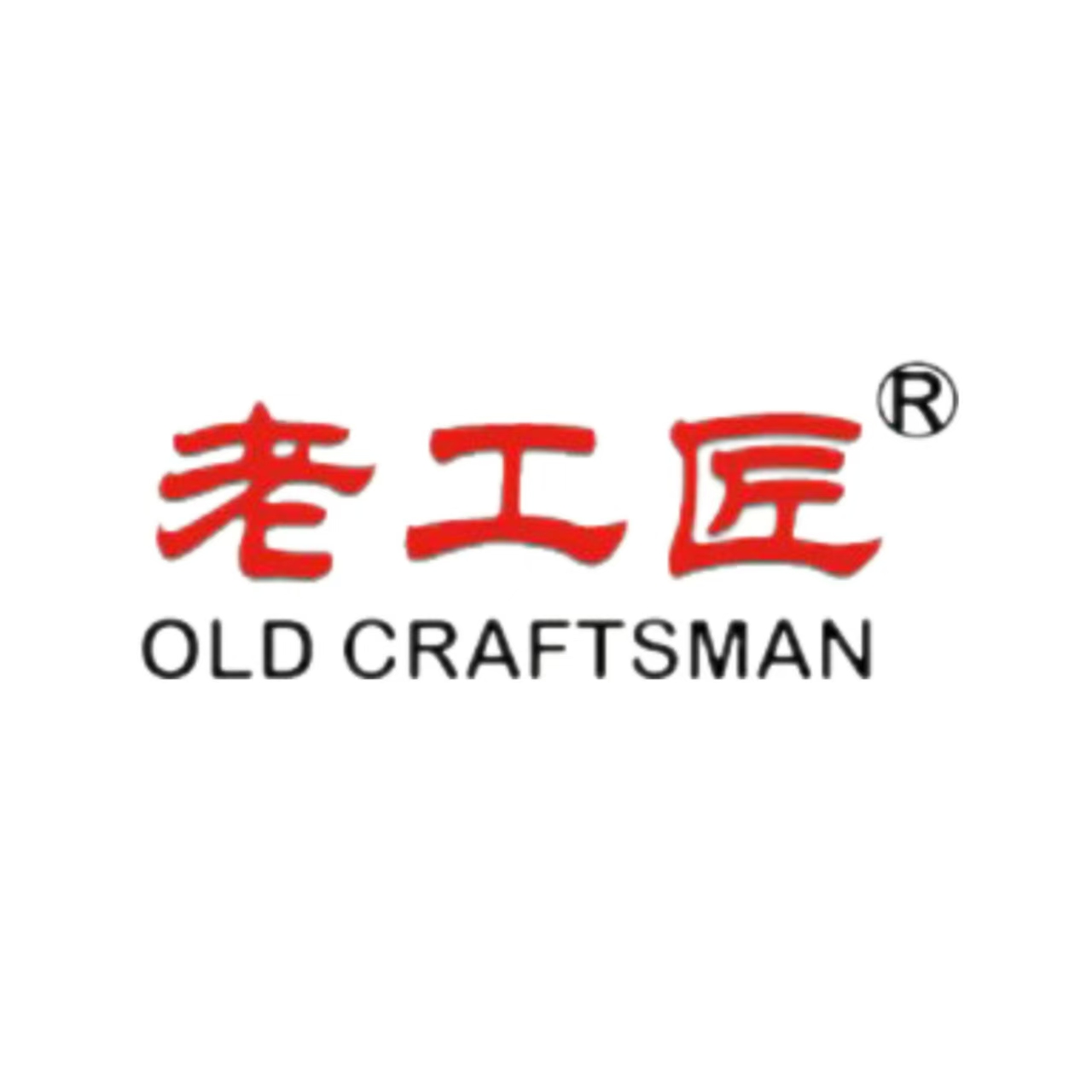
In crushers, minimizing downtime is critical. Our vacuum brazed tungsten carbide hammerheads offer a durable, efficient solution:
- Lower Maintenance Costs: With reduced wear and longer service life, our hammerheads require fewer replacements, saving on maintenance and downtime.
- Increased Productivity: Superior wear resistance ensures consistent performance and fewer breakdowns, boosting productivity.
- Sustainability: Fewer replacements mean less waste and more sustainable operations.
Conclusion: The Future of Crusher Wear Parts
The growing adoption of tungsten carbide hammerheads reflects the industry’s shift toward durability and cost-efficiency. By choosing our vacuum brazed tungsten carbide hammerheads, operators can reduce downtime, enhance performance, and lower long-term maintenance costs.
For more information on how our wear parts can improve your crusher’s performance, contact us feel free.
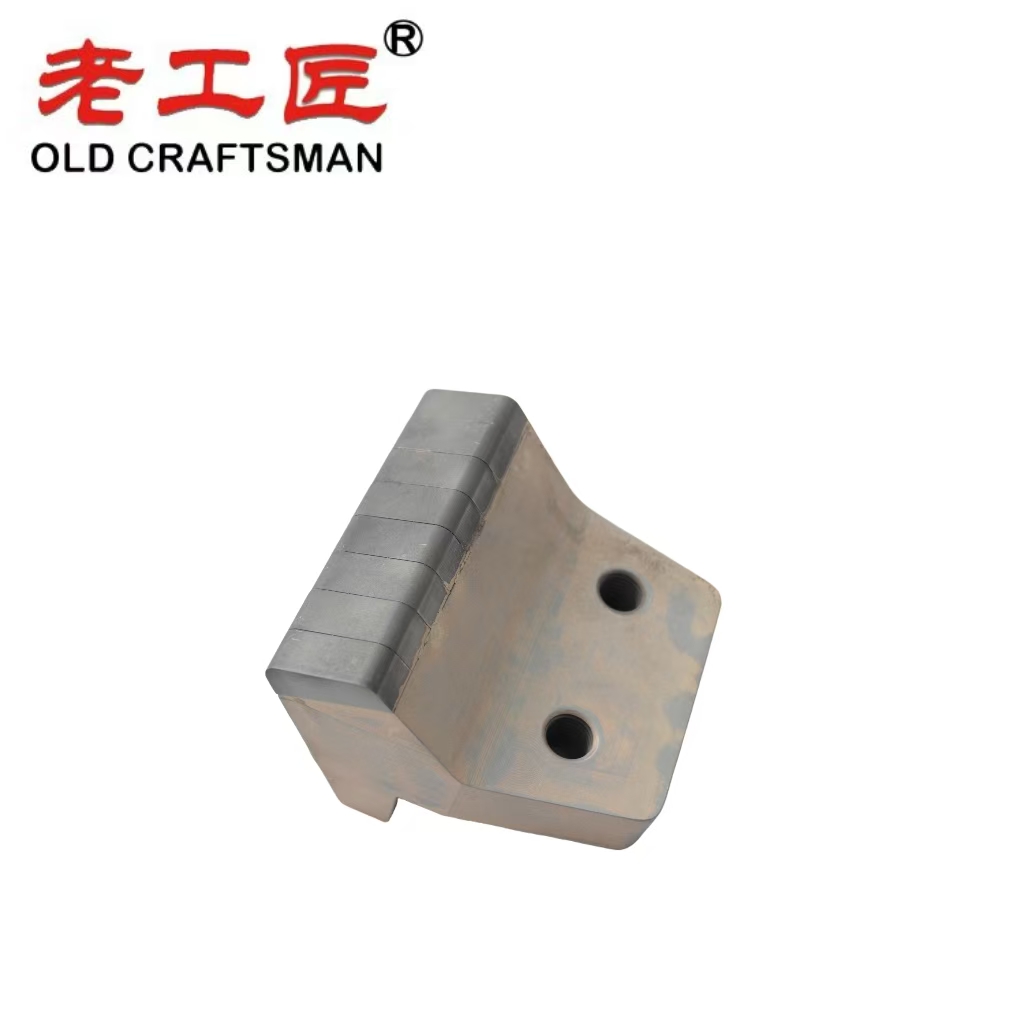
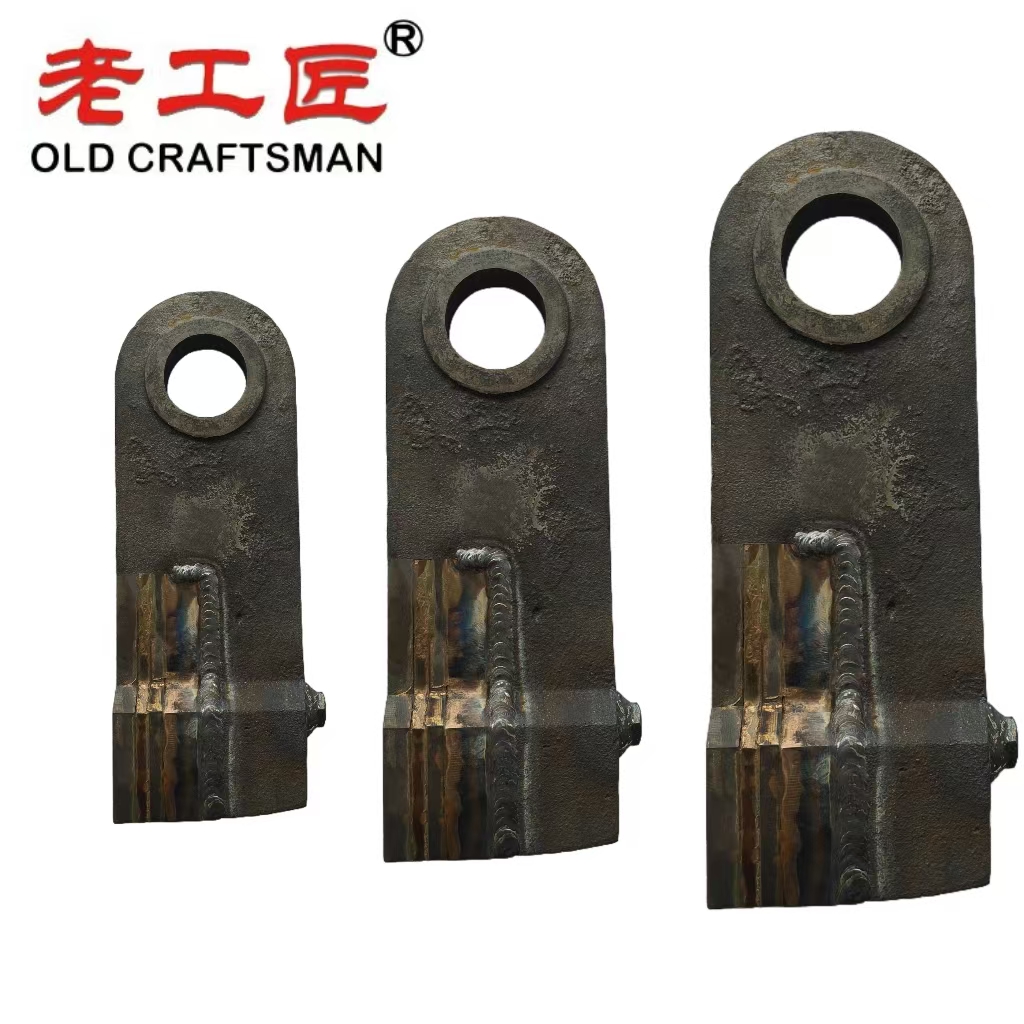