With the rapid development of the industrial market and technology, we can see that tungsten carbide wear plates have demonstrated excellent adaptability in the application of HPGR (High-Pressure Grinding Rolls) feed chutes. This is because the feed chutes are constantly exposed to high-intensity material impacts and wear, and conventional materials often fail to meet the operational demands. Tungsten carbide wear plates, with their high hardness and superior wear resistance, effectively reduce wear rates and significantly extend equipment maintenance intervals, thus lowering operational costs. A lot professional teams claims that by using tungsten carbide wear plates, maintenance costs for HPGR feed chutes can be reduced by 25%, and equipment downtime can be cut by 30%.
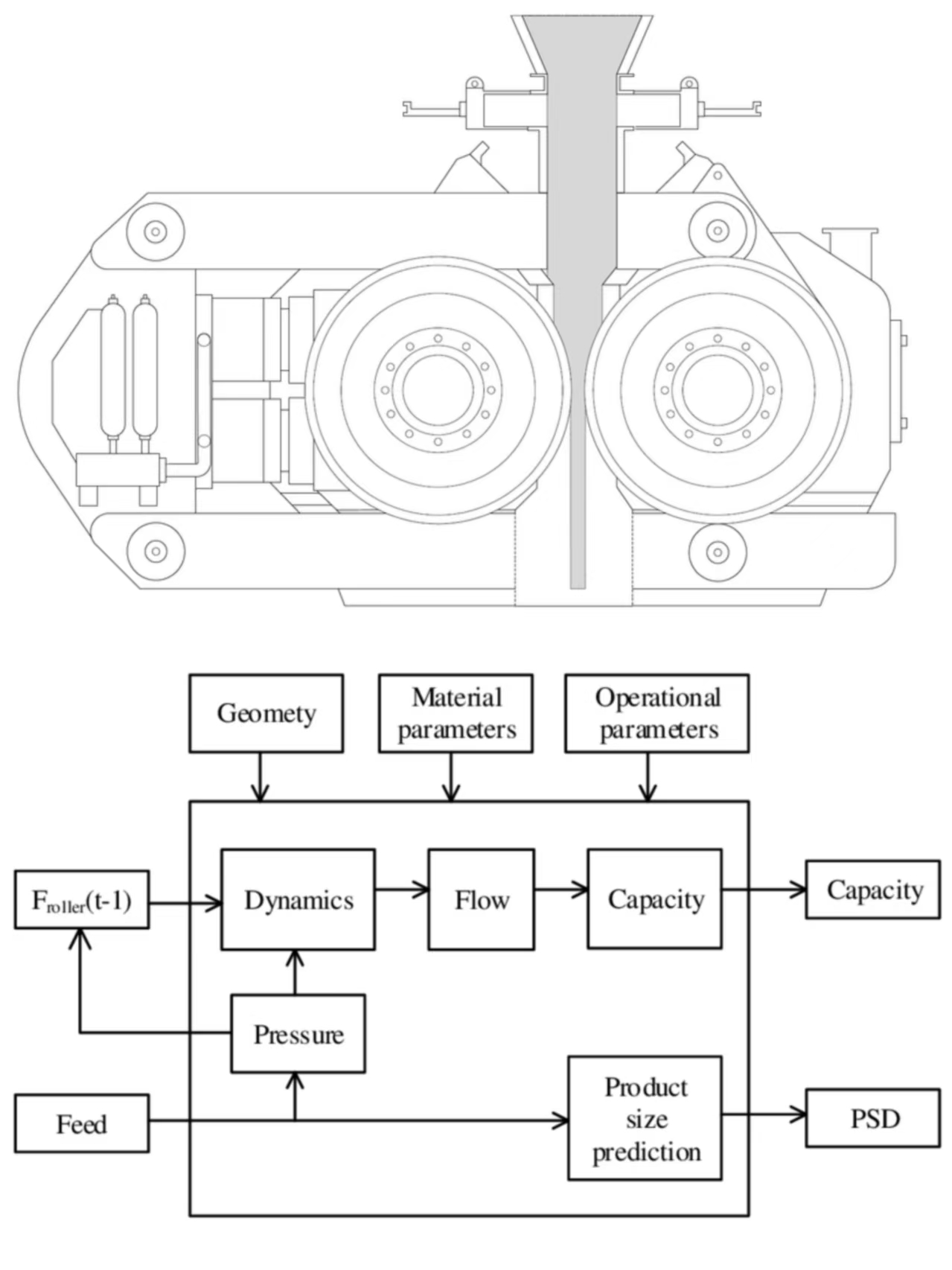
Zhu Zhou Old Craftsman Precision Alloy Co., Ltd. has enhanced the performance of these wear plates by using a vacuum brazing process to bond tungsten carbide with a substrate. With the widespread promotion of this technology in the mining equipment field, the reliability and economic benefits of HPGR equipment have significantly improved.
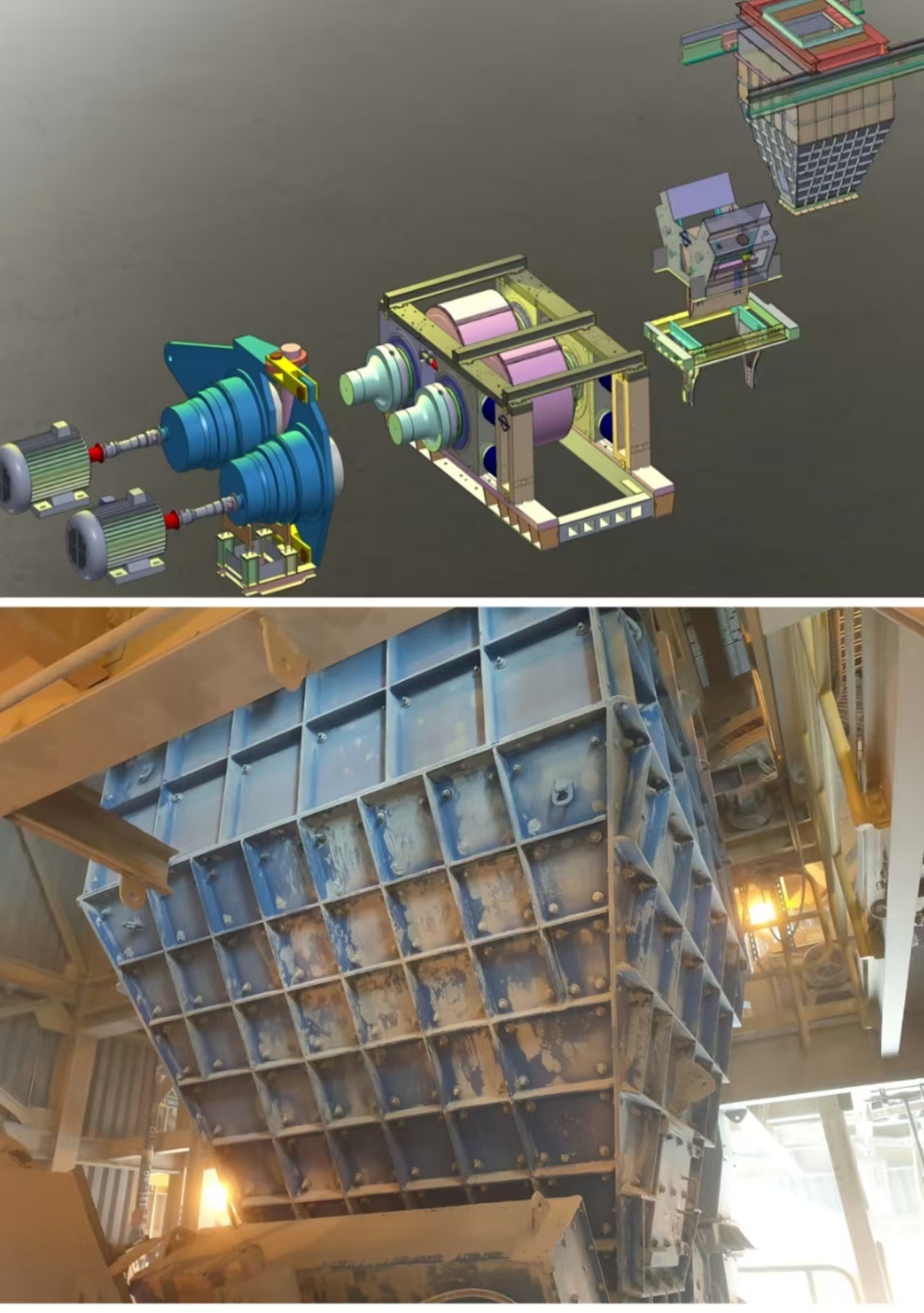
So, why are more and more companies choosing tungsten carbide wear liner ?
First, it’s essential to understand that tungsten carbide is a material made from tungsten carbide (WC) hard particles combined with a metal binder (such as cobalt) through powder metallurgy. It is known for its high hardness, wear resistance, and good toughness, often referred to as the “teeth of modern industry.” Due to its extremely high hardness and wear resistance, tungsten carbide has quickly and widely been applied in various industrial fields since its introduction.
The applications of tungsten carbide are vast and cover almost every area requiring high hardness and wear resistance, including, but not limited to, machining tools such as turning, milling, and drilling tools in mechanical manufacturing; wear plates and drill bits used in mining equipment; high-temperature resistant parts in aerospace; and dental drills and surgical tools in the medical industry.
What makes vacuum-brazed tungsten carbide so versatile and suitable for such a broad range of fields? Let’s explore this from an academic research perspective to understand its unique properties.
Hardness and Wear Resistance of Tungsten Carbide
Tungsten carbide is one of the hardest materials known, with a Vickers hardness typically between 1700 and 2000 HV, which is close to that of natural diamond. This hardness makes it highly effective in resisting wear. In applications such as metal cutting and impact drilling, tungsten carbide tools can maintain a sharp cutting edge for extended periods, significantly prolonging the service life of equipment.
A study published in the Chinese journal Rare Metals and Hard Alloys explored the performance enhancement of high-entropy alloys with added tungsten carbide. It found that an appropriate amount of tungsten carbide could improve the hardness of the alloy, while excessive addition could lead to increased porosity and reduced hardness. This research offers new directions for the application of tungsten carbide in composite materials. Zhu Zhou Old Craftsman Precision Alloy Co., Ltd. has precisely optimized the amount of tungsten carbide used to maximize the hardness of its alloys.
High-Temperature Performance and Corrosion Resistance
Tungsten carbide exhibits excellent high-temperature stability, with a melting point as high as 2870°C. Even in high-temperature environments, it can maintain outstanding hardness and strength, making it an ideal material for aerospace and high-temperature industrial applications. Furthermore, tungsten carbide is highly resistant to acids, alkalis, and other chemicals, enabling it to remain stable in harsh environments for extended periods.
Another study explored the preparation of ultra-fine tungsten carbide powder using mechanical ball milling, which significantly improved the performance of the powder. This technology has important implications for the manufacturing of high-temperature wear-resistant components.
Customizable Material Properties
By adjusting the particle size of the tungsten carbide, the type and ratio of the binder, the material’s properties can be customized to meet specific application needs. For instance, increasing the binder content can enhance the material’s toughness, making it suitable for impact-resistant applications, while reducing the binder content improves the hardness and wear resistance, making it ideal for high-precision cutting tools.
Environmental Impact and Sustainability
With the growing emphasis on environmental awareness, the recycling of tungsten carbide waste has become a research focus. For example, a method using D309 resin to recover tungsten from arsenic-containing tungsten polytungstic acid solutions was introduced in a journal. This technology not only reduces production costs but also effectively reduces resource waste and environmental pollution, contributing to the sustainable development of tungsten carbide.
Although tungsten carbide has already played an irreplaceable role in many industries, researchers are still exploring ways to further optimize its performance. For example, using nanotechnology to produce ultra-fine tungsten carbide particles can significantly enhance its hardness and toughness. Additionally, adding high-entropy alloys or other novel binder materials can improve its overall performance.
In conclusion
Tungsten carbide, with its unique hardness, wear resistance, and versatility, occupies a crucial position in modern industry. In the future industrial development, choosing vacuum-brazed tungsten carbide hard alloy wear products will become a new trend in the industry.
Looking to the future,in order to let more customers choose and trust us, our Old Craftsman Precision Alloy Co., Ltd. will continue to explore the potential of tungsten carbide materials and continuously innovate technology, not only to improve the wear-resistant materials of high-pressure roller grinding mills,let more companies feel the convenience brought by vacuum brazing tungsten carbide wear-resistant materials in HPGR; it will also bring revolutionary changes to more industries and continue to provide strong support and solutions for the field of efficient industrial development.
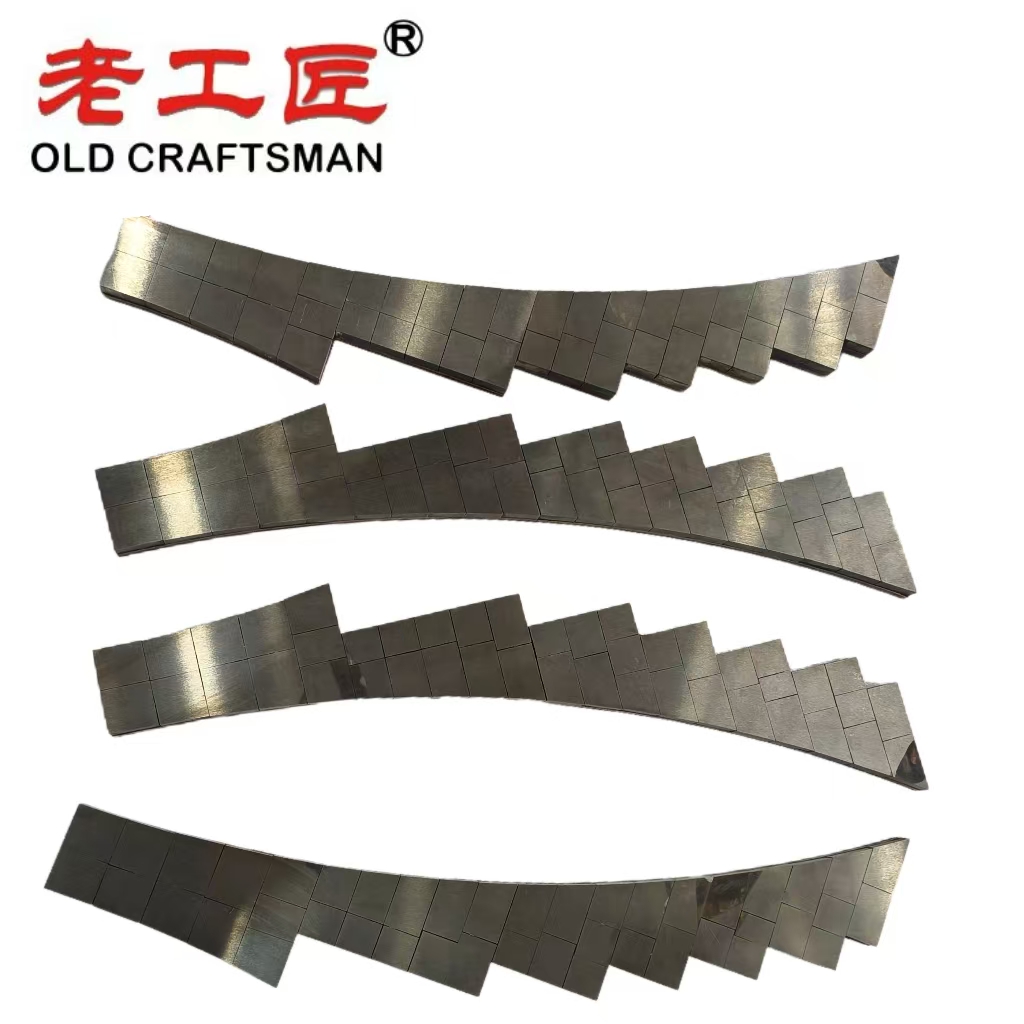
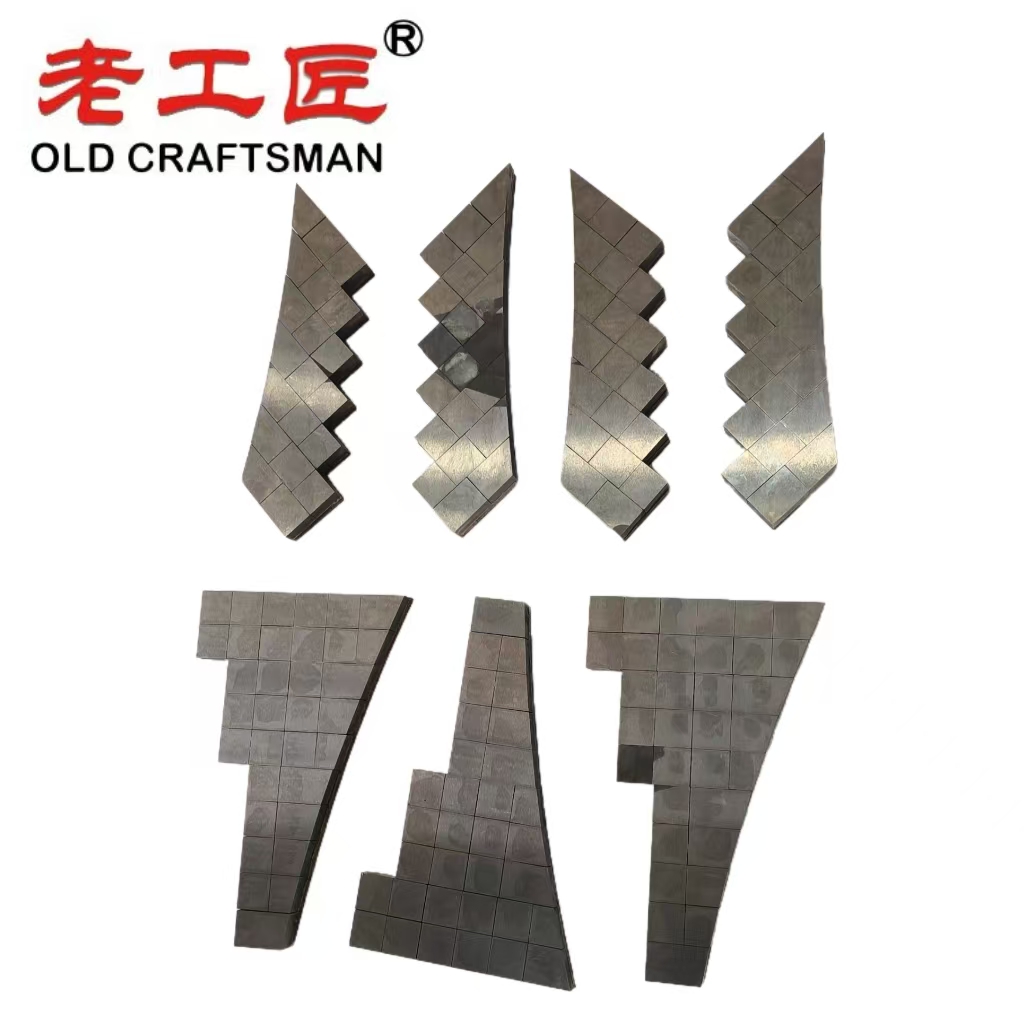
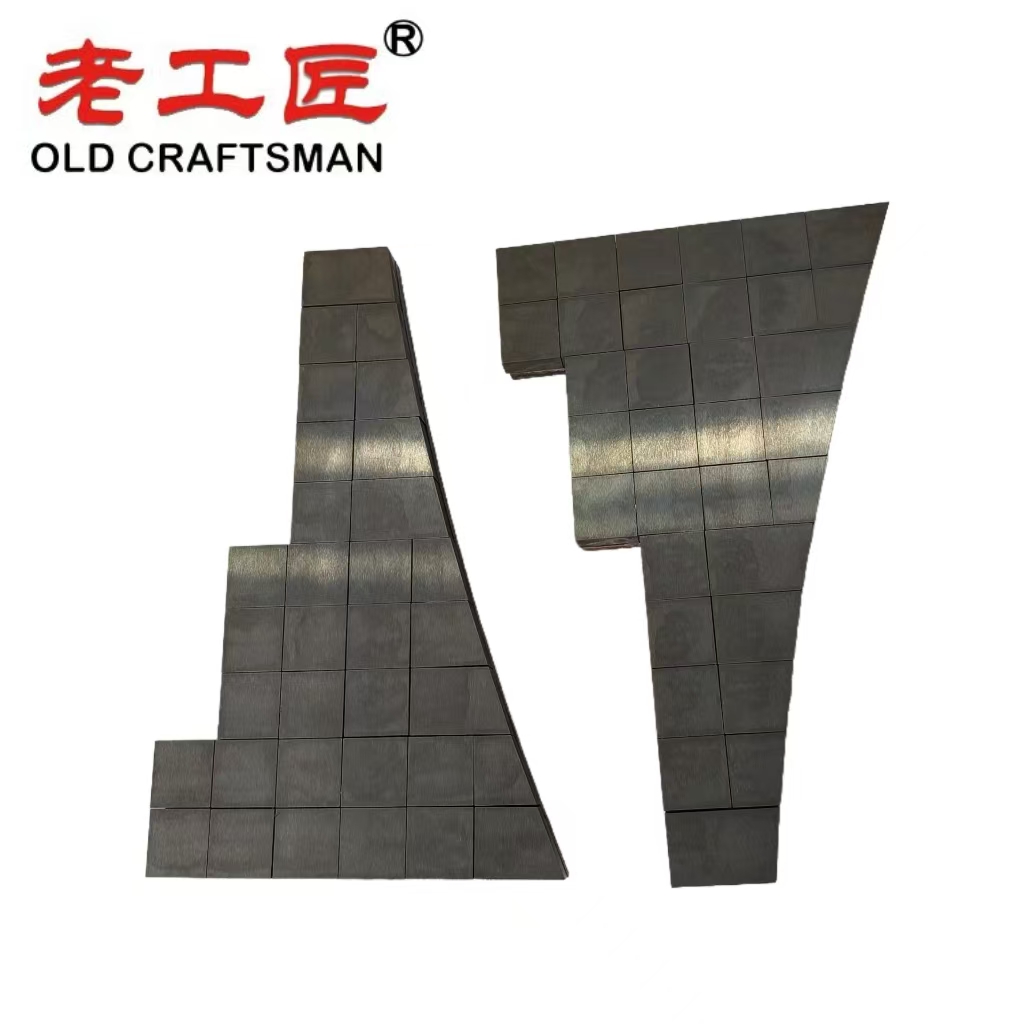
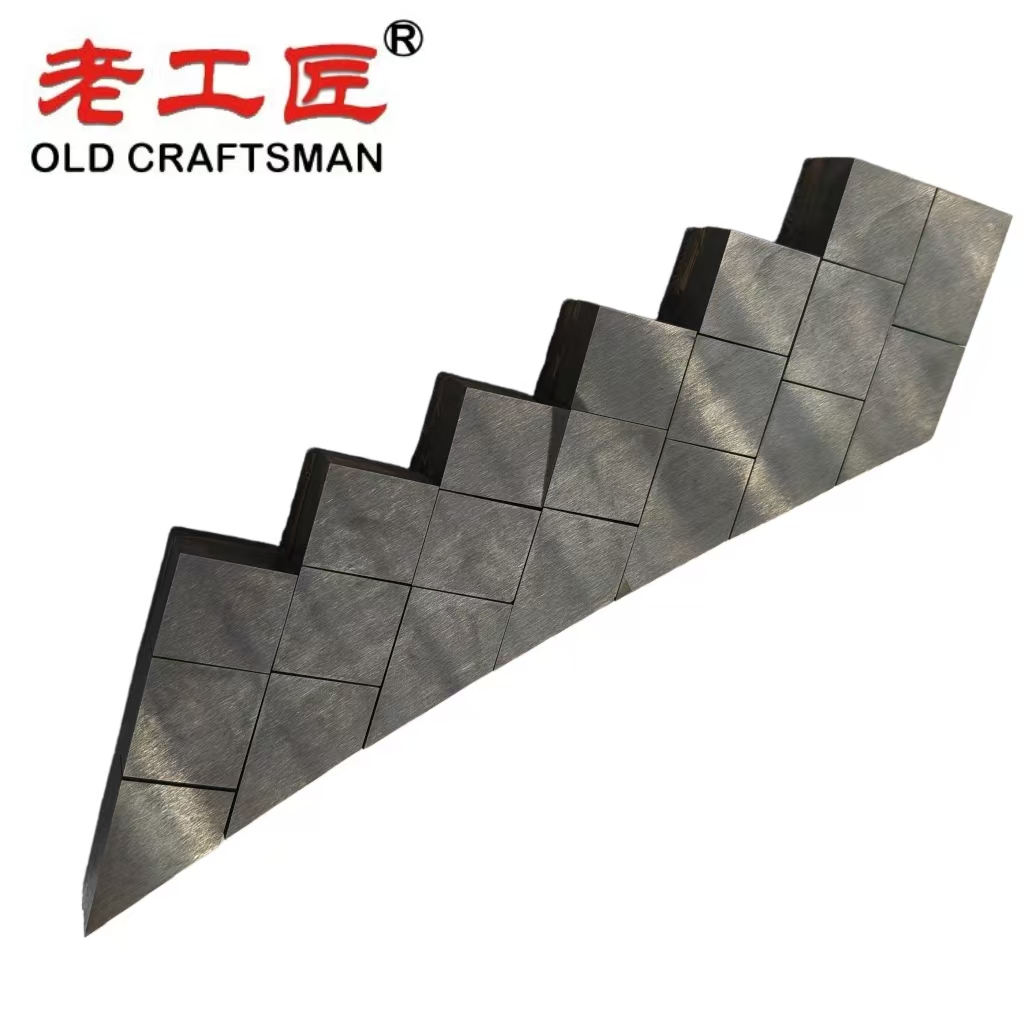